Zirconium, a versatile and robust metal, has gained significant attention in various industries due to its unique properties. When it comes to working with zirconium, particularly in the form of a 5mm bar, questions often arise regarding its weldability and machinability. This blog post delves into the intricacies of welding and machining 5mm zirconium bars, exploring the possibilities, challenges, and best practices associated with these processes.
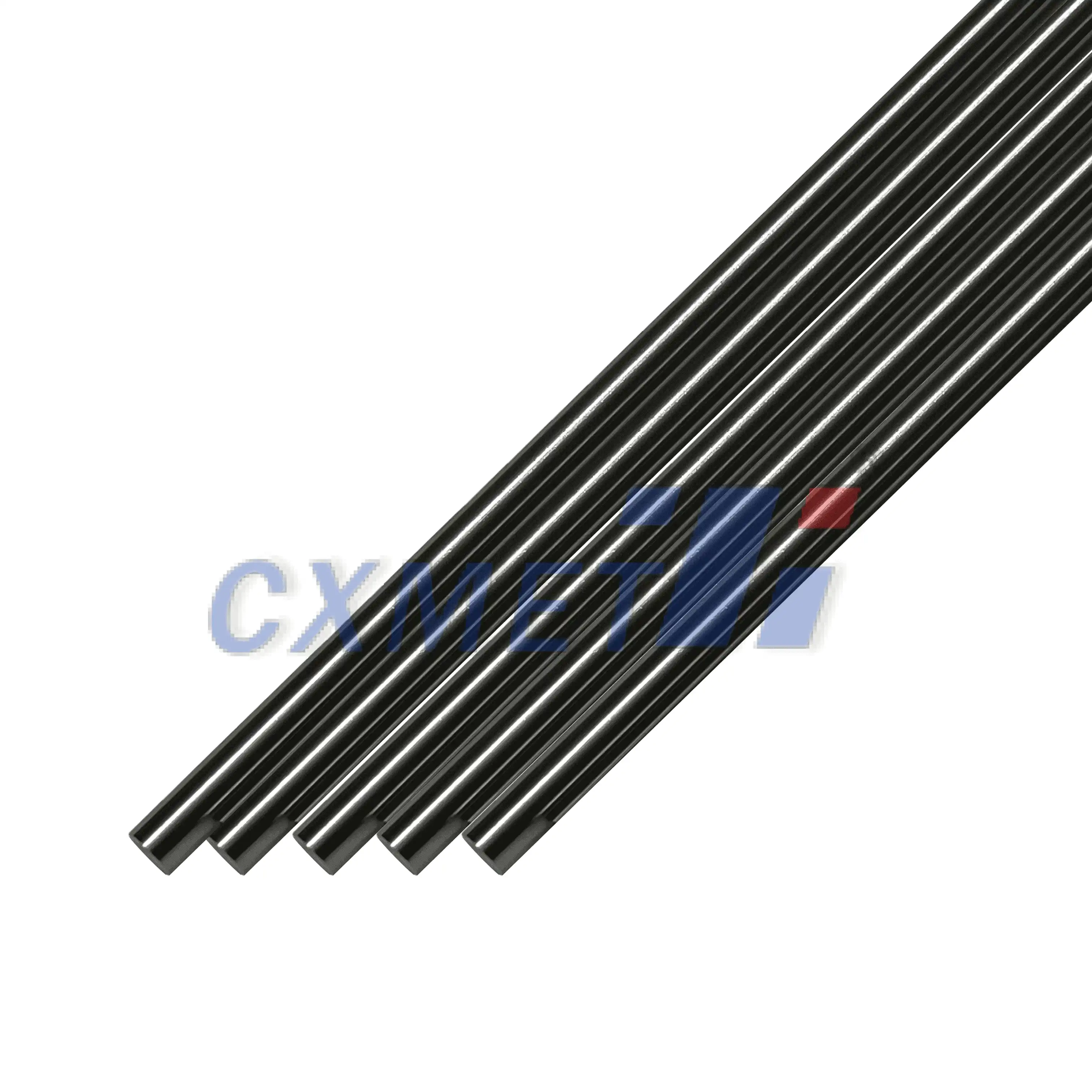
What are the best welding techniques for 5mm zirconium bars?
Welding zirconium bars, especially those with a 5mm diameter, requires careful consideration and specialized techniques. The reactive nature of zirconium with atmospheric gases at high temperatures necessitates stringent control over the welding environment. Here are some of the most effective welding techniques for 5mm zirconium bars:
- Gas Tungsten Arc Welding (GTAW): Also known as TIG welding, this method is widely preferred for zirconium due to its precision and ability to produce high-quality welds. When welding 5mm zirconium bars, GTAW allows for excellent control over the heat input, reducing the risk of contamination and ensuring a clean, strong weld. The process typically involves using pure argon as a shielding gas to prevent oxidation.
- Electron Beam Welding (EBW): This advanced welding technique is particularly suitable for zirconium bars of smaller diameters, such as 5mm. EBW offers the advantage of a highly focused heat source, minimizing the heat-affected zone and reducing the risk of distortion. The process is carried out in a vacuum, which eliminates the need for shielding gas and provides an ultra-clean welding environment, crucial for maintaining zirconium's integrity.
- Laser Beam Welding: Similar to EBW, laser welding provides a highly concentrated heat source, making it suitable for precision welding of 5mm zirconium bars. This method offers good control over the weld penetration and can be performed with minimal heat input, reducing the potential for thermal distortion.
Regardless of the chosen technique, welding zirconium requires meticulous preparation and execution. The welding area must be thoroughly cleaned to remove any surface contaminants that could compromise the weld quality. Additionally, the use of high-purity shielding gases (typically argon) is crucial to prevent atmospheric contamination during the welding process.
It's worth noting that the success of welding 5mm zirconium bars also depends on the specific grade of zirconium being used. Some zirconium alloys may exhibit better weldability than others, and the welding parameters may need to be adjusted accordingly. Consulting with materials specialists or conducting trial welds on sample pieces is often recommended to determine the optimal welding parameters for a specific zirconium grade and application.
How can 5mm zirconium bars be effectively machined?
Machining 5mm zirconium bars presents unique challenges due to the material's properties, but with the right approaches and tools, it can be accomplished effectively. Here are some key considerations and techniques for machining 5mm zirconium bars:
- Cutting Tools: When machining zirconium, it's crucial to use sharp, high-quality cutting tools. Carbide tools are often preferred due to their hardness and wear resistance. For 5mm bars, micro-grain carbide tools can provide the precision needed for small-diameter workpieces.
- Cooling and Lubrication: Proper cooling is essential when machining zirconium to prevent overheating and potential ignition. Flood coolants or high-pressure coolant systems are recommended. Water-soluble coolants are often used, but it's important to ensure they don't contain chlorine, which can cause stress corrosion cracking in zirconium.
- Cutting Speed and Feed Rate: For 5mm zirconium bars, relatively low cutting speeds and moderate feed rates are typically recommended. This helps to minimize heat generation and reduce the risk of tool wear. The exact parameters will depend on the specific machining operation and the grade of zirconium being worked with.
- Depth of Cut: When working with small-diameter bars like 5mm zirconium, it's important to take light cuts to avoid excessive deflection or vibration. Multiple passes with shallow depths of cut can help achieve the desired dimensions while maintaining precision.
- Machine Rigidity: Given the small diameter of 5mm zirconium bars, using rigid machine setups is crucial to minimize vibration and ensure accurate machining. This may involve using tailstock support for longer bars or specialized workholding solutions for shorter pieces.
Various machining operations can be performed on 5mm zirconium bars, including turning, milling, drilling, and threading. However, each operation requires careful consideration of the tools and parameters used:
- Turning: When turning 5mm zirconium bars, use sharp carbide tools with positive rake angles. Continuous cutting is preferred over interrupted cutting to reduce the risk of work hardening.
- Milling: For milling operations on small zirconium bars, end mills with multiple flutes can provide good results. Climb milling is often preferred to conventional milling to reduce work hardening.
- Drilling: When drilling 5mm zirconium bars, use sharp drill bits with a point angle of around 118°. Peck drilling techniques can help with chip evacuation and prevent heat buildup.
- Threading: Threading 5mm zirconium bars requires careful control of cutting forces. Single-point threading tools or thread milling can be effective, depending on the thread specifications.
It's important to note that machining zirconium produces fine, pyrophoric chips that can ignite spontaneously. Proper chip management and disposal procedures must be in place to ensure safety during machining operations.
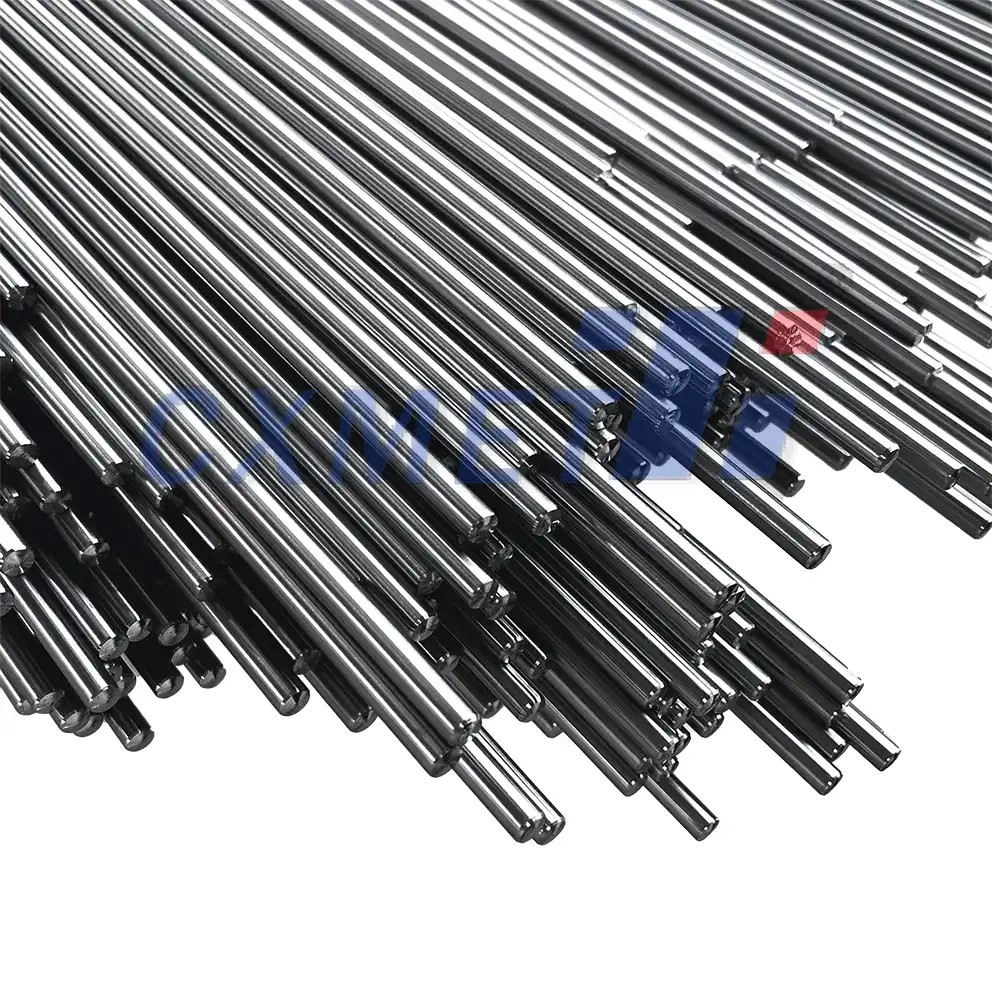
What are the key considerations for handling and storing 5mm zirconium bars?
Proper handling and storage of 5mm zirconium bars are crucial for maintaining their integrity and ensuring safety in the workplace. Here are some key considerations:
- Fire Safety: Zirconium in fine particle form, such as chips or dust, can be pyrophoric. While solid 5mm bars are generally stable, care should be taken to prevent the accumulation of fine particles during handling or machining. Proper cleaning and disposal procedures for zirconium waste should be implemented.
- Contamination Prevention: Zirconium is highly reactive with certain elements, particularly at elevated temperatures. Store 5mm zirconium bars in a clean, dry environment away from potential contaminants. Avoid contact with materials containing halogens (chlorine, fluorine, etc.) as these can cause stress corrosion cracking.
- Temperature Control: While 5mm zirconium bars are stable at room temperature, avoid storing them in areas with extreme temperature fluctuations or high humidity, as this can affect surface quality over time.
- Handling Precautions: When handling 5mm zirconium bars, use clean gloves to prevent contamination from skin oils or other substances. Avoid dropping or impacting the bars, as zirconium can be brittle and may chip or crack under sudden stress.
- Inventory Management: Implement a proper inventory system to track the grade, batch, and history of 5mm zirconium bars. This is particularly important in industries with strict material traceability requirements, such as aerospace or nuclear applications.
- Transportation: When transporting 5mm zirconium bars, ensure they are securely packaged to prevent movement or damage. For longer bars, use appropriate support to prevent bending or warping during transit.
- Environmental Considerations: While zirconium is generally considered non-toxic, follow proper disposal procedures for any waste material, including machining chips or coolant contaminated with zirconium particles.
In industrial settings where 5mm zirconium bars are regularly used, it's advisable to develop specific handling and storage protocols tailored to the facility's needs and the particular applications of the zirconium. This may include designated storage areas, specialized handling equipment, and training programs for personnel working with zirconium materials.
By adhering to these handling and storage considerations, you can help ensure the longevity and quality of 5mm zirconium bars while maintaining a safe working environment. Proper care in handling and storage not only preserves the material's properties but also contributes to the overall efficiency and safety of operations involving zirconium.
Conclusion
Working with 5mm zirconium bars requires a comprehensive understanding of the material's properties and the appropriate techniques for welding and machining. While challenges exist, the unique characteristics of zirconium make it a valuable material in various industries. By employing the right methods and taking necessary precautions, 5mm zirconium bars can be effectively welded, machined, and handled to meet diverse application requirements. As technology advances, we can expect even more refined techniques for working with this versatile metal, opening up new possibilities for its use in cutting-edge applications.
At SHAANXI CXMET TECHNOLOGY CO., LTD, we take pride in our extensive product range, which caters to diverse customer needs. Our company is equipped with outstanding production and processing capabilities, ensuring the high quality and precision of our products. We are committed to innovation and continuously strive to develop new products, keeping us at the forefront of our industry. With leading technological development capabilities, we are able to adapt and evolve in a rapidly changing market. Furthermore, we offer customized solutions to meet the specific requirements of our clients. If you are interested in our products or wish to learn more about the intricate details of our offerings, please do not hesitate to contact us at sales@cxmet.com. Our team is always ready to assist you.
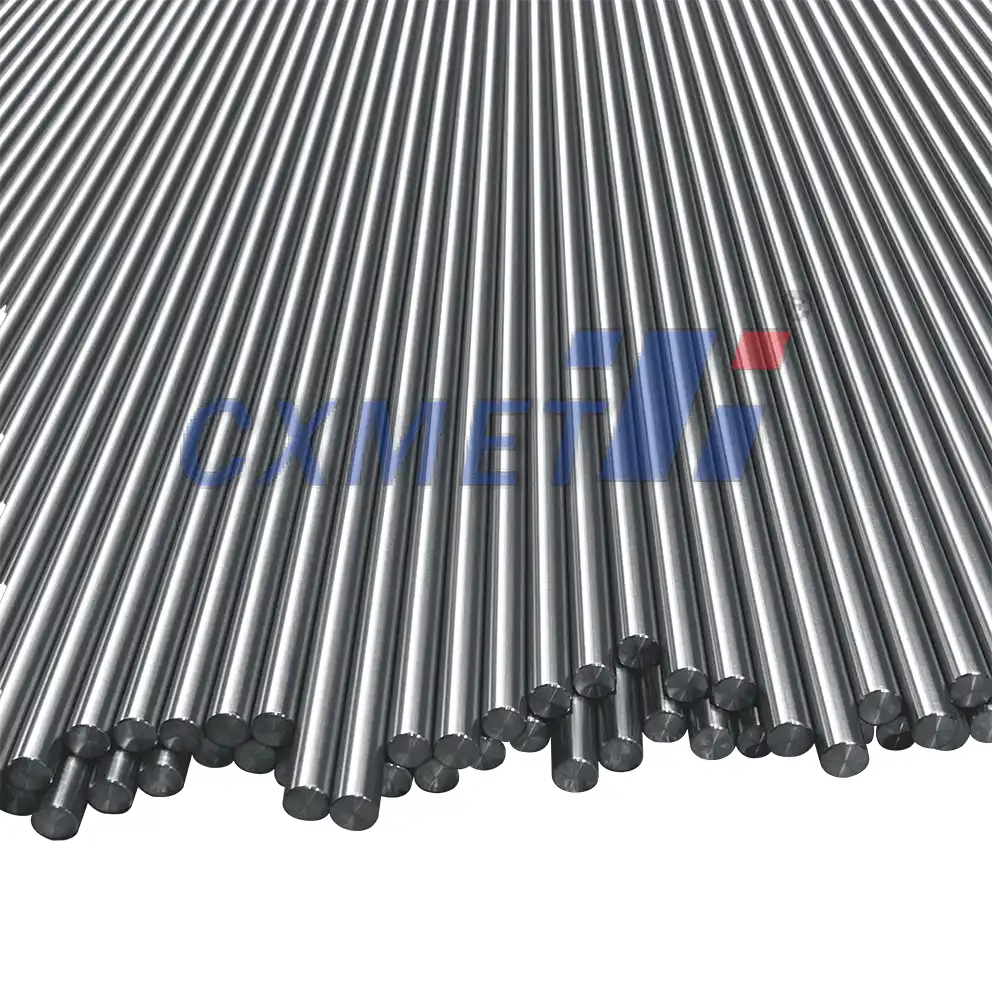
References
1. ASM International. (2006). ASM Handbook, Volume 6: Welding, Brazing, and Soldering. Materials Park, OH: ASM International.
2. Garverick, L. (1994). Corrosion in the Petrochemical Industry. ASM International.
3. Gupta, C. K., & Sathiyamoorthy, D. (2013). Fluid Bed Technology in Materials Processing. CRC Press.
4. Holleman, A. F., Wiberg, E., & Wiberg, N. (2001). Inorganic Chemistry. Academic Press.
5. Kalpakjian, S., & Schmid, S. R. (2014). Manufacturing Engineering and Technology. Pearson.
6. Leyens, C., & Peters, M. (Eds.). (2006). Titanium and Titanium Alloys: Fundamentals and Applications. John Wiley & Sons.