Gr11 titanium wire, also known as Grade 11 titanium wire, is a high-performance material that has gained significant attention in various industrial applications. This alloy combines the excellent properties of titanium with enhanced strength and corrosion resistance, making it a popular choice for demanding environments. In this blog post, we will explore the potential of the product in industrial settings and answer some frequently asked questions about its use.
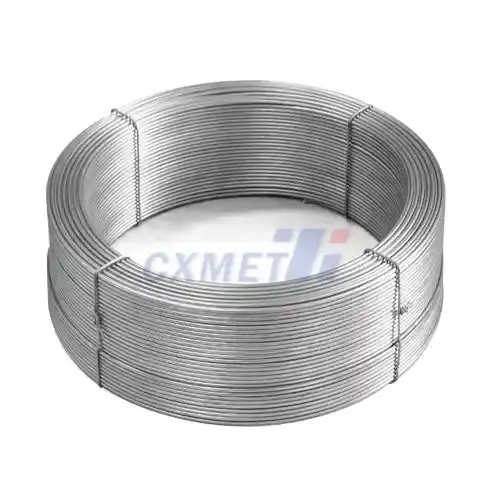
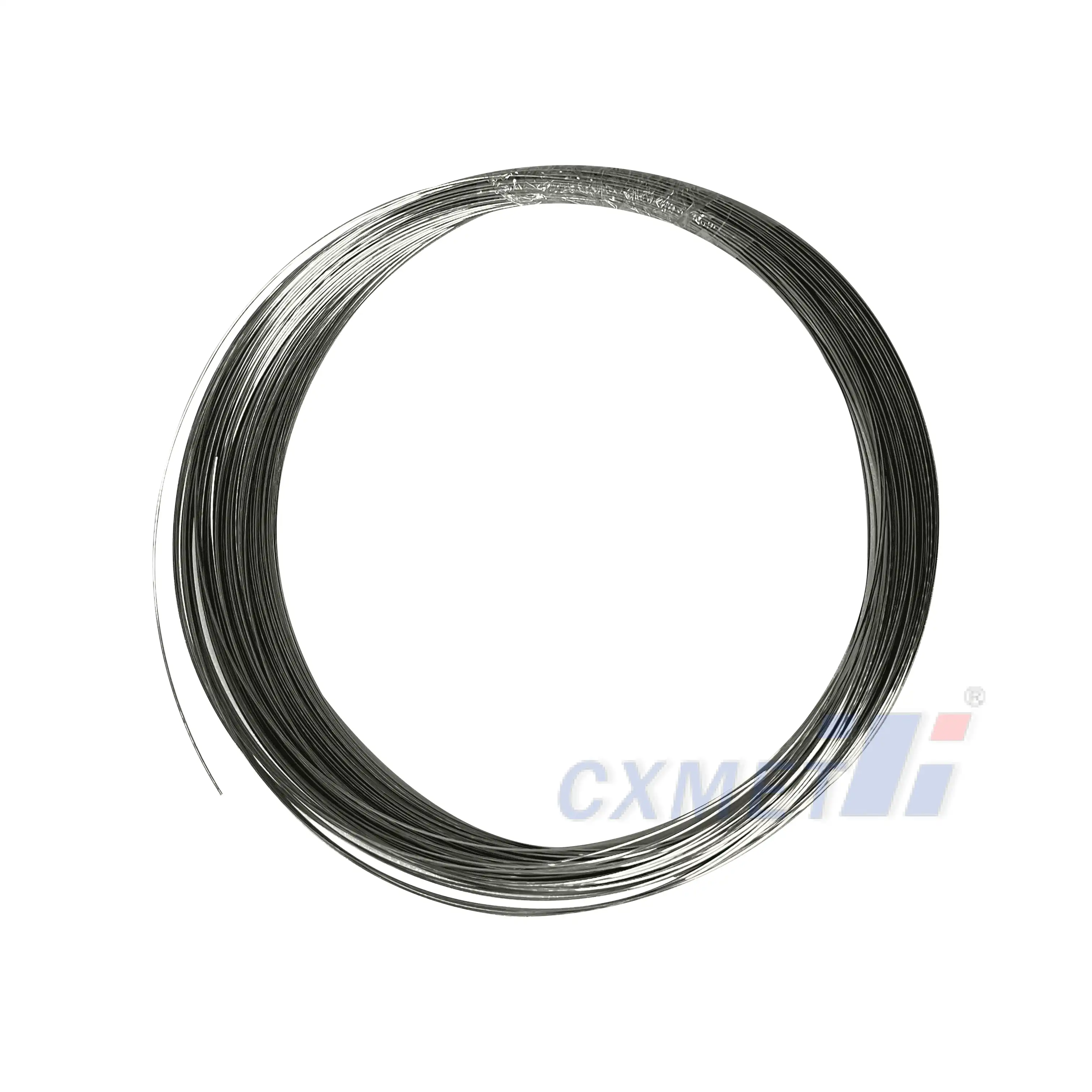
What are the key properties of Gr11 titanium wire?
Gr11 titanium wire possesses a unique combination of properties that make it highly desirable for industrial applications. Some of the key characteristics include:
- Exceptional strength-to-weight ratio: Gr11 titanium wire offers an impressive strength-to-weight ratio, making it ideal for applications where weight reduction is crucial without compromising on strength. This property is particularly beneficial in aerospace, automotive, and marine industries where lightweight yet strong materials are essential.
- Superior corrosion resistance: One of the standout features of Gr11 titanium wire is its excellent corrosion resistance. It can withstand harsh chemical environments, saltwater, and other corrosive substances that would quickly degrade many other metals. This makes it an excellent choice for use in chemical processing plants, offshore oil rigs, and marine applications.
- High temperature resistance: Gr11 titanium wire maintains its strength and structural integrity at elevated temperatures, making it suitable for use in high-temperature industrial processes. This property is particularly valuable in applications such as heat exchangers, furnace components, and exhaust systems.
- Biocompatibility: Although not directly related to industrial environments, it's worth noting that Gr11 titanium wire is biocompatible. This property opens up possibilities for its use in medical and pharmaceutical industries, where contact with biological tissues may be necessary.
- Low thermal expansion: Gr11 titanium wire has a low coefficient of thermal expansion, which means it maintains its dimensional stability across a wide range of temperatures. This property is crucial in applications where precise tolerances must be maintained, such as in aerospace components or precision instruments.
These properties, combined with its excellent formability and weldability, make it a versatile material for various industrial applications. Its ability to withstand extreme conditions while maintaining its structural integrity makes it an attractive option for engineers and designers working on projects that require high-performance materials.
How does Gr11 titanium wire compare to other industrial materials?
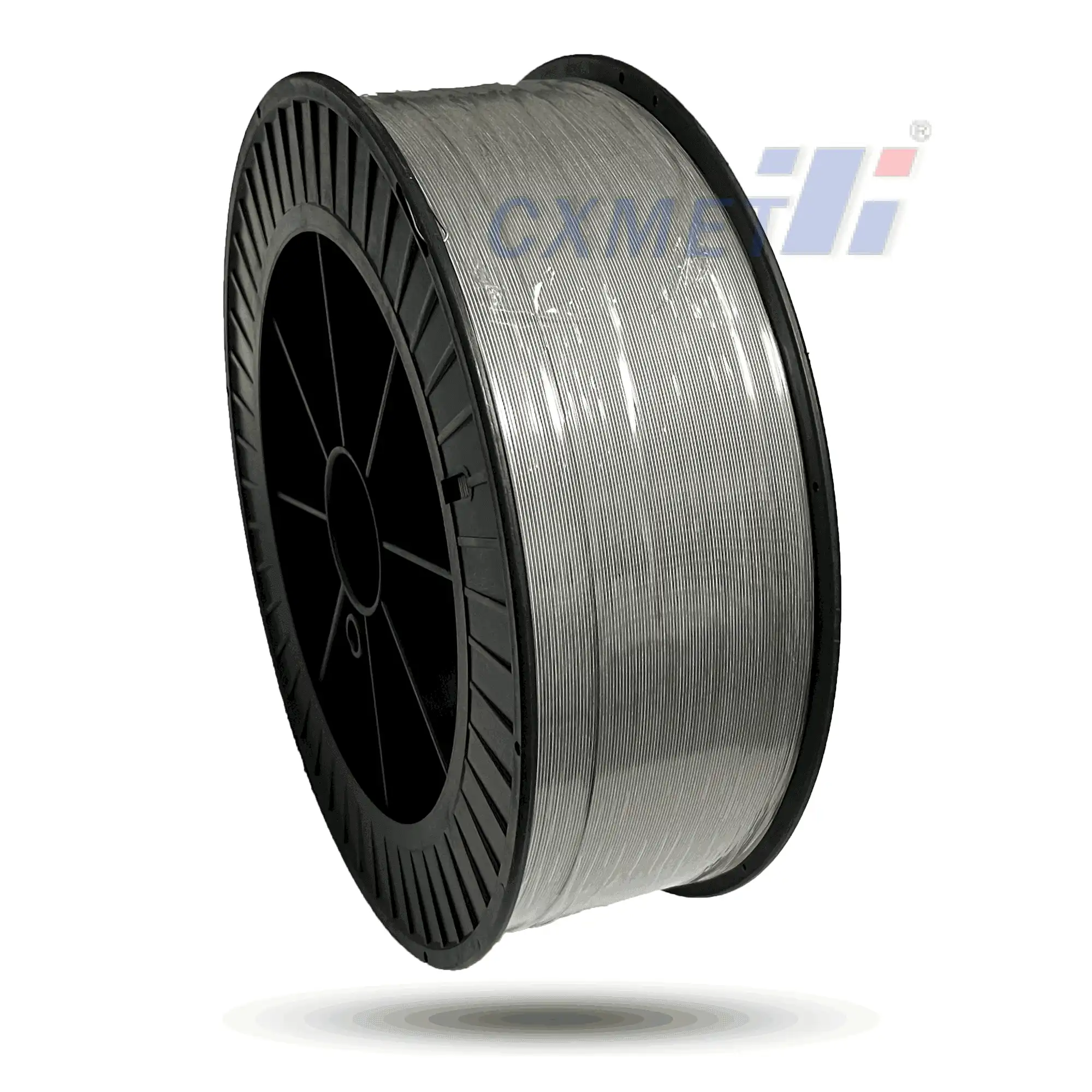
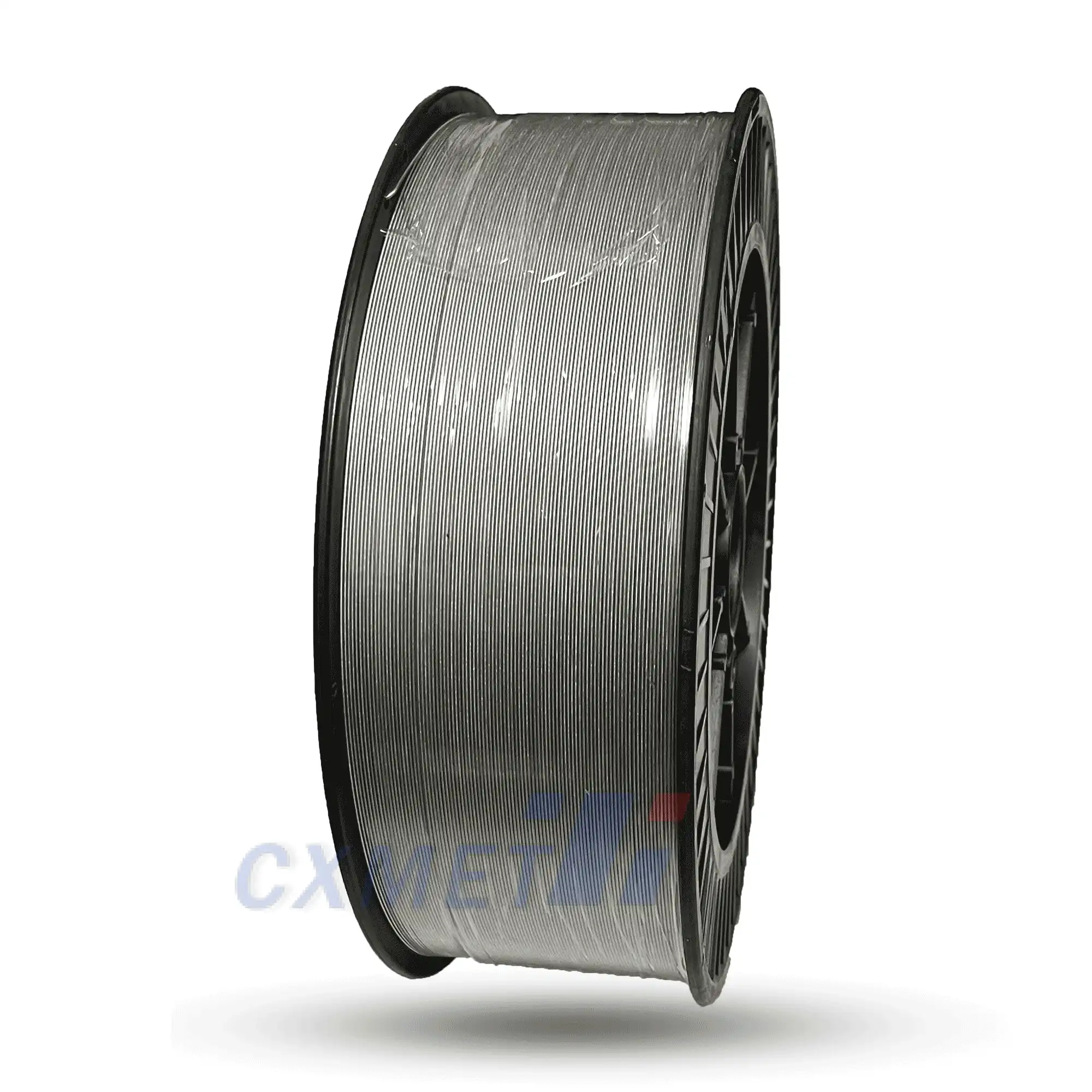
When considering materials for industrial applications, it's essential to compare Gr11 titanium wire with other commonly used materials to understand its advantages and potential limitations. Here's a comparison of Gr11 titanium wire with some other industrial materials:
- Stainless Steel: While stainless steel is widely used in industrial settings due to its corrosion resistance and strength, Gr11 titanium wire offers several advantages. Titanium has a higher strength-to-weight ratio, making it more suitable for applications where weight reduction is critical. Additionally, titanium's corrosion resistance surpasses that of most stainless steel grades, especially in harsh chemical environments and seawater.
- Aluminum: Aluminum is known for its lightweight properties and is often used in aerospace and automotive industries. However, Gr11 titanium wire offers superior strength and temperature resistance compared to aluminum. In applications where high strength and corrosion resistance are required, titanium outperforms aluminum.
- Nickel alloys: Nickel alloys, such as Inconel, are known for their high-temperature performance and corrosion resistance. While these alloys perform well in extreme environments, Gr11 titanium wire often provides a better strength-to-weight ratio and is more resistant to stress corrosion cracking in certain environments.
- Carbon fiber composites: In recent years, carbon fiber composites have gained popularity in industrial applications due to their high strength-to-weight ratio. While carbon fiber excels in certain areas, Gr11 titanium wire offers better temperature resistance, easier repairability, and superior impact resistance.
When comparing Gr11 titanium wire to these materials, it's important to consider the specific requirements of the application. Factors such as operating temperature, chemical exposure, weight constraints, and cost all play a role in material selection. In many cases, Gr11 titanium wire offers a unique combination of properties that make it the ideal choice for challenging industrial environments.
It's worth noting that while Gr11 titanium wire may have a higher initial cost compared to some other materials, its long-term performance and durability often result in lower lifecycle costs. The extended service life and reduced maintenance requirements can offset the higher upfront investment, especially in critical applications where failure is not an option.
What are the main industrial applications for Gr11 titanium wire?
Gr11 titanium wire finds applications across a wide range of industries due to its exceptional properties. Some of the main industrial applications include:
- Aerospace: In the aerospace industry, it is used in the manufacture of aircraft components such as hydraulic systems, engine parts, and structural elements. Its high strength-to-weight ratio and excellent fatigue resistance make it ideal for applications where weight reduction and reliability are crucial.
- Chemical Processing: The corrosion resistance of it makes it an excellent choice for use in chemical processing plants. It is used in the construction of heat exchangers, reaction vessels, and piping systems that handle corrosive chemicals.
- Oil and Gas: In the oil and gas industry, Gr11 titanium wire is used in offshore drilling equipment, subsea components, and pipeline systems. Its resistance to corrosion in saltwater environments and high strength make it suitable for these demanding applications.
- Marine Engineering: The marine industry utilizes Gr11 titanium wire in the construction of ship propellers, pumps, valves, and other components exposed to seawater. Its corrosion resistance and high strength-to-weight ratio make it an excellent choice for marine applications.
- Power Generation: In power plants, Gr11 titanium wire is used in heat exchangers, condensers, and turbine components. Its ability to withstand high temperatures and resist corrosion in various coolants makes it valuable in this industry.
- Medical and Pharmaceutical: Although not strictly industrial, it's worth mentioning that Gr11 titanium wire is used in the manufacture of medical implants, surgical instruments, and pharmaceutical processing equipment due to its biocompatibility and corrosion resistance.
- Automotive: In the automotive industry, Gr11 titanium wire is used in high-performance applications such as exhaust systems, suspension components, and racing car parts where weight reduction and high strength are essential.
- Desalination Plants: The corrosion resistance of it makes it an excellent material for use in desalination plants, where it is used in heat exchangers and other components exposed to saltwater.
In these applications, Gr11 titanium wire offers several advantages over traditional materials. Its use often results in lighter, more durable components that can withstand harsh environments and operate reliably for extended periods. This leads to improved performance, reduced maintenance requirements, and longer service life for industrial equipment and systems.
It's important to note that the selection of Gr11 titanium wire for any specific application should be based on a thorough analysis of the operating conditions, performance requirements, and economic considerations. While its properties make it suitable for a wide range of industrial uses, proper design and manufacturing processes are crucial to fully leverage its benefits.
In conclusion, Gr11 titanium wire is indeed a versatile and high-performance material that can be effectively used in various industrial environments. Its unique combination of properties, including high strength-to-weight ratio, excellent corrosion resistance, and temperature stability, make it an attractive option for applications where traditional materials may fall short. As industries continue to push the boundaries of performance and efficiency, materials like Gr11 titanium wire will play an increasingly important role in enabling new technologies and improving existing systems.
At SHAANXI CXMET TECHNOLOGY CO., LTD, we take pride in our extensive product range, which caters to diverse customer needs. Our company is equipped with outstanding production and processing capabilities, ensuring the high quality and precision of our products. We are committed to innovation and continuously strive to develop new products, keeping us at the forefront of our industry. With leading technological development capabilities, we are able to adapt and evolve in a rapidly changing market. Furthermore, we offer customized solutions to meet the specific requirements of our clients. If you are interested in our products or wish to learn more about the intricate details of our offerings, please do not hesitate to contact us at sales@cxmet.com. Our team is always ready to assist you.
References
- ASTM International. (2021). ASTM B863-14 Standard Specification for Titanium and Titanium Alloy Wire.
- Lutjering, G., & Williams, J. C. (2007). Titanium (2nd ed.). Springer-Verlag Berlin Heidelberg.
- Leyens, C., & Peters, M. (Eds.). (2003). Titanium and Titanium Alloys: Fundamentals and Applications. Wiley-VCH.
- Boyer, R., Welsch, G., & Collings, E. W. (1994). Materials Properties Handbook: Titanium Alloys. ASM International.
- Donachie, M. J. (2000). Titanium: A Technical Guide (2nd ed.). ASM International.
- Peters, M., Kumpfert, J., Ward, C. H., & Leyens, C. (2003). Titanium Alloys for Aerospace Applications. Advanced Engineering Materials, 5(6), 419-427.
- Schutz, R. W., & Watkins, H. B. (1998). Recent developments in titanium alloy application in the energy industry. Materials Science and Engineering: A, 243(1-2), 305-315.
- Yamada, M. (1996). An overview on the development of titanium alloys for non-aerospace application in Japan. Materials Science and Engineering: A, 213(1-2), 8-15.
- Rack, H. J., & Qazi, J. I. (2006). Titanium alloys for biomedical applications. Materials Science and Engineering: C, 26(8), 1269-1277.
- Faller, K., & Froes, F. H. (2001). The use of titanium in family automobiles: Current trends. JOM, 53(4), 27-28.