Grade 3 titanium wire, known for its excellent corrosion resistance and moderate strength, is a popular choice in various industries. Many manufacturers and engineers often wonder about the possibilities of welding or machining this versatile material. In this blog post, we'll explore the weldability and machinability of Gr3 titanium wire, discussing its properties, applications, and the best practices for working with this material.
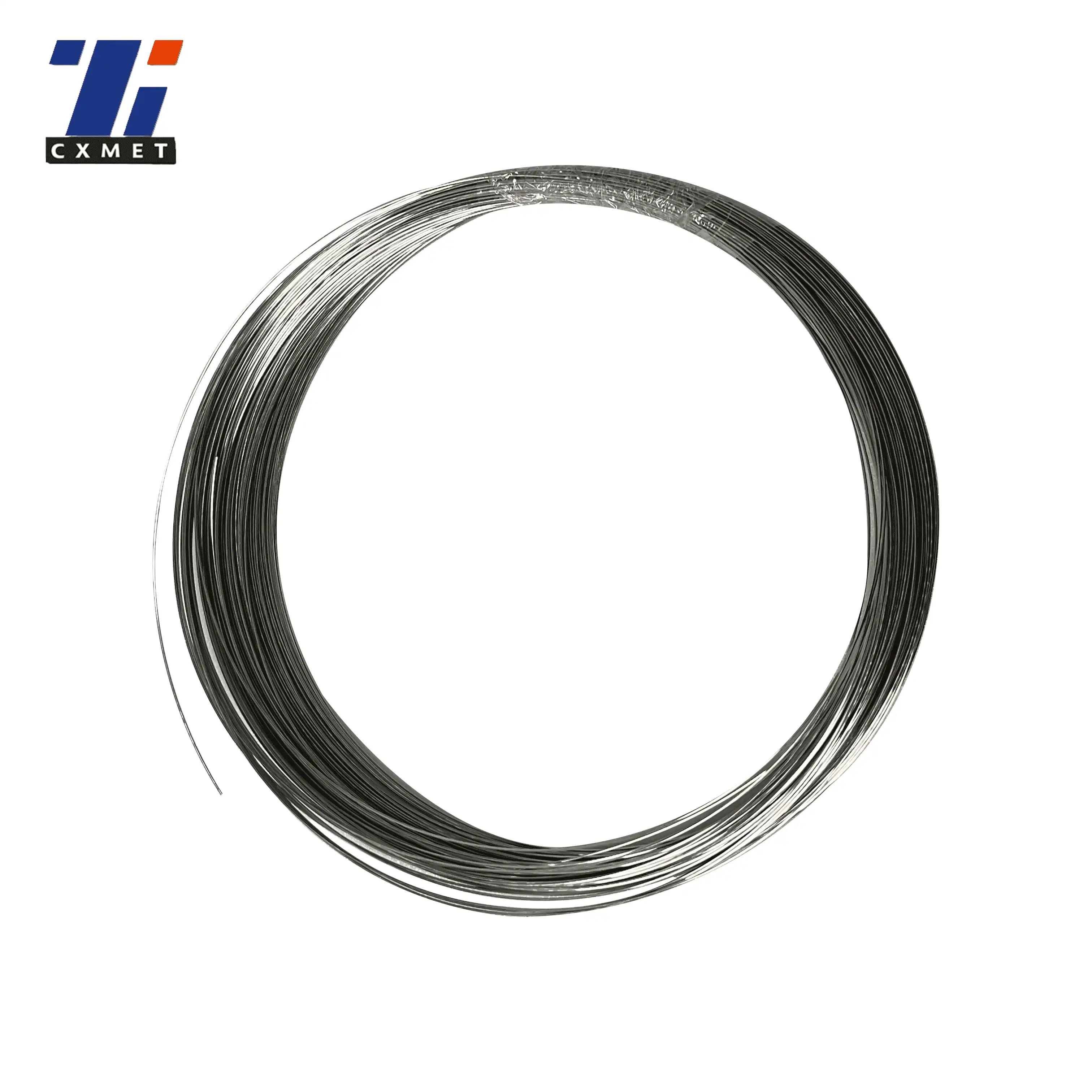
What are the properties of Grade 3 titanium wire?
Gr3 titanium wire is a commercially pure titanium alloy with a unique set of properties that make it suitable for various applications. Its chemical composition typically includes a minimum of 99.1% titanium, with small amounts of other elements such as iron, carbon, nitrogen, hydrogen, and oxygen. These trace elements contribute to the wire's specific characteristics and performance.
Some key properties of Grade 3 titanium wire include:
- Excellent corrosion resistance: Grade 3 titanium wire exhibits exceptional resistance to corrosion in various environments, including seawater, acids, and industrial chemicals. This property makes it ideal for marine applications and chemical processing equipment.
- Moderate strength: While not as strong as some higher-grade titanium alloys, Grade 3 titanium wire offers a good balance of strength and ductility. It has a typical tensile strength range of 380-550 MPa (55-80 ksi) and a yield strength of 275-450 MPa (40-65 ksi).
- Low density: With a density of approximately 4.51 g/cm³, Grade 3 titanium wire is significantly lighter than steel, making it an excellent choice for weight-sensitive applications.
- Biocompatibility: Grade 3 titanium is considered biocompatible, making it suitable for medical and dental applications where contact with human tissue is required.
- Good formability: The wire can be easily formed and shaped into various configurations, allowing for versatility in manufacturing processes.
These properties contribute to the wire's suitability for welding and machining, which we'll explore in more detail in the following sections.
How does welding affect the properties of Gr3 titanium wire?
Welding Grade 3 titanium wire can have significant effects on its properties, and understanding these changes is crucial for ensuring the integrity and performance of the welded components. The welding process introduces heat and potential contaminants, which can alter the microstructure and chemical composition of the titanium wire.
Effects of welding on Gr3 titanium wire properties:
- Grain growth: The heat from welding can cause grain growth in the heat-affected zone (HAZ) of the titanium wire. This can lead to a reduction in strength and an increase in ductility in the welded area.
- Oxidation: Titanium is highly reactive with oxygen at elevated temperatures. During welding, if proper shielding is not maintained, oxygen can diffuse into the metal, forming a brittle layer known as "alpha case." This can significantly reduce the ductility and fatigue resistance of the welded joint.
- Contamination: Titanium is sensitive to contamination from elements such as carbon, nitrogen, and hydrogen. These contaminants can be introduced during the welding process if proper precautions are not taken, leading to embrittlement of the weld.
- Residual stress: The rapid heating and cooling during welding can induce residual stresses in the material, potentially affecting the dimensional stability and fatigue performance of the welded component.
- Phase transformation: Although less pronounced in Grade 3 titanium compared to higher-grade alloys, the heat from welding can cause localized phase transformations, potentially altering the mechanical properties in the weld zone.
To mitigate these effects and maintain the desired properties of Grade 3 titanium wire after welding, several best practices should be followed:
- Use proper shielding gas: Inert gases such as argon or helium should be used to protect the weld pool and surrounding area from atmospheric contamination.
- Clean thoroughly: Ensure that the surfaces to be welded are free from contaminants, oils, and oxides before welding.
- Control heat input: Minimize heat input to reduce grain growth and the extent of the heat-affected zone.
- Post-weld heat treatment: In some cases, post-weld heat treatment may be necessary to relieve residual stresses and optimize the microstructure of the welded joint.
- Use appropriate filler material: When required, use filler material that is compatible with Grade 3 titanium to maintain the desired properties of the base material.
By carefully controlling the welding process and following these best practices, it is possible to weld Grade 3 titanium wire while minimizing adverse effects on its properties. However, it's important to note that welded joints may still have slightly different characteristics compared to the base material, and this should be taken into account in the design and application of welded components.
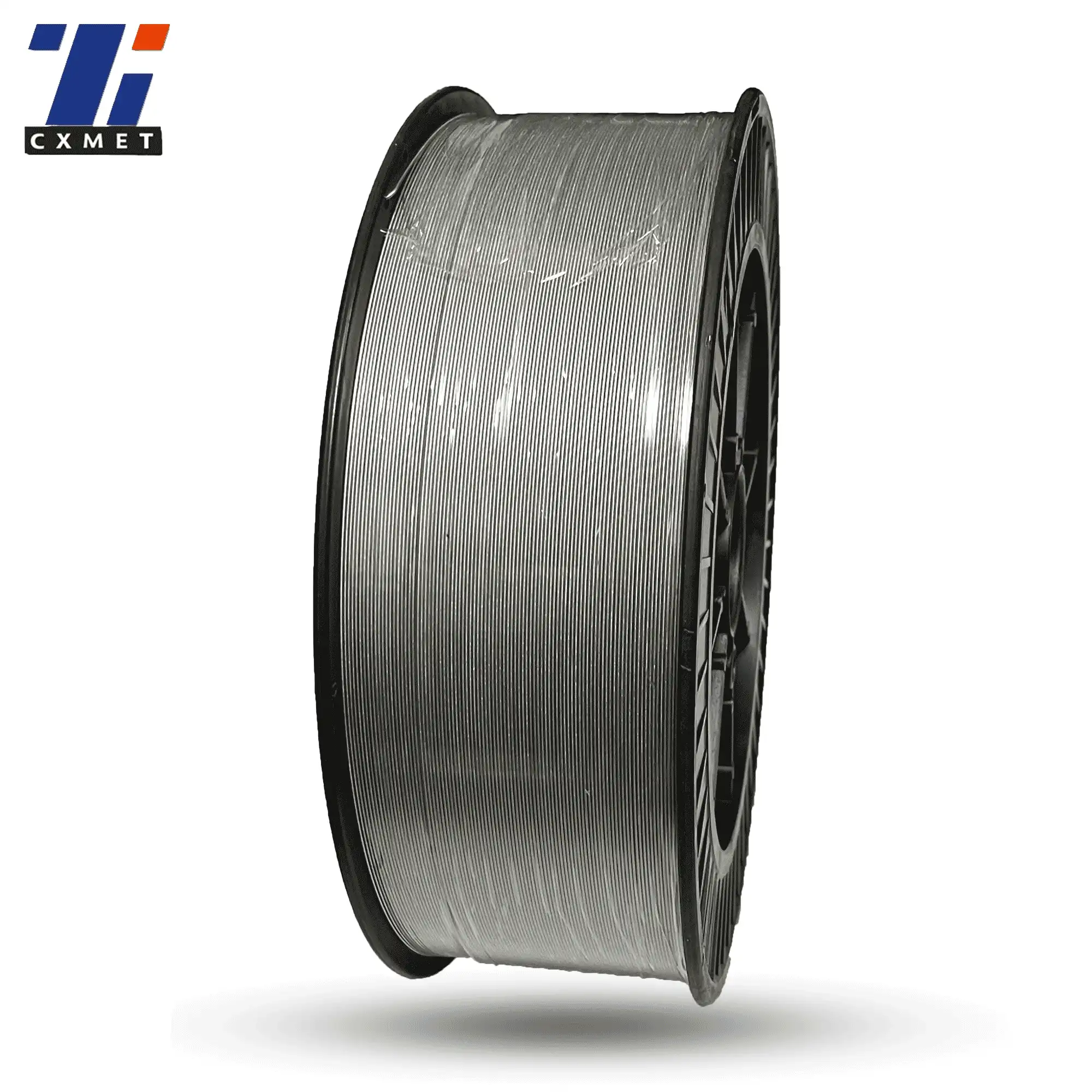
What are the best machining techniques for Gr3 titanium wire?
Machining Grade 3 titanium wire requires careful consideration of its unique properties and characteristics. While titanium is known for its excellent strength-to-weight ratio and corrosion resistance, it can be challenging to machine due to its low thermal conductivity, high chemical reactivity, and tendency to work harden. However, with the right techniques and tools, Gr3 titanium wire can be successfully machined for various applications.
Best machining techniques for Gr3 titanium wire:
- Cutting speed and feed rate:
- Use lower cutting speeds compared to steel or aluminum. Typical cutting speeds for Grade 3 titanium range from 30 to 60 m/min (100 to 200 ft/min).
- Maintain higher feed rates to minimize work hardening and heat buildup. This helps to keep the cutting edge engaged and reduces the time the tool is in contact with the workpiece.
- Tool selection:
- Use sharp, rigid cutting tools with positive rake angles to reduce cutting forces and heat generation.
- Carbide tools are generally preferred for their hardness and wear resistance. Coated carbide tools, particularly those with TiAlN or TiCN coatings, can provide improved performance and tool life.
- For certain operations, polycrystalline diamond (PCD) tools may be beneficial due to their high hardness and thermal conductivity.
- Cooling and lubrication:
- Use abundant coolant to dissipate heat and flush away chips. High-pressure coolant delivery systems can be particularly effective.
- Water-soluble or synthetic coolants are often preferred over oil-based ones to prevent potential contamination of the titanium surface.
- Rigid setup:
- Ensure a rigid setup with minimal overhang of the workpiece and tools to reduce vibration and chatter.
- Use the shortest possible tool lengths and most rigid tool holders to maximize stiffness.
- Chip control:
- Use chip breakers or interrupted cutting techniques to manage chip formation and prevent long, stringy chips that can wrap around the tool or workpiece.
- Regular chip evacuation is crucial to prevent re-cutting of chips, which can lead to poor surface finish and reduced tool life.
- Specific machining operations:
- Turning: Use a positive rake angle and a large nose radius to improve surface finish. Maintain constant feed and depth of cut to prevent work hardening.
- Milling: Climb milling is generally preferred over conventional milling to reduce work hardening. Use tools with a high number of flutes to distribute cutting forces and improve chip evacuation.
- Drilling: Use short, rigid drills with proper point geometry. Peck drilling techniques can help with chip evacuation and heat dissipation.
- Threading: Use thread milling rather than tapping when possible, as it reduces the risk of tool breakage and produces better thread quality.
When machining Grade 3 titanium wire, it's important to monitor tool wear closely and replace tools before they become excessively worn. Dull tools can lead to increased cutting forces, heat generation, and work hardening, which can quickly deteriorate the machining process and workpiece quality.
Additionally, consider the following tips for successful machining of Gr3 titanium wire:
- Start with conservative cutting parameters and gradually optimize based on results and tool wear.
- Use specialized CAM software and cutting strategies designed for titanium machining to optimize tool paths and minimize heat buildup.
- Consider cryogenic machining techniques for improved tool life and surface finish in certain applications.
- Implement proper safety measures, as titanium chips can be pyrophoric under certain conditions.
By following these best practices and techniques, it is possible to machine Grade 3 titanium wire effectively, achieving the desired dimensional accuracy and surface finish while maintaining reasonable tool life and productivity.
Conclusion
In conclusion, Grade 3 titanium wire can indeed be welded and machined, but both processes require careful consideration of the material's unique properties and characteristics. Welding Gr3 titanium wire is possible with proper techniques and precautions to maintain its desirable properties. Machining, while challenging, can be successfully accomplished using appropriate cutting parameters, tools, and cooling strategies. By understanding the material's behavior and following best practices, manufacturers and engineers can effectively work with Grade 3 titanium wire to create high-quality components for various applications in industries such as aerospace, medical, and marine engineering.
At SHAANXI CXMET TECHNOLOGY CO., LTD, we take pride in our extensive product range, which caters to diverse customer needs. Our company is equipped with outstanding production and processing capabilities, ensuring the high quality and precision of our products. We are committed to innovation and continuously strive to develop new products, keeping us at the forefront of our industry. With leading technological development capabilities, we are able to adapt and evolve in a rapidly changing market. Furthermore, we offer customized solutions to meet the specific requirements of our clients. If you are interested in our products or wish to learn more about the intricate details of our offerings, please do not hesitate to contact us at sales@cxmet.com. Our team is always ready to assist you.
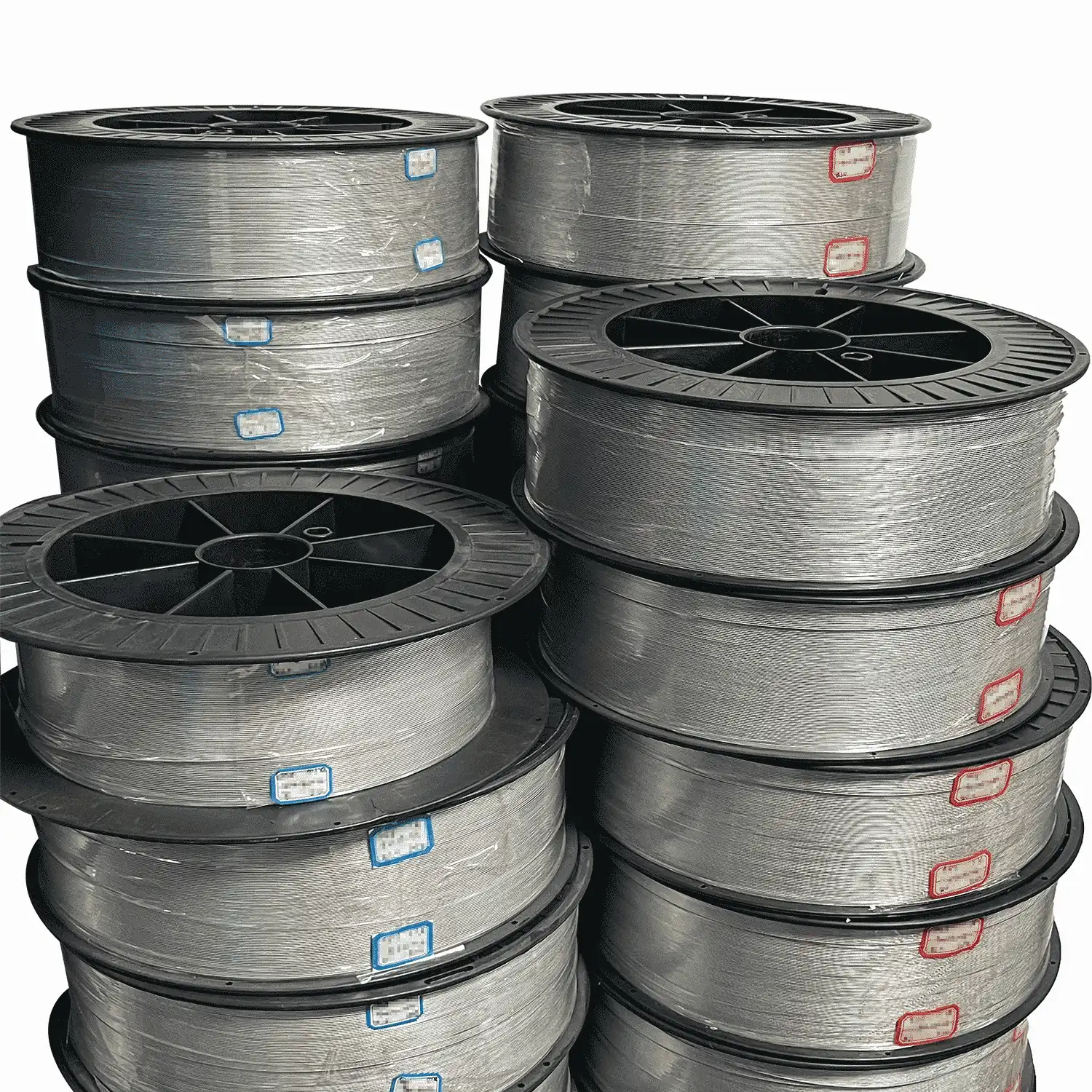
References
- ASM International. (2015). ASM Handbook, Volume 6A: Welding Fundamentals and Processes.
- Boyer, R., Welsch, G., & Collings, E. W. (1994). Materials Properties Handbook: Titanium Alloys. ASM International.
- Donachie, M. J. (2000). Titanium: A Technical Guide. ASM International.
- Ezugwu, E. O., & Wang, Z. M. (1997). Titanium alloys and their machinability—a review. Journal of Materials Processing Technology, 68(3), 262-274.
- Leyens, C., & Peters, M. (Eds.). (2003). Titanium and titanium alloys: fundamentals and applications. John Wiley & Sons.
- Lütjering, G., & Williams, J. C. (2007). Titanium. Springer Science & Business Media.
- Machado, A. R., & Wallbank, J. (1990). Machining of titanium and its alloys—a review. Proceedings of the Institution of Mechanical Engineers, Part B: Journal of Engineering Manufacture, 204(1), 53-60.
- Peters, M., Kumpfert, J., Ward, C. H., & Leyens, C. (2003). Titanium alloys for aerospace applications. Advanced Engineering Materials, 5(6), 419-427.
- Veiga, C., Davim, J. P., & Loureiro, A. J. R. (2013). Properties and applications of titanium alloys: A brief review. Reviews on Advanced Materials Science, 32(2), 133-148.
- Yang, X., & Liu, C. R. (1999). Machining titanium and its alloys. Machining Science and Technology, 3(1), 107-139.