Selecting the appropriate Ti-6AL-7Nb titanium alloy wire for your project is crucial for ensuring optimal performance and longevity. This advanced titanium alloy, known for its exceptional strength-to-weight ratio, corrosion resistance, and biocompatibility, has found widespread applications in various industries, including aerospace, medical, and automotive. In this comprehensive guide, we'll explore the key factors to consider when choosing the right Ti-6AL-7Nb titanium alloy wire, helping you make an informed decision for your specific project requirements.
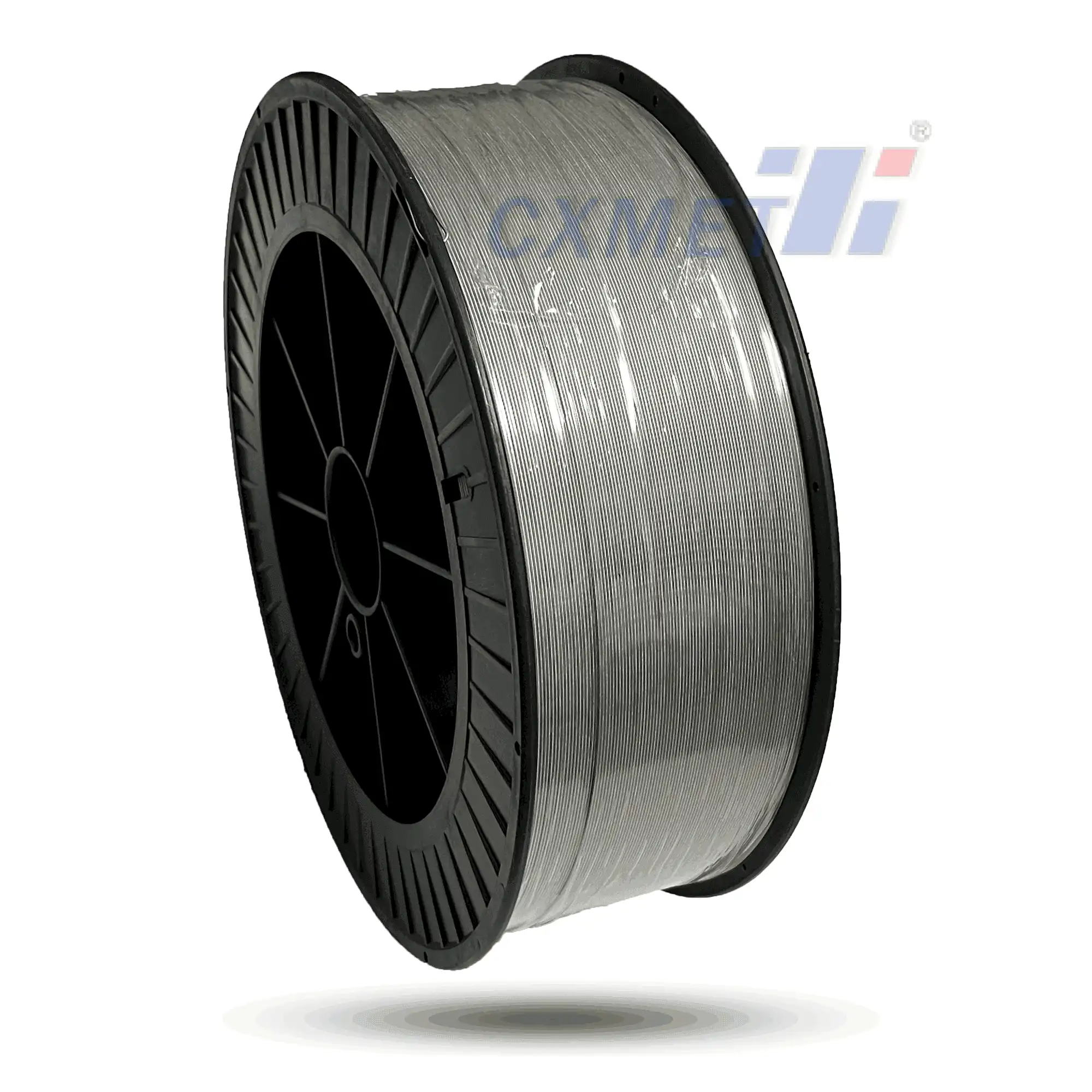
What are the key properties of Ti-6AL-7Nb titanium alloy wire?
Ti-6AL-7Nb titanium alloy wire is renowned for its unique combination of properties that make it an ideal choice for a wide range of applications. Understanding these key properties is essential for selecting the right wire for your project:
- Mechanical Strength: Ti-6AL-7Nb offers excellent mechanical strength, with a tensile strength ranging from 900 to 1050 MPa. This high strength-to-weight ratio makes it particularly suitable for applications requiring robust yet lightweight materials.
- Corrosion Resistance: The alloy exhibits superior corrosion resistance, especially in aggressive environments. This property is attributed to the formation of a stable oxide layer on the surface, protecting the underlying metal from further oxidation.
- Biocompatibility: Ti-6AL-7Nb is highly biocompatible, making it an excellent choice for medical implants and devices. The alloy's low toxicity and ability to integrate with human tissue without adverse reactions have led to its widespread use in orthopedic and dental applications.
- Heat Resistance: The alloy maintains its mechanical properties at elevated temperatures, making it suitable for high-temperature applications in aerospace and automotive industries.
- Fatigue Resistance: Ti-6AL-7Nb demonstrates excellent fatigue resistance, ensuring long-term durability in applications subjected to cyclic loading.
- Low Modulus of Elasticity: The alloy's relatively low modulus of elasticity (about 105 GPa) allows for better stress distribution and reduced stress shielding in medical implants.
When selecting Ti-6AL-7Nb titanium alloy wire, it's crucial to consider these properties in relation to your specific project requirements. For instance, if your application demands high strength and excellent corrosion resistance, Ti-6AL-7Nb wire could be an ideal choice. However, if biocompatibility is a primary concern, such as in medical implants, the alloy's proven track record in this field makes it particularly attractive.
How does Ti-6AL-7Nb compare to other titanium alloys for wire applications?
When considering Ti-6AL-7Nb Titanium Alloy Wire for wire applications, it's essential to understand how it compares to other titanium alloys. This comparison will help you determine if Ti-6AL-7Nb is indeed the best choice for your specific project:
- Ti-6AL-7Nb vs. Ti-6AL-4V: Ti-6AL-4V is one of the most widely used titanium alloys. While both alloys offer similar strength levels, Ti-6AL-7Nb has the advantage of being vanadium-free, which is particularly beneficial in medical applications due to concerns about the long-term effects of vanadium in the body. Ti-6AL-7Nb also exhibits slightly better corrosion resistance and biocompatibility.
- Ti-6AL-7Nb vs. Commercially Pure Titanium (CP Ti): CP Ti is known for its excellent corrosion resistance and biocompatibility. However, Ti-6AL-7Nb offers significantly higher strength and better mechanical properties, making it more suitable for applications requiring both strength and biocompatibility.
- Ti-6AL-7Nb vs. Ti-15Mo: Ti-15Mo is another biocompatible alloy used in medical applications. While Ti-15Mo has a lower elastic modulus, which can be beneficial in certain orthopedic applications, Ti-6AL-7Nb generally offers higher strength and better overall mechanical properties.
- Ti-6AL-7Nb vs. Ti-13Nb-13Zr: Both alloys are used in biomedical applications. Ti-13Nb-13Zr has a lower elastic modulus, which can be advantageous in reducing stress shielding. However, Ti-6AL-7Nb typically offers higher strength and better overall performance in a wider range of applications.
When comparing Ti-6AL-7Nb to other titanium alloys for wire applications, consider the following factors:
- Strength Requirements: If high strength is a primary concern, Ti-6AL-7Nb is often a superior choice compared to CP Ti and some other biomedical alloys.
- Biocompatibility: For medical applications, Ti-6AL-7Nb offers excellent biocompatibility, comparable to or better than many other titanium alloys.
- Corrosion Resistance: While most titanium alloys offer good corrosion resistance, Ti-6AL-7Nb excels in this area, particularly in biological environments.
- Cost and Availability: Consider the cost and availability of Ti-6AL-7Nb compared to other alloys. While it may be more expensive than some alternatives, its unique properties often justify the cost in specialized applications.
- Specific Application Requirements: Some applications may have specific requirements that favor one alloy over another. For example, if a very low elastic modulus is crucial, an alloy like Ti-15Mo might be preferred over Ti-6AL-7Nb.
By carefully considering these factors and comparing Ti-6AL-7Nb to other titanium alloys, you can make an informed decision on whether it's the right choice for your wire application. Remember that while Ti-6AL-7Nb offers an excellent balance of properties, the best alloy choice will ultimately depend on your specific project requirements and constraints.
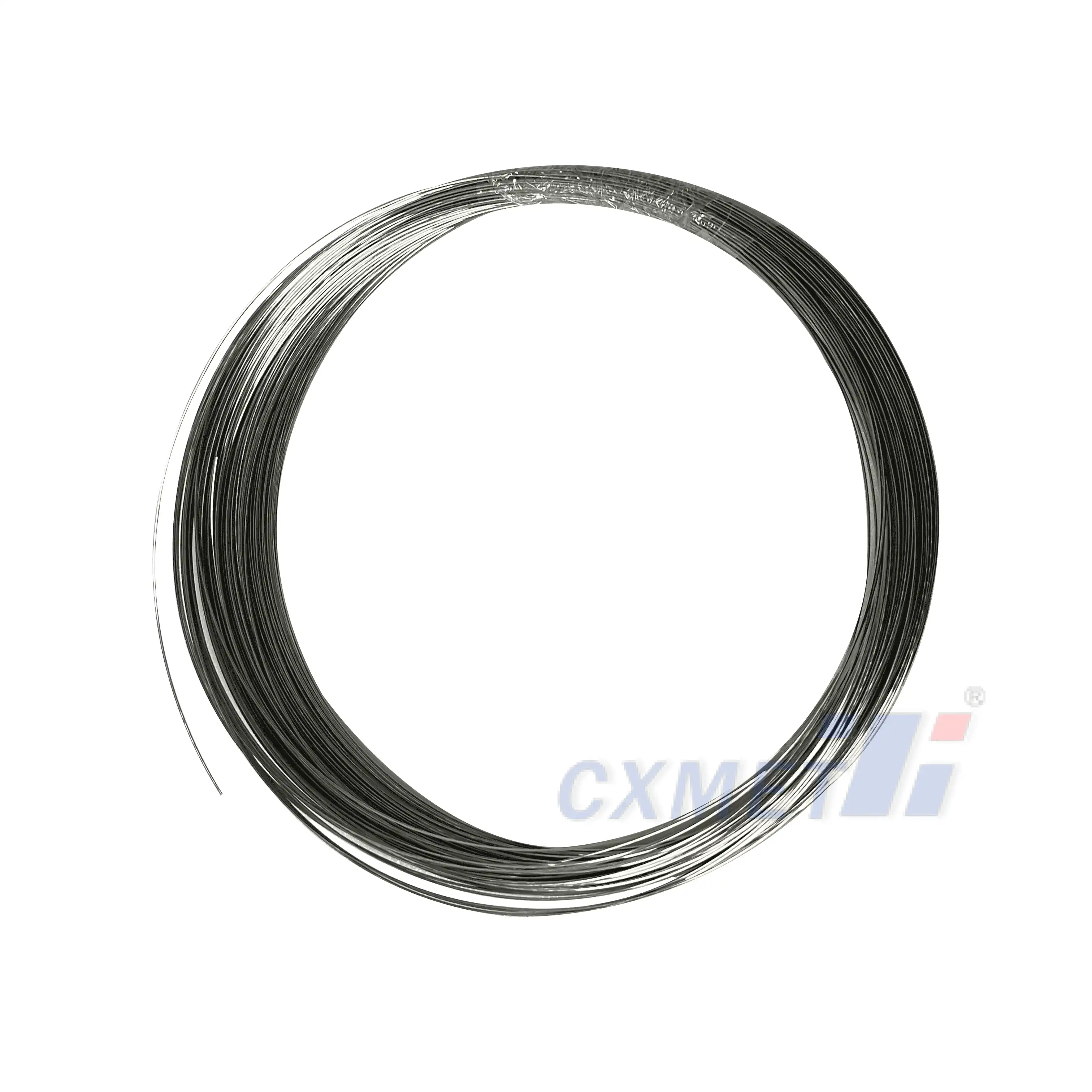
What are the best manufacturing processes for Ti-6AL-7Nb titanium alloy wire?
Selecting the appropriate manufacturing process for Ti-6AL-7Nb Titanium Alloy Wire is crucial to ensure the desired properties and performance in your final product. Here are some of the best manufacturing processes for Ti-6AL-7Nb titanium alloy wire, along with their advantages and considerations:
- Cold Drawing:
- Process: The wire is drawn through a series of dies with progressively smaller diameters, reducing its cross-sectional area and increasing its length.
- Advantages: Produces wire with excellent surface finish, tight dimensional tolerances, and improved mechanical properties due to work hardening.
- Considerations: May require intermediate annealing steps to prevent excessive work hardening and maintain ductility.
- Hot Extrusion:
- Process: The alloy is heated to high temperatures and forced through a die to create the wire form.
- Advantages: Allows for the production of complex cross-sections and can process larger diameter wires more efficiently than cold drawing.
- Considerations: May result in a less refined microstructure compared to cold-worked wire, potentially requiring additional processing.
- Powder Metallurgy:
- Process: Ti-6AL-7Nb powder is compacted and sintered to form wire.
- Advantages: Allows for precise control of composition and can produce near-net-shape products with minimal material waste.
- Considerations: May have higher production costs and can sometimes result in residual porosity that needs to be addressed.
- Additive Manufacturing (3D Printing):
- Process: Wire is produced layer by layer using techniques such as Direct Energy Deposition (DED) or Wire Arc Additive Manufacturing (WAAM).
- Advantages: Enables the production of complex geometries and can be cost-effective for small-scale or customized production.
- Considerations: May require post-processing to achieve desired surface finish and mechanical properties.
When selecting the best manufacturing process for your Ti-6AL-7Nb titanium alloy wire, consider the following factors:
- Desired Wire Diameter and Tolerance: Cold drawing typically offers the tightest tolerances and is ideal for smaller diameter wires, while hot extrusion may be more suitable for larger diameters.
- Required Mechanical Properties: Cold-worked wire generally offers higher strength due to work hardening, but may have reduced ductility. Hot-worked or annealed wire may provide a better balance of strength and ductility.
- Surface Finish Requirements: Cold drawing usually produces the best surface finish, which can be crucial for certain applications, particularly in the medical field.
- Production Volume: For high-volume production, traditional processes like cold drawing or hot extrusion may be more cost-effective. For smaller batches or customized products, additive manufacturing could be advantageous.
- Complexity of Wire Geometry: If you require wires with complex cross-sections or internal features, processes like hot extrusion or additive manufacturing may be more suitable.
- Post-Processing Requirements: Consider any additional treatments or processes that may be necessary after wire formation, such as heat treatment, surface modification, or sterilization for medical applications.
It's important to note that the choice of manufacturing process can significantly impact the final properties of the Ti-6AL-7Nb wire. For instance, cold-worked wire may have higher strength but lower ductility compared to annealed wire. Therefore, it's crucial to work closely with your material supplier or manufacturer to ensure that the chosen process aligns with your specific application requirements.
In many cases, a combination of processes may be employed to achieve the desired properties. For example, wire might be initially produced through hot extrusion, followed by cold drawing to refine the diameter and improve surface finish, and finally subjected to a specific heat treatment to optimize the microstructure and mechanical properties.
By carefully considering these factors and working with experienced manufacturers, you can ensure that the Ti-6AL-7Nb titanium alloy wire for your project is produced using the most appropriate manufacturing processes, resulting in a product that meets or exceeds your performance requirements.
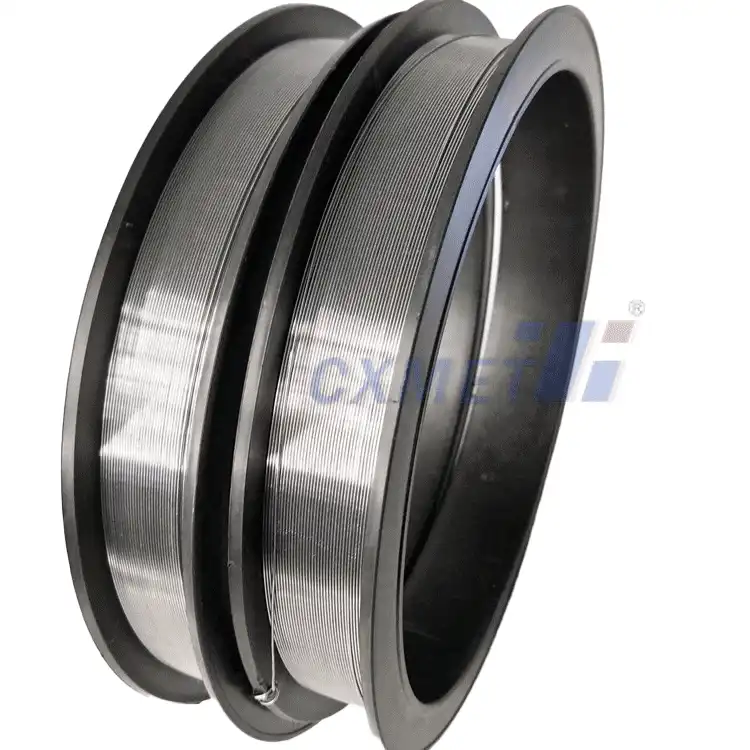
Conclusion
Choosing the right Ti-6AL-7Nb titanium alloy wire for your project involves careful consideration of its unique properties, how it compares to other titanium alloys, and the most suitable manufacturing processes. By understanding these key aspects, you can make an informed decision that ensures optimal performance and longevity in your specific application. Whether you're working on a medical implant, aerospace component, or any other demanding application, Ti-6AL-7Nb offers a compelling combination of strength, corrosion resistance, and biocompatibility that makes it a versatile and valuable material choice.
At SHAANXI CXMET TECHNOLOGY CO., LTD, we take pride in our extensive product range, which caters to diverse customer needs. Our company is equipped with outstanding production and processing capabilities, ensuring the high quality and precision of our products. We are committed to innovation and continuously strive to develop new products, keeping us at the forefront of our industry. With leading technological development capabilities, we are able to adapt and evolve in a rapidly changing market. Furthermore, we offer customized solutions to meet the specific requirements of our clients. If you are interested in our products or wish to learn more about the intricate details of our offerings, please do not hesitate to contact us at sales@cxmet.com. Our team is always ready to assist you.
References
- Geetha, M., Singh, A. K., Asokamani, R., & Gogia, A. K. (2009). Ti based biomaterials, the ultimate choice for orthopaedic implants – A review. Progress in Materials Science, 54(3), 397-425.
- Niinomi, M. (2008). Mechanical biocompatibilities of titanium alloys for biomedical applications. Journal of the Mechanical Behavior of Biomedical Materials, 1(1), 30-42.
- Rack, H. J., & Qazi, J. I. (2006). Titanium alloys for biomedical applications. Materials Science and Engineering: C, 26(8), 1269-1277.
- Long, M., & Rack, H. J. (1998). Titanium alloys in total joint replacement—a materials science perspective. Biomaterials, 19(18), 1621-1639.
- Elias, C. N., Lima, J. H. C., Valiev, R., & Meyers, M. A. (2008). Biomedical applications of titanium and its alloys. JOM, 60(3), 46-49.
- Titanium Information Group. (2021). Titanium Alloys - Ti-6Al-7Nb Properties and Applications.
- ASM International. (2015). ASM Handbook, Volume 2: Properties and Selection: Nonferrous Alloys and Special-Purpose Materials. Materials Park, OH: ASM International.
- ASTM International. (2019). ASTM F1295 - 19 Standard Specification for Wrought Titanium-6Aluminum-7Niobium Alloy for Surgical Implant Applications (UNS R56700).
- Lutjering, G., & Williams, J. C. (2007). Titanium (2nd ed.). Berlin: Springer-Verlag.
- Donachie, M. J. (2000). Titanium: A Technical Guide (2nd ed.). Materials Park, OH: ASM International.