Titanium socket weld flanges are crucial components in various industrial applications, known for their exceptional strength, corrosion resistance, and durability. Proper maintenance of these flanges is essential to ensure their longevity and optimal performance. This blog post will explore the best practices for maintaining titanium socket weld flanges, addressing common concerns and providing practical solutions to keep these vital components in top condition.
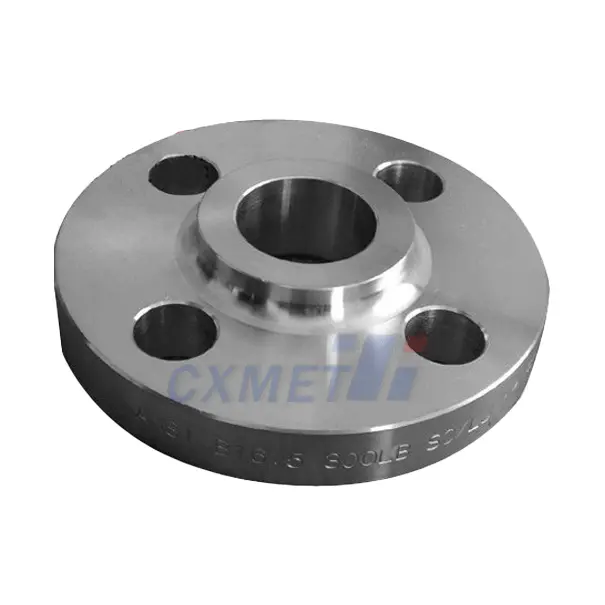
What are the best cleaning methods for titanium socket weld flanges?
Cleaning titanium socket weld flanges is a critical aspect of their maintenance. The proper cleaning methods not only ensure the longevity of the flanges but also maintain their structural integrity and performance. Here are some of the best cleaning methods for titanium socket weld flanges:
- Solvent cleaning: This method involves using organic solvents such as acetone, methyl ethyl ketone (MEK), or isopropyl alcohol to remove oils, greases, and other organic contaminants from the flange surface. It's important to use clean, lint-free cloths or wipes during this process to avoid introducing additional contaminants.
- Alkaline cleaning: For more stubborn contaminants, an alkaline cleaning solution can be used. These solutions are typically composed of sodium hydroxide or potassium hydroxide and are effective in removing heavy oils, greases, and particulate matter. After cleaning, it's crucial to thoroughly rinse the flange with deionized water to remove any residual alkaline solution.
- Acid cleaning: In cases where scale, rust, or other inorganic contaminants are present, acid cleaning may be necessary. However, this method should be used with caution, as improper application can damage the titanium surface. Commonly used acids include hydrofluoric acid, nitric acid, or a mixture of both. It's essential to follow proper safety protocols and manufacturer guidelines when using acid cleaning methods.
- Ultrasonic cleaning: This method uses high-frequency sound waves to create cavitation bubbles in a liquid cleaning solution. These bubbles implode on the surface of the flange, effectively removing contaminants. Ultrasonic cleaning is particularly useful for removing particles from hard-to-reach areas and complex geometries.
- Abrasive cleaning: For light surface contamination or oxidation, mild abrasive cleaning methods can be employed. This may include the use of non-metallic abrasive pads or fine-grit sandpaper. It's crucial to use only titanium-compatible abrasives to avoid contamination of the flange surface.
Regardless of the cleaning method chosen, it's essential to follow up with a thorough rinse using clean, deionized water to remove any residual cleaning agents or contaminants. After cleaning, the flange should be dried immediately to prevent water spots or corrosion.
It's worth noting that the choice of cleaning method depends on the type and severity of contamination, as well as the specific requirements of the application. In some cases, a combination of cleaning methods may be necessary to achieve the desired results. Always consult the manufacturer's guidelines and industry standards when determining the most appropriate cleaning method for your titanium socket weld flanges.
How often should titanium socket weld flanges be inspected?
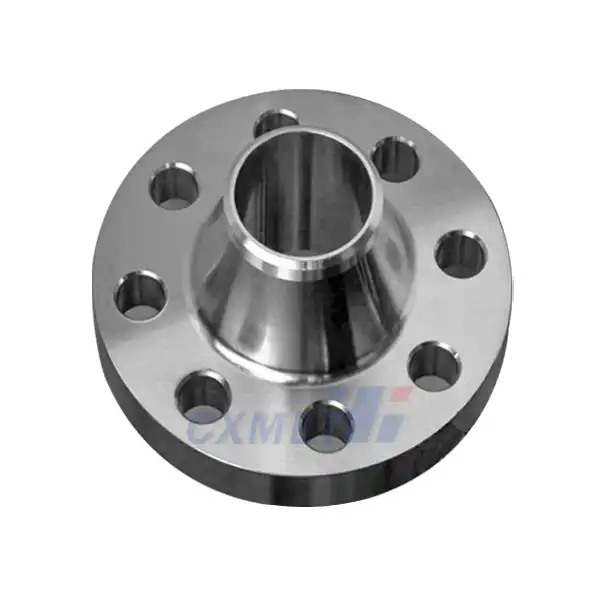
Regular inspection of titanium socket weld flanges is crucial for maintaining their integrity and ensuring the safety and efficiency of the entire piping system. The frequency of inspections can vary depending on several factors, including the operating environment, the nature of the fluid or gas being transported, and the criticality of the application. However, there are some general guidelines that can help determine an appropriate inspection schedule:
- Initial inspection: A thorough inspection should be conducted immediately after installation to ensure proper fit, alignment, and absence of any damage that may have occurred during the installation process.
- Routine visual inspections: These should be performed at least quarterly, or more frequently in harsh environments. Visual inspections can help identify obvious signs of wear, corrosion, or damage.
- Annual comprehensive inspections: A more detailed inspection should be carried out annually, involving a close examination of the flange surface, weld joints, and gasket seating areas. This may include non-destructive testing methods such as dye penetrant testing or ultrasonic testing.
- Shutdown inspections: During planned shutdowns or maintenance periods, take the opportunity to perform a thorough inspection of all flanges in the system.
- Post-incident inspections: After any significant event, such as a process upset, earthquake, or extreme weather conditions, conduct a special inspection to ensure the integrity of the flanges has not been compromised.
During these inspections, pay particular attention to the following areas:
- Surface condition: Look for signs of corrosion, pitting, or erosion on the flange face and bore.
- Weld integrity: Examine the socket weld for any cracks, porosity, or incomplete fusion.
- Gasket seating area: Check for any damage, scratches, or irregularities that could affect the seal.
- Bolt holes: Inspect for any elongation, cracking, or wear around the bolt holes.
- Alignment: Ensure the flange remains properly aligned with its mating flange.
It's important to note that the inspection frequency may need to be increased in certain situations, such as:
- When the flanges are exposed to highly corrosive or erosive environments
- In critical applications where failure could result in significant safety hazards or operational downtime
- When there's a history of issues or failures with similar flanges in the system
- In applications with frequent thermal cycling or high vibration
Always consult industry standards, such as ASME B31.3 for process piping or API 570 for in-service inspection of piping systems, to ensure compliance with recommended inspection intervals and procedures. Additionally, maintain detailed records of all inspections, including dates, findings, and any corrective actions taken. These records can be invaluable for tracking the performance of the flanges over time and identifying any emerging trends or issues.
What are common signs of wear in titanium socket weld flanges?
Recognizing the signs of wear in titanium socket weld flanges is crucial for maintaining the integrity and safety of piping systems. While titanium is known for its excellent corrosion resistance and durability, these flanges can still experience wear over time, especially in demanding industrial environments. Being able to identify these signs early can help prevent more serious issues and costly downtime. Here are some common signs of wear to look out for in titanium socket weld flanges:
- Surface corrosion: Although titanium is highly resistant to corrosion, it can still occur under certain conditions. Look for discoloration, pitting, or rough spots on the flange surface. In some cases, you may notice a thin, tightly adherent oxide film, which is normal and actually provides additional protection. However, if the oxide layer appears loose or flaky, it may indicate underlying corrosion issues.
- Erosion: High-velocity fluids or particles in the fluid stream can cause erosion, particularly in areas of turbulent flow. Check for thinning of the flange material, especially near the bore and at the transition between the flange face and the bore.
- Cracking: Inspect for any signs of cracking, which can occur due to stress corrosion, fatigue, or improper installation. Pay particular attention to areas around bolt holes and the socket weld joint. Even small cracks can propagate over time and lead to failures.
- Deformation: Look for any signs of warping, bending, or out-of-roundness in the flange. This can be caused by excessive loads, thermal cycling, or improper handling during installation or maintenance.
- Galling or seizing: Check the threads of any bolts or studs for signs of galling, which can occur when titanium surfaces rub against each other under high loads. This can lead to seizing and make disassembly difficult.
- Gasket impression: Examine the gasket seating area for any permanent indentation or damage caused by over-compression of the gasket. This can affect the flange's ability to maintain a proper seal.
- Fretting wear: In applications with vibration or frequent thermal cycling, look for signs of fretting wear at the contact points between the flange and its mating surface.
- Discoloration: While some discoloration is normal for titanium (it can form a protective oxide layer), unusual or excessive discoloration may indicate exposure to contaminants or high temperatures that could affect the flange's properties.
- Weld defects: Carefully inspect the socket weld for any signs of cracking, incomplete fusion, porosity, or undercutting. These defects can compromise the integrity of the joint and lead to leaks or failures.
- Bolt hole elongation: Check for any elongation or wear around the bolt holes, which can be caused by improper bolt tension or vibration.
When inspecting for these signs of wear, it's important to use appropriate inspection techniques. Visual inspection is a good starting point, but it may not reveal all potential issues. Consider using non-destructive testing methods such as:
- Dye penetrant testing to detect surface cracks
- Ultrasonic testing to identify internal flaws or measure wall thickness
- Radiographic testing for a comprehensive view of the weld integrity
- Hardness testing to check for any changes in material properties
If any signs of wear are detected, it's crucial to assess their severity and potential impact on the flange's performance. In some cases, minor wear may be acceptable and can be monitored over time. However, significant wear or any signs that could compromise the flange's integrity should be addressed promptly. This may involve repairing the flange, replacing it, or adjusting operating conditions to mitigate further wear.
Remember that the interpretation of wear signs should be done by qualified personnel who are familiar with the specific application and operating conditions of the titanium socket weld flanges. Always refer to relevant industry standards and manufacturer guidelines when assessing wear and making decisions about maintenance or replacement.
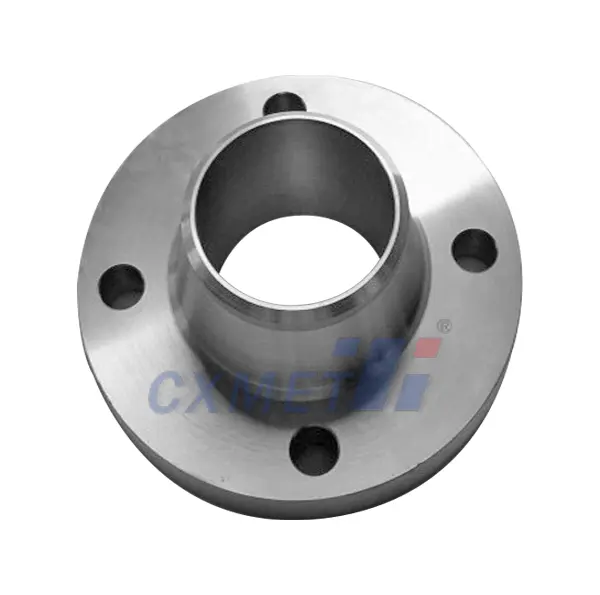
Conclusion
Maintaining titanium socket weld flanges is crucial for ensuring the longevity and reliability of piping systems in various industrial applications. By implementing proper cleaning methods, adhering to regular inspection schedules, and being vigilant for signs of wear, operators can significantly extend the life of these critical components and prevent costly failures. Remember that while titanium is known for its durability and corrosion resistance, it still requires careful attention and maintenance to perform optimally in demanding environments. Always consult with manufacturers, industry standards, and experienced professionals to develop a comprehensive maintenance strategy tailored to your specific application and operating conditions.
At SHAANXI CXMET TECHNOLOGY CO., LTD, we take pride in our extensive product range, which caters to diverse customer needs. Our company is equipped with outstanding production and processing capabilities, ensuring the high quality and precision of our products. We are committed to innovation and continuously strive to develop new products, keeping us at the forefront of our industry. With leading technological development capabilities, we are able to adapt and evolve in a rapidly changing market. Furthermore, we offer customized solutions to meet the specific requirements of our clients. If you are interested in our products or wish to learn more about the intricate details of our offerings, please do not hesitate to contact us at sales@cxmet.com. Our team is always ready to assist you.
References
- ASME B16.5 - Pipe Flanges and Flanged Fittings
- API 570 - Piping Inspection Code: In-service Inspection, Rating, Repair, and Alteration of Piping Systems
- ASTM B381 - Standard Specification for Titanium and Titanium Alloy Forgings
- NACE SP0199 - Standard Practice: Corrosion Control of Titanium in Oilfield and Chemical Service
- AWS D1.9/D1.9M - Structural Welding Code - Titanium
- Titanium Information Group - Cleaning and Maintenance of Titanium
- Journal of Materials Engineering and Performance - "Corrosion Behavior of Titanium and Its Alloys in Various Environments"
- Handbook of Maintenance Management and Engineering - Chapter on Flange Maintenance
- International Journal of Pressure Vessels and Piping - "Inspection and Maintenance of Flanged Joints in Process Plants"
- Materials Science and Engineering: A - "Wear Mechanisms in Titanium Alloys Under Different Loading Conditions"