Grade 4 titanium wire, known for its exceptional corrosion resistance and strength, has gained significant attention in marine applications. This high-performance material offers a unique combination of properties that make it particularly well-suited for use in harsh marine environments. In this blog post, we'll explore the performance of Gr4 titanium wire in marine settings, addressing its corrosion resistance, mechanical properties, and long-term durability.
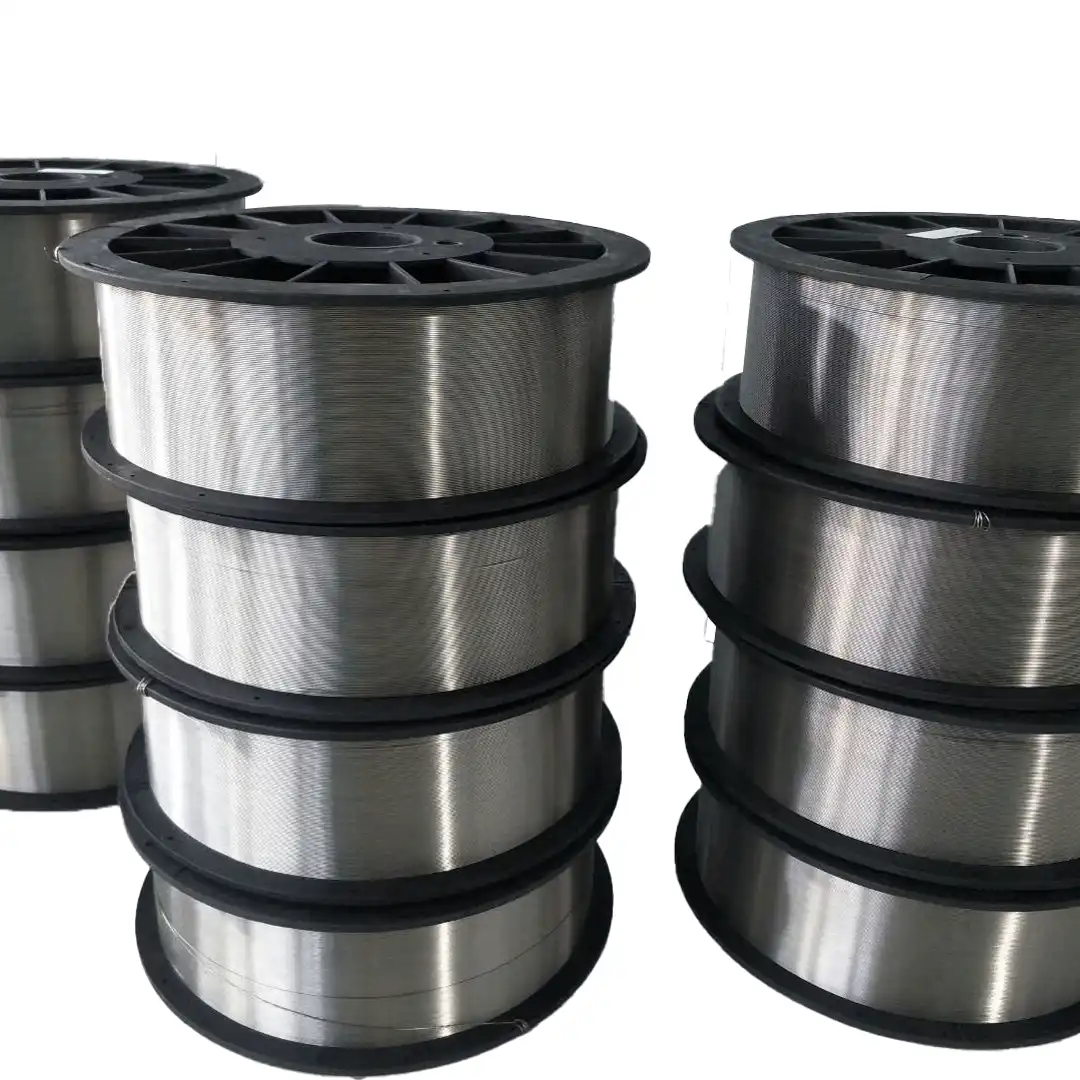
What makes Gr4 titanium wire resistant to seawater corrosion?
Gr4 titanium wire wire exhibits outstanding resistance to seawater corrosion, making it an ideal choice for marine applications. This exceptional corrosion resistance can be attributed to several factors:
- Passive oxide layer formation: When exposed to oxygen, titanium rapidly forms a thin, stable oxide layer on its surface. This naturally occurring protective film, primarily composed of titanium dioxide (TiO2), acts as a barrier against corrosive elements in seawater. The oxide layer is self-healing, meaning that if it's damaged, it quickly reforms in the presence of oxygen, providing continuous protection.
- Chemical stability: Gr4 titanium has a high affinity for oxygen, which contributes to the formation and stability of the protective oxide layer. This chemical stability prevents the wire from reacting with corrosive elements in seawater, such as chlorides and sulfates.
- Galvanic compatibility: Titanium has a relatively noble electrochemical potential, which means it's less likely to participate in galvanic corrosion when in contact with other metals in seawater. This property makes it compatible with a wide range of materials used in marine environments.
- Resistance to pitting and crevice corrosion: The stable oxide layer on Gr4 titanium wire provides excellent protection against localized forms of corrosion, such as pitting and crevice corrosion, which are common challenges in marine environments.
The combination of these factors results in Gr4 titanium wire's exceptional performance in seawater, with corrosion rates typically measured in microns per year. This superior corrosion resistance translates to extended service life and reduced maintenance requirements for marine applications, making it a cost-effective choice for long-term use in harsh marine environments.
How do the mechanical properties of Gr4 titanium wire compare to other marine-grade materials?
Grade 4 titanium wire offers a unique combination of mechanical properties that make it stand out among other marine-grade materials. When comparing Gr4 titanium wire to alternatives such as stainless steel, copper alloys, and other titanium grades, several key aspects come into play:
- Strength-to-weight ratio: Gr4 titanium wire boasts an impressive strength-to-weight ratio, surpassing that of many stainless steel grades commonly used in marine applications. This high strength combined with low density makes it an excellent choice for applications where weight reduction is crucial, such as in offshore structures or marine vessels.
- Yield strength and tensile strength: Grade 4 titanium wire typically exhibits a yield strength of around 480 MPa and a tensile strength of about 550 MPa. These values are higher than those of many austenitic stainless steels, such as 316L, which is widely used in marine environments. The superior strength of Gr4 titanium allows for the use of thinner wire diameters while maintaining the required load-bearing capacity.
- Fatigue resistance: Titanium alloys, including Gr4, demonstrate excellent fatigue resistance, which is crucial for components subjected to cyclic loading in marine applications. This property contributes to the long-term reliability and durability of structures and equipment made with Gr4 titanium wire.
- Low elastic modulus: The relatively low elastic modulus of titanium (about half that of steel) provides greater flexibility and better stress distribution in certain applications. This characteristic can be advantageous in marine environments where structures may be subjected to dynamic loads and vibrations.
- Toughness and ductility: Gr4 titanium wire exhibits good toughness and ductility, allowing it to withstand impact loads and deform without fracturing. These properties are particularly valuable in marine applications where components may be subjected to sudden stresses or impacts.
- Temperature resistance: Titanium maintains its mechanical properties over a wide temperature range, from cryogenic temperatures to moderately elevated temperatures. This stability makes it suitable for various marine applications, including deep-sea exploration and offshore oil and gas operations.
When compared to other marine-grade materials, Gr4 titanium wire often outperforms in terms of overall mechanical properties and corrosion resistance. For instance, while duplex stainless steels offer high strength and good corrosion resistance, they may be more susceptible to stress corrosion cracking in chloride-rich environments. Copper alloys, while offering excellent biofouling resistance, generally have lower strength and may be more prone to erosion-corrosion in high-flow seawater conditions.
It's important to note that the selection of materials for marine applications should consider not only mechanical properties but also factors such as cost, availability, and specific environmental conditions. While Gr4 titanium wire excels in many aspects, it may not always be the most cost-effective solution for every application. However, its unique combination of properties makes it an attractive option for critical components and long-term installations in harsh marine environments.
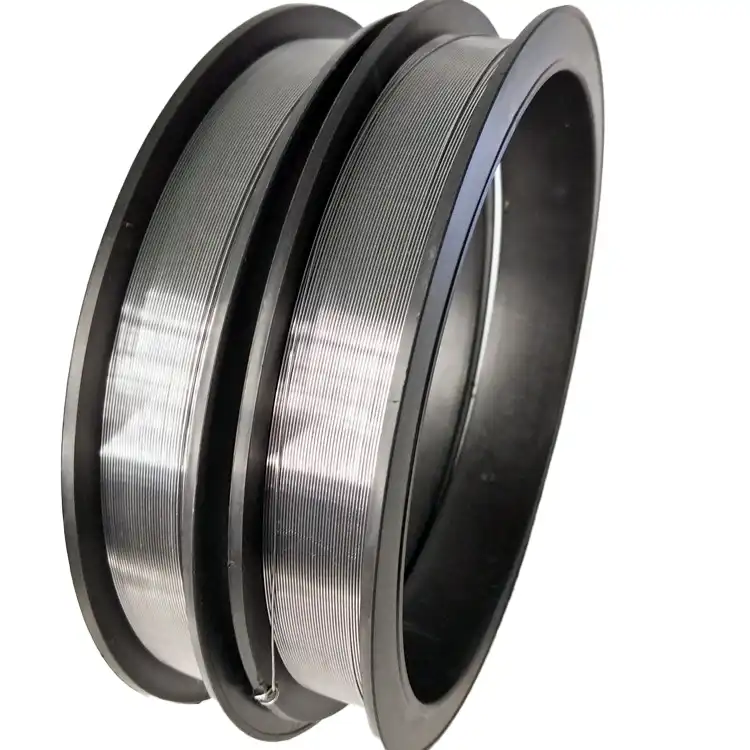
What are the long-term effects of marine exposure on Gr4 titanium wire?
The long-term performance of Gr4 titanium wire in marine environments is a critical consideration for engineers and designers working on marine projects. Understanding how this material behaves over extended periods of exposure to seawater and marine conditions is essential for predicting its service life and maintenance requirements. Let's explore the long-term effects of marine exposure on Gr4 titanium wire:
- Corrosion resistance stability: One of the most notable long-term effects of marine exposure on Gr4 titanium wire is the stability of its corrosion resistance. The protective oxide layer that forms on the surface of the titanium continues to provide excellent protection against corrosion even after years of exposure to seawater. Studies have shown that the corrosion rate of titanium in seawater remains extremely low, often less than 0.1 mm per year, even after decades of immersion.
- Mechanical property retention: Gr4 titanium wire generally maintains its mechanical properties over long periods in marine environments. Unlike some other materials that may experience degradation in strength or ductility due to corrosion or environmental factors, titanium's inherent corrosion resistance helps preserve its mechanical integrity. This property retention contributes to the long-term reliability of structures and components made with Gr4 titanium wire.
- Biofouling resistance: While not completely immune to marine growth, titanium exhibits better resistance to biofouling compared to many other materials. The smooth, stable oxide surface of Gr4 titanium wire makes it less hospitable for marine organisms to attach and grow. Over time, this can result in reduced maintenance requirements and improved performance of marine structures and equipment.
- Galvanic corrosion considerations: In long-term marine applications, it's important to consider the galvanic compatibility of Gr4 titanium wire with other materials in the system. While titanium is generally noble and resistant to galvanic corrosion, it can potentially accelerate the corrosion of less noble metals if not properly isolated. Proper design and material selection can mitigate this risk in long-term installations.
- Fatigue performance: The excellent fatigue resistance of Gr4 titanium wire contributes to its long-term durability in marine environments. Components subjected to cyclic loading, such as mooring lines or structural supports, can benefit from titanium's ability to withstand repeated stress cycles without significant degradation in performance.
- Erosion-corrosion resistance: In high-flow seawater conditions or areas with suspended particles, Gr4 titanium wire demonstrates good resistance to erosion-corrosion. The hard, stable oxide layer protects the underlying metal from the combined effects of mechanical wear and chemical attack, maintaining its integrity over extended periods.
- Hydrogen embrittlement resistance: Unlike some high-strength steels, Gr4 titanium wire exhibits excellent resistance to hydrogen embrittlement in marine environments. This property is particularly important for long-term applications where exposure to cathodic protection systems or other sources of hydrogen might be a concern.
- Temperature stability: The mechanical and corrosion-resistant properties of Gr4 titanium wire remain stable across a wide range of temperatures commonly encountered in marine environments. This stability ensures consistent performance in various marine applications, from shallow coastal waters to deep-sea installations.
Long-term studies and field experiences have consistently demonstrated the excellent durability of Gr4 titanium wire in marine environments. For example, titanium heat exchangers and piping systems in offshore oil and gas platforms have shown minimal degradation after decades of service in seawater. Similarly, titanium components used in marine research equipment and oceanographic instrumentation have proven their reliability in long-term deployments.
However, it's important to note that while Gr4 titanium wire exhibits exceptional long-term performance in marine environments, proper design, installation, and maintenance practices are still crucial. Factors such as stress concentration, crevice corrosion in poorly designed joints, and potential galvanic interactions should be considered in the overall system design to ensure optimal long-term performance.
In conclusion, the long-term effects of marine exposure on Gr4 titanium wire are predominantly positive, with the material maintaining its excellent corrosion resistance, mechanical properties, and overall integrity. These characteristics make it an attractive choice for critical marine applications where long service life, reliability, and minimal maintenance are essential.
At SHAANXI CXMET TECHNOLOGY CO., LTD, we take pride in our extensive product range, which caters to diverse customer needs. Our company is equipped with outstanding production and processing capabilities, ensuring the high quality and precision of our products. We are committed to innovation and continuously strive to develop new products, keeping us at the forefront of our industry. With leading technological development capabilities, we are able to adapt and evolve in a rapidly changing market. Furthermore, we offer customized solutions to meet the specific requirements of our clients. If you are interested in our products or wish to learn more about the intricate details of our offerings, please do not hesitate to contact us at sales@cxmet.com. Our team is always ready to assist you.
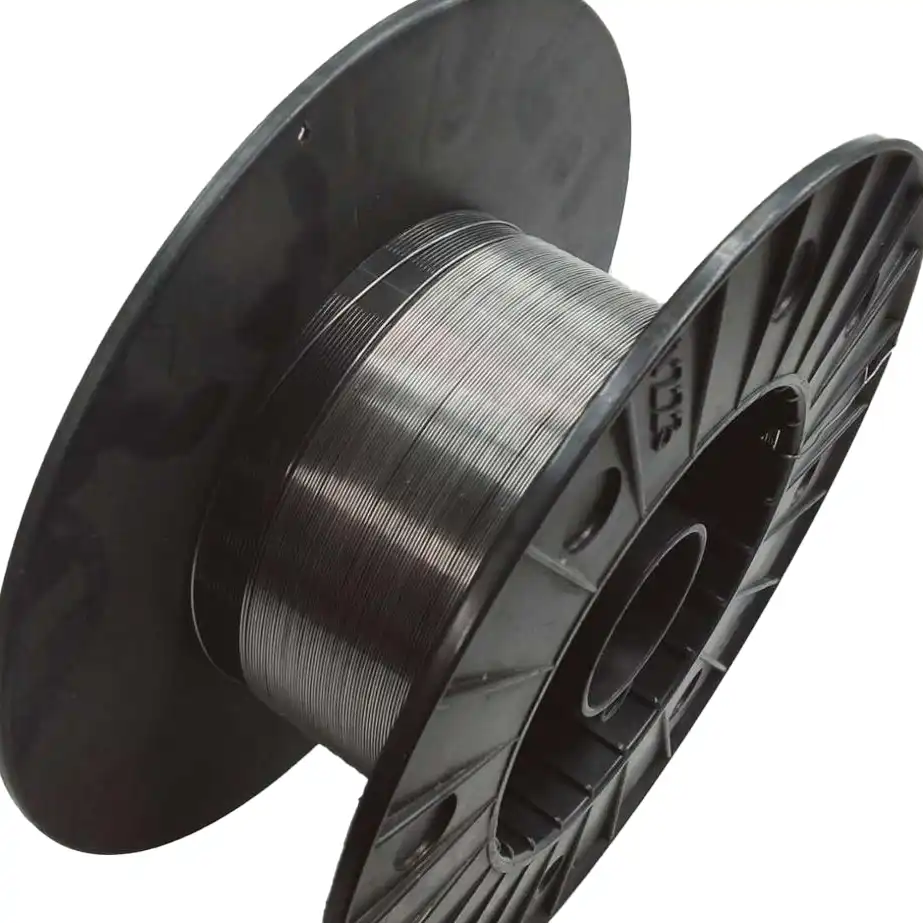
References
- Schutz, R. W., & Thomas, D. E. (1987). Corrosion of titanium and titanium alloys. ASM Handbook, 13, 669-706.
- Revie, R. W., & Uhlig, H. H. (2008). Corrosion and corrosion control: an introduction to corrosion science and engineering. John Wiley & Sons.
- Oldfield, J. W. (1988). Electrochemical theory of galvanic corrosion. Galvanic Corrosion, ASTM International.
- Donachie, M. J. (2000). Titanium: a technical guide. ASM International.
- Schutz, R. W. (2005). Corrosion of titanium and titanium alloys. Corrosion: Materials, 13, 252-299.
- Schillmoller, C. M. (1992). Selection and performance of stainless steels and other nickel-bearing alloys in sulphuric acid. Nickel Development Institute.
- Banerjee, D., & Williams, J. C. (2013). Perspectives on titanium science and technology. Acta Materialia, 61(3), 844-879.
- Schutz, R. W., & Watkins, M. (1998). Recent developments in titanium alloy application in the energy industry. Materials Science and Engineering: A, 243(1-2), 305-315.
- Peters, M., Kumpfert, J., Ward, C. H., & Leyens, C. (2003). Titanium alloys for aerospace applications. Advanced Engineering Materials, 5(6), 419-427.
- Schütze, M., Roche, M., & Bender, R. (2019). Corrosion resistance of steels, nickel alloys, and titanium in aqueous media. John Wiley & Sons.