Molybdenum bars are essential components in various industrial applications, known for their high strength, excellent thermal conductivity, and resistance to corrosion. The manufacturing process of molybdenum bars involves several complex steps, from raw material extraction to the final product. This blog post will explore the intricacies of molybdenum bar production, covering the key stages and techniques used in the industry.
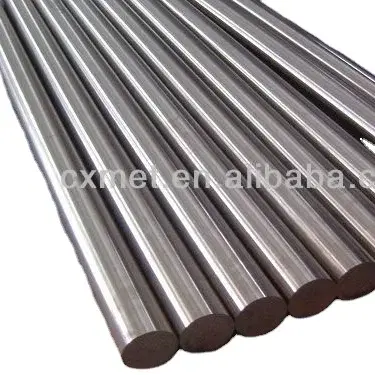
What are the properties of molybdenum that make it suitable for bar production?
Molybdenum possesses a unique set of properties that make it an ideal material for bar production and various industrial applications. These properties include:
- High melting point: Molybdenum has a melting point of 2,623°C (4,753°F), one of the highest among all elements. This characteristic makes it suitable for use in high-temperature environments, such as furnace components and rocket nozzles.
- Excellent strength and hardness: Molybdenum exhibits exceptional strength-to-weight ratio and maintains its strength at elevated temperatures. This property is crucial for applications in aerospace, defense, and power generation industries.
- Low thermal expansion: The material's low coefficient of thermal expansion ensures dimensional stability across a wide range of temperatures, making it ideal for precision components and measuring instruments.
- High thermal and electrical conductivity: Molybdenum's excellent thermal and electrical conductivity properties make it suitable for use in electrical contacts, heat sinks, and other electronic applications.
- Corrosion resistance: Molybdenum demonstrates good resistance to various corrosive environments, including molten metals and aggressive chemicals, making it valuable in chemical processing and metallurgy.
These properties contribute to the versatility of molybdenum bars in numerous industries, including aerospace, electronics, energy, and metallurgy. The unique combination of high-temperature strength, corrosion resistance, and thermal stability makes molybdenum an indispensable material for many critical applications.
What are the main steps in the molybdenum bar manufacturing process?
The production of molybdenum bars involves several key steps, each crucial to achieving the desired quality and properties of the final product. The main steps in the manufacturing process include:
- Raw material extraction: The process begins with the mining of molybdenum-bearing ores, primarily molybdenite (MoS2). These ores are extracted through open-pit or underground mining techniques.
- Ore processing and concentration: The mined ore undergoes crushing, grinding, and flotation to separate molybdenite from other minerals. This process results in a concentrated molybdenum sulfide.
- Roasting: The concentrated molybdenum sulfide is roasted in air at high temperatures (500-700°C) to convert it into molybdenum trioxide (MoO3).
- Reduction: Molybdenum trioxide is then reduced to pure molybdenum powder using hydrogen gas at temperatures ranging from 1000-1200°C. This step is often carried out in multiple stages to ensure complete reduction.
- Powder preparation: The reduced molybdenum powder is carefully processed to achieve the desired particle size distribution and purity levels required for bar production.
- Powder compaction: The molybdenum powder is compacted into green bars using hydraulic presses or cold isostatic pressing (CIP) techniques. This step creates a dense, uniform structure in the material.
- Sintering: The compacted green bars are sintered in hydrogen atmosphere furnaces at temperatures close to the melting point of molybdenum (typically 2000-2200°C). This process bonds the powder particles together, increasing density and strength.
- Hot working: The sintered bars may undergo hot working processes such as forging, rolling, or extrusion to further improve their mechanical properties and achieve the desired shape and dimensions.
- Heat treatment: Depending on the specific application requirements, the molybdenum bars may undergo various heat treatment processes to optimize their microstructure and properties.
- Finishing: The final step involves machining, grinding, or other finishing operations to achieve the required surface finish and dimensional tolerances.
Each of these steps is carefully controlled to ensure the production of high-quality molybdenum bars with consistent properties. The specific parameters and techniques used may vary depending on the manufacturer and the intended application of the molybdenum bars.
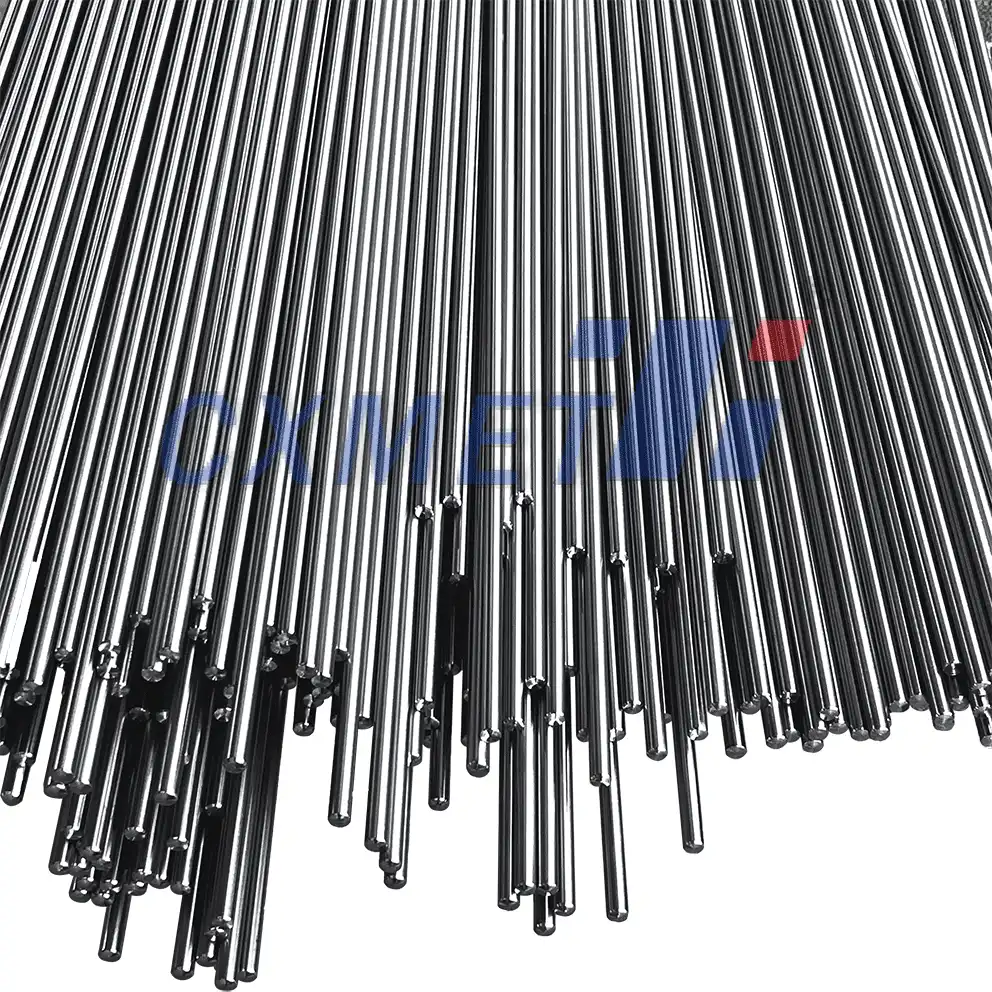
How do different manufacturing methods affect the properties of molybdenum bars?
The manufacturing methods employed in the production of molybdenum bars can significantly influence their final properties and performance characteristics. Different techniques and processing parameters can lead to variations in microstructure, mechanical properties, and overall quality of the molybdenum bars. Some of the key manufacturing methods and their effects on molybdenum bar properties include:
- Powder metallurgy vs. melting and casting:
- Powder metallurgy: This method, which involves compacting and sintering molybdenum powder, typically results in a more uniform microstructure and better control over grain size. Molybdenum bars produced through powder metallurgy often exhibit higher strength and improved ductility at room temperature.
- Melting and casting: While less common due to molybdenum's high melting point, this method can produce larger ingots. However, it may lead to segregation issues and a less uniform microstructure compared to powder metallurgy techniques.
- Sintering conditions:
- Temperature: Higher sintering temperatures generally result in increased density and grain growth. This can lead to improved mechanical properties but may also reduce ductility.
- Time: Longer sintering times can enhance densification and promote grain growth, potentially increasing strength but potentially reducing toughness.
- Atmosphere: Sintering in a hydrogen atmosphere helps prevent oxidation and ensures purity, while vacuum sintering may be used for specific applications.
- Hot working techniques:
- Forging: This process can improve the mechanical properties of molybdenum bars by refining the grain structure and increasing density. Forged bars often exhibit higher strength and better isotropy compared to as-sintered bars.
- Rolling: Hot rolling can produce molybdenum bars with a more refined grain structure and improved strength in the rolling direction. However, it may also introduce anisotropy in the material properties.
- Extrusion: This method can create molybdenum bars with a highly uniform cross-section and good surface finish. Extruded bars may exhibit enhanced strength and ductility due to the severe plastic deformation involved in the process.
- Heat treatment:
- Recrystallization: Controlled heat treatment can induce recrystallization, leading to a more uniform grain structure and improved ductility. This is particularly important for molybdenum bars that have undergone extensive cold working.
- Stress relief: Heat treatment can be used to relieve internal stresses in molybdenum bars, improving dimensional stability and reducing the risk of warpage or distortion during use.
- Alloying and doping:
- Addition of small amounts of other elements (e.g., lanthanum oxide, titanium, or zirconium) during the powder preparation stage can significantly affect the properties of molybdenum bars. These additions can improve high-temperature strength, creep resistance, and recrystallization behavior.
The choice of manufacturing method and processing parameters depends on the specific requirements of the end application. For instance, aerospace components may require molybdenum bars with exceptional high-temperature strength and creep resistance, while electrical applications may prioritize conductivity and purity. By carefully selecting and optimizing the manufacturing process, producers can tailor the properties of molybdenum bars to meet the diverse needs of various industries.
In conclusion, the manufacturing of molybdenum bars is a complex process that requires careful control and optimization at each stage. From the initial extraction of molybdenum ore to the final finishing operations, each step plays a crucial role in determining the quality and properties of the finished product. By understanding the intricacies of the manufacturing process and the effects of different production methods, engineers and manufacturers can continue to improve the performance and versatility of molybdenum bars, ensuring their continued importance in advanced technological applications.
At SHAANXI CXMET TECHNOLOGY CO., LTD, we take pride in our extensive product range, which caters to diverse customer needs. Our company is equipped with outstanding production and processing capabilities, ensuring the high quality and precision of our products. We are committed to innovation and continuously strive to develop new products, keeping us at the forefront of our industry. With leading technological development capabilities, we are able to adapt and evolve in a rapidly changing market. Furthermore, we offer customized solutions to meet the specific requirements of our clients. If you are interested in our products or wish to learn more about the intricate details of our offerings, please do not hesitate to contact us at sales@cxmet.com. Our team is always ready to assist you.
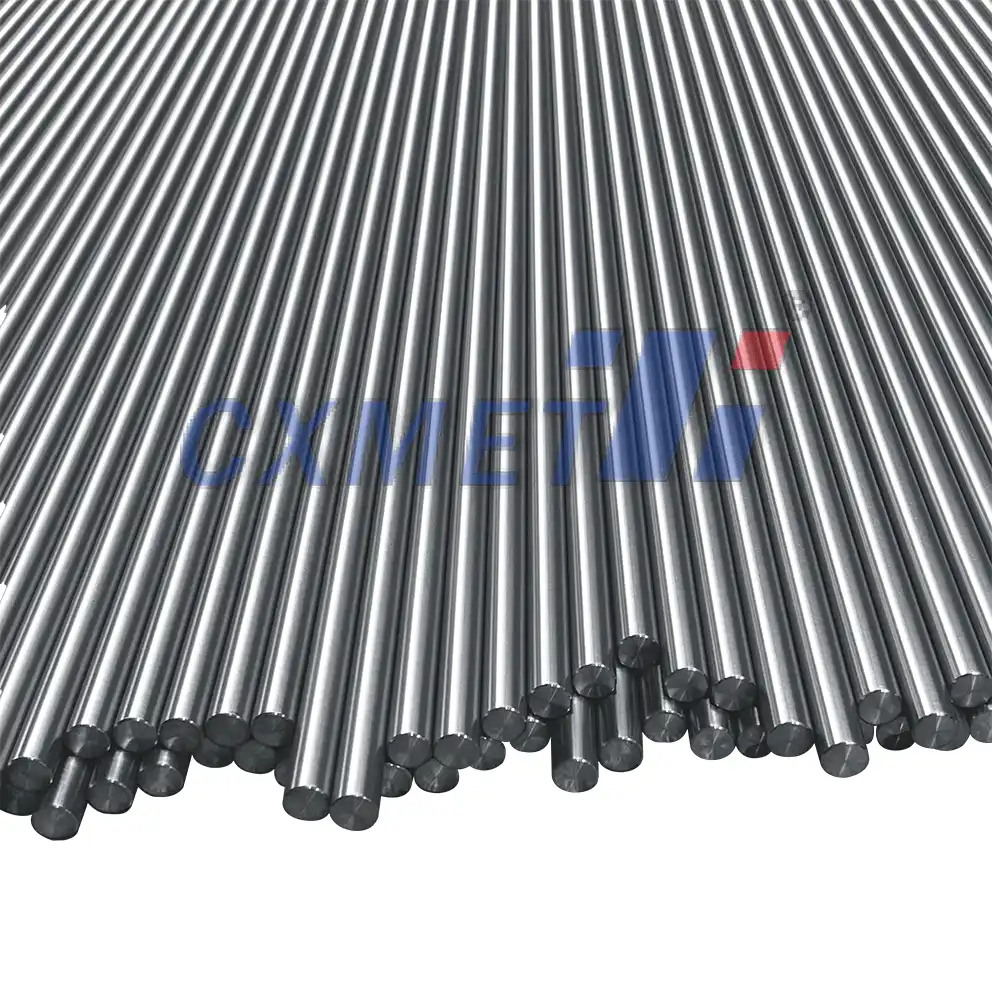
References
1. Lassner, E., & Schubert, W. D. (1999). Tungsten: properties, chemistry, technology of the element, alloys, and chemical compounds. Springer Science & Business Media.
2. ASM International. (2006). ASM Handbook, Volume 7: Powder Metal Technologies and Applications. ASM International.
3. Cockeram, B. V. (2002). The role of stress state on the fracture toughness and toughening mechanisms of wrought molybdenum and molybdenum alloys. Materials Science and Engineering: A, 354(1-2), 83-95.
4. Primig, S., Leitner, H., Clemens, H., Lorich, A., Knabl, W., & Stickler, R. (2010). On the recrystallization behavior of technically pure molybdenum. International Journal of Refractory Metals and Hard Materials, 28(6), 703-708.
5. Shields, J. A. (2013). Applications of molybdenum metal and its alloys. International Molybdenum Association.
6. Shen, Y., Wang, Z., Zhang, X., & Li, Y. (2015). Microstructure and mechanical properties of pure molybdenum processed by equal channel angular pressing. Materials Science and Engineering: A, 648, 134-142.