Gr23 ERTi-23 Medical Titanium Wire is a highly specialized material used in various medical applications, particularly in orthopedic and dental implants. This titanium alloy is known for its exceptional biocompatibility, corrosion resistance, and mechanical properties, making it an ideal choice for medical devices and implants. In this blog post, we will explore the key properties of Gr23 ERTi-23 medical titanium wire and discuss its applications in the medical field.
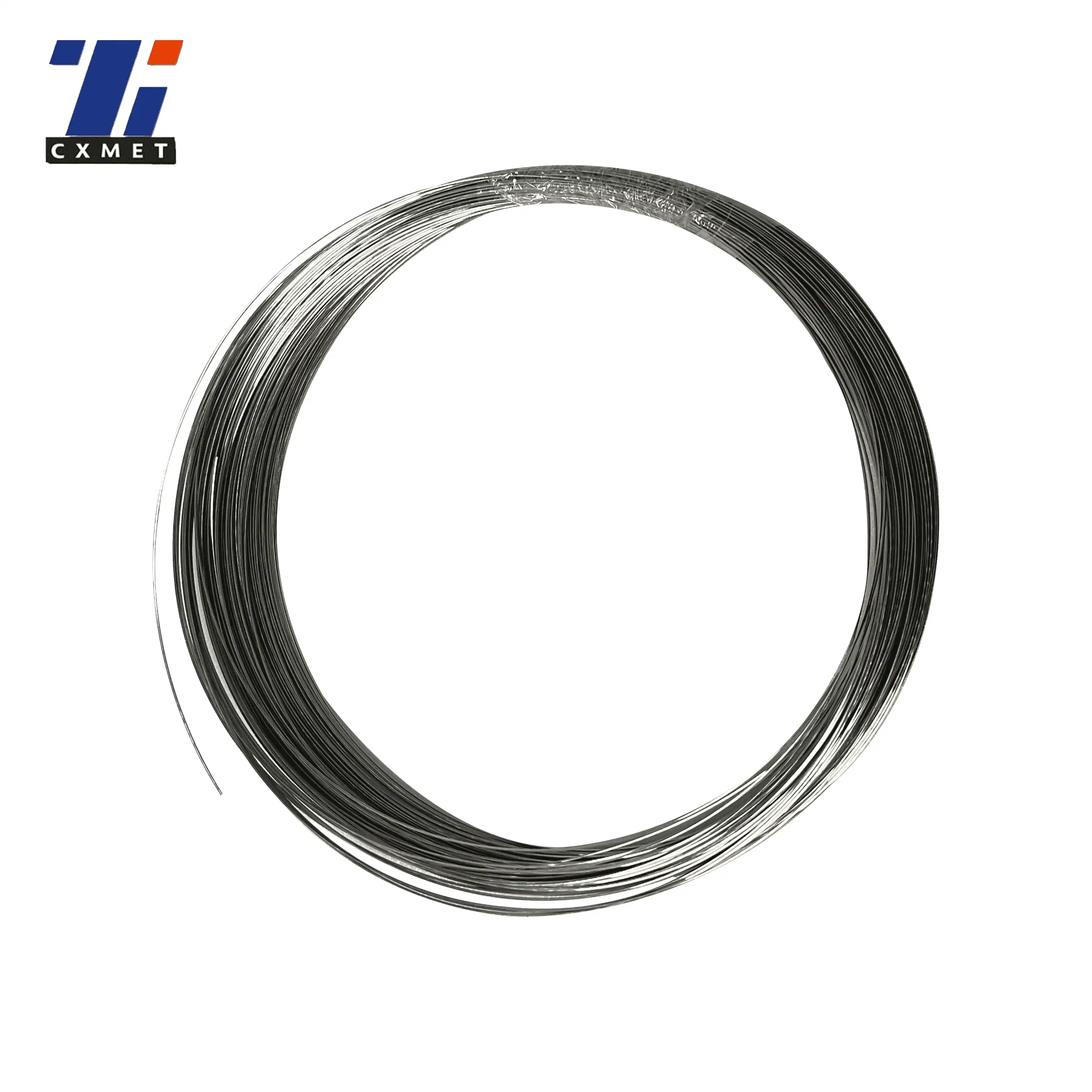
How does Gr23 ERTi-23 titanium wire compare to other medical-grade materials?
Gr23 ERTi-23 Medical Titanium Wire stands out among medical-grade materials due to its unique combination of properties. When compared to other materials commonly used in medical applications, such as stainless steel or cobalt-chromium alloys, Gr23 ERTi-23 titanium wire offers several advantages:
- Biocompatibility: Gr23 ERTi-23 titanium wire exhibits excellent biocompatibility, meaning it is well-tolerated by the human body and does not cause adverse reactions. This property is crucial for medical implants and devices that come into direct contact with living tissues. The material's ability to integrate with bone tissue, known as osseointegration, makes it particularly suitable for orthopedic and dental implants.
- Corrosion resistance: Titanium alloys, including Gr23 ERTi-23, are known for their superior corrosion resistance. This property is essential in medical applications, as it prevents the release of harmful metal ions into the body and ensures the longevity of the implant or device. The corrosion resistance of Gr23 ERTi-23 titanium wire is significantly higher than that of stainless steel and comparable to that of more expensive cobalt-chromium alloys.
- Mechanical properties: Gr23 ERTi-23 titanium wire offers an excellent balance of strength and flexibility. Its high strength-to-weight ratio allows for the creation of lightweight yet durable medical devices and implants. This property is particularly beneficial in applications where weight reduction is crucial, such as in joint replacements or spinal implants.
- Low modulus of elasticity: Compared to other metallic materials used in medical applications, Gr23 ERTi-23 titanium wire has a lower modulus of elasticity, which is closer to that of human bone. This characteristic helps reduce stress shielding, a phenomenon where the implant takes on most of the load, leading to bone resorption and potential implant failure.
- Non-magnetic properties: Unlike some stainless steel alloys, Gr23 ERTi-23 titanium wire is non-magnetic, making it compatible with magnetic resonance imaging (MRI) procedures. This property is crucial for patients who may require post-operative imaging or long-term monitoring.
These properties make Gr23 ERTi-23 titanium wire an excellent choice for various medical applications, including orthopedic implants, dental implants, cardiovascular devices, and surgical instruments. Its superior performance in terms of biocompatibility, corrosion resistance, and mechanical properties often justifies its higher cost compared to other medical-grade materials.
What are the main applications of Gr23 ERTi-23 titanium wire in medical devices?
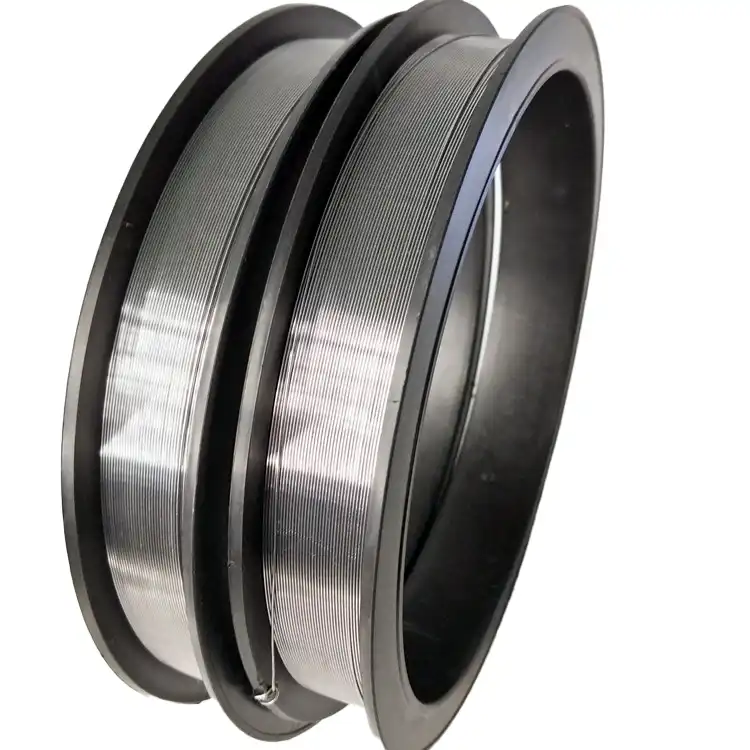
Gr23 ERTi-23 Medical Titanium Wire finds applications in a wide range of medical devices and implants due to its exceptional properties. Some of the main applications include:
- Orthopedic implants: Gr23 ERTi-23 titanium wire is extensively used in various orthopedic implants, such as:
- Joint replacements (hip, knee, shoulder)
- Spinal fusion cages and rods
- Bone plates and screws
- Intramedullary nails
- External fixation devices
The material's biocompatibility, strength, and low modulus of elasticity make it ideal for these applications, promoting bone integration and reducing the risk of implant failure.
- Dental implants: Gr23 ERTi-23 titanium wire is commonly used in dental implants due to its excellent osseointegration properties. It is used to create:
- Dental implant screws
- Abutments
- Crowns and bridges
The material's corrosion resistance and biocompatibility ensure long-lasting and well-integrated dental restorations.
- Cardiovascular devices: The non-magnetic and biocompatible nature of Gr23 ERTi-23 titanium wire makes it suitable for various cardiovascular applications, including:
- Stents
- Heart valve components
- Pacemaker leads
- Artificial heart components
These devices benefit from the material's corrosion resistance and long-term stability in the body.
- Surgical instruments: Gr23 ERTi-23 titanium wire is used to manufacture various surgical instruments due to its strength, lightweight nature, and resistance to repeated sterilization. Examples include:
- Surgical scissors
- Forceps
- Retractors
- Surgical staples
The material's durability and corrosion resistance ensure the longevity of these instruments.
- Maxillofacial and craniofacial implants: Gr23 ERTi-23 titanium wire is used in the fabrication of custom implants for facial reconstruction and skull repair. Its ability to be shaped into complex forms while maintaining strength makes it ideal for these applications.
- Prosthetic components: The material is used in various prosthetic devices, such as artificial limbs and joints, where its lightweight nature and strength provide improved comfort and functionality for patients.
The versatility of Gr23 ERTi-23 titanium wire in medical applications stems from its unique combination of properties, which allow it to meet the diverse requirements of different medical devices and implants. Its use continues to expand as new medical technologies and techniques are developed, further solidifying its position as a crucial material in the medical field.
What are the manufacturing processes used to produce Gr23 ERTi-23 titanium wire?
The production of Gr23 ERTi-23 Medical Titanium Wire involves several sophisticated manufacturing processes to ensure the material meets the stringent requirements for medical applications. These processes are designed to achieve the desired mechanical properties, dimensional accuracy, and surface quality. The main manufacturing processes used to produce Gr23 ERTi-23 titanium wire include:
- Melting and ingot formation: The process begins with the melting of high-purity titanium and alloying elements in a vacuum or inert atmosphere to prevent contamination. The molten metal is then cast into ingots using various techniques such as vacuum arc remelting (VAR) or electron beam melting (EBM). These methods ensure the removal of impurities and the achievement of a homogeneous composition.
- Hot working: The ingots are then subjected to hot working processes, such as forging or extrusion, to break down the as-cast structure and improve the material's mechanical properties. This step helps in achieving a more uniform grain structure and enhancing the overall strength of the material.
- Cold working: After hot working, the material undergoes cold working processes, which may include drawing or rolling. These processes further refine the grain structure and increase the strength and hardness of the wire. Cold working also helps in achieving the desired dimensional accuracy.
- Heat treatment: Heat treatment processes, such as annealing or age hardening, are employed to optimize the mechanical properties of the wire. These treatments can help in relieving internal stresses, improving ductility, or increasing strength, depending on the specific requirements of the end application.
- Surface treatment: Various surface treatments may be applied to enhance the wire's properties or prepare it for specific applications. These treatments can include:
- Electropolishing to improve surface smoothness and corrosion resistance
- Anodizing to create a protective oxide layer
- Coating with bioactive materials to enhance osseointegration in certain implant applications
- Quality control and testing: Throughout the manufacturing process, rigorous quality control measures are implemented to ensure the wire meets the required specifications. This includes:
- Chemical composition analysis
- Mechanical property testing (tensile strength, yield strength, elongation)
- Microstructure examination
- Dimensional checks
- Surface quality inspection
- Packaging and sterilization: For medical applications, the wire is often packaged in clean room environments and may undergo sterilization processes such as gamma irradiation or ethylene oxide treatment to ensure it is ready for use in medical devices or implants.
The manufacturing processes for Gr23 ERTi-23 titanium wire are carefully controlled and optimized to produce a material that meets the stringent requirements of the medical industry. Advances in manufacturing technologies, such as additive manufacturing or 3D printing, are also being explored for the production of complex titanium alloy components, potentially offering new possibilities for customized medical devices and implants.
In conclusion, Gr23 ERTi-23 Medical Titanium Wire is a remarkable material that has revolutionized the field of medical implants and devices. Its unique combination of biocompatibility, corrosion resistance, and mechanical properties make it an ideal choice for a wide range of medical applications. As research and development in medical technologies continue to advance, the importance of materials like Gr23 ERTi-23 titanium wire is likely to grow, leading to further improvements in patient care and outcomes.
At SHAANXI CXMET TECHNOLOGY CO., LTD, we take pride in our extensive product range, which caters to diverse customer needs. Our company is equipped with outstanding production and processing capabilities, ensuring the high quality and precision of our products. We are committed to innovation and continuously strive to develop new products, keeping us at the forefront of our industry. With leading technological development capabilities, we are able to adapt and evolve in a rapidly changing market. Furthermore, we offer customized solutions to meet the specific requirements of our clients. If you are interested in our products or wish to learn more about the intricate details of our offerings, please do not hesitate to contact us at sales@cxmet.com. Our team is always ready to assist you.
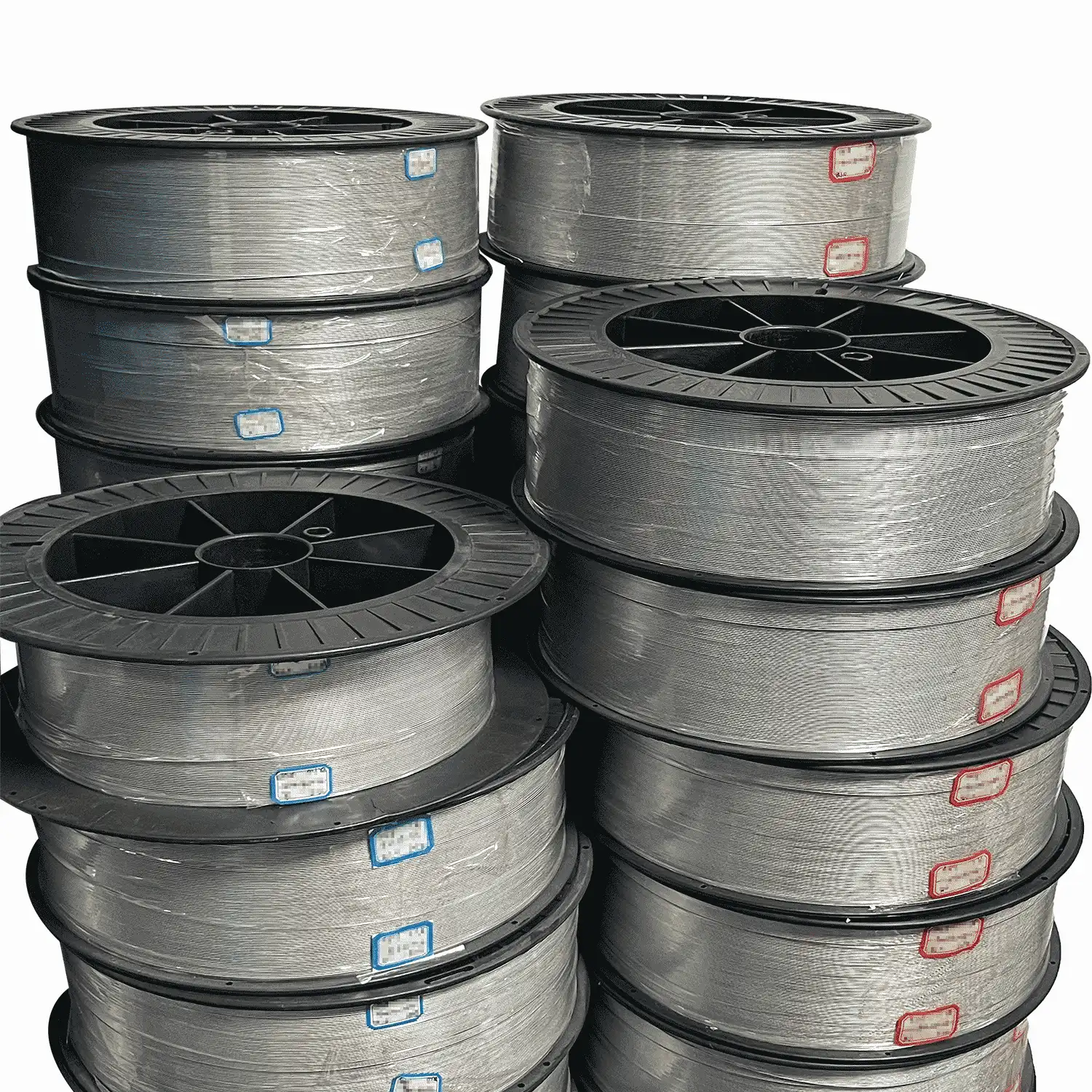
References
- Rack, H. J., & Qazi, J. I. (2006). Titanium alloys for biomedical applications. Materials Science and Engineering: C, 26(8), 1269-1277.
- Niinomi, M. (2008). Mechanical biocompatibilities of titanium alloys for biomedical applications. Journal of the mechanical behavior of biomedical materials, 1(1), 30-42.
- Elias, C. N., Lima, J. H. C., Valiev, R., & Meyers, M. A. (2008). Biomedical applications of titanium and its alloys. Jom, 60(3), 46-49.
- Geetha, M., Singh, A. K., Asokamani, R., & Gogia, A. K. (2009). Ti based biomaterials, the ultimate choice for orthopaedic implants–a review. Progress in materials science, 54(3), 397-425.
- Chen, Q., & Thouas, G. A. (2015). Metallic implant biomaterials. Materials Science and Engineering: R: Reports, 87, 1-57.
- Sidambe, A. T. (2014). Biocompatibility of advanced manufactured titanium implants—A review. Materials, 7(12), 8168-8188.
- Bauer, S., Schmuki, P., von der Mark, K., & Park, J. (2013). Engineering biocompatible implant surfaces: Part I: Materials and surfaces. Progress in materials science, 58(3), 261-326.
- Liu, X., Chu, P. K., & Ding, C. (2004). Surface modification of titanium, titanium alloys, and related materials for biomedical applications. Materials Science and Engineering: R: Reports, 47(3-4), 49-121.
- Bandyopadhyay, A., & Bose, S. (Eds.). (2013). Characterization of biomaterials. Newnes.
- Brunette, D. M., Tengvall, P., Textor, M., & Thomsen, P. (Eds.). (2012). Titanium in medicine: material science, surface science, engineering, biological responses and medical applications. Springer Science & Business Media.