Ti3AL2.5VTitanium Alloy tube are widely used in aerospace, chemical processing, and medical industries due to their excellent strength-to-weight ratio, corrosion resistance, and biocompatibility. Understanding the welding characteristics of these tubes is crucial for ensuring the integrity and performance of structures and components made from this alloy. This blog post will explore the unique welding properties of Ti3Al2.5V titanium alloy tubes, discussing the challenges, techniques, and best practices for achieving high-quality welds.
What are the recommended welding techniques for Ti3Al2.5V titanium alloy tubes?
When it comes to welding Ti3AL2.5VTitanium Alloy tube, several techniques have proven to be effective. The choice of welding method depends on factors such as the tube thickness, desired joint properties, and application requirements. Here are some of the most recommended welding techniques for Ti3Al2.5V titanium alloy tubes:
- Gas Tungsten Arc Welding (GTAW): Also known as TIG welding, this method is widely used for welding Ti3Al2.5V titanium alloy tubes. GTAW offers excellent control over the weld pool and produces high-quality, clean welds. It is particularly suitable for thin-walled tubes and applications requiring precise, aesthetically pleasing welds. The process uses a non-consumable tungsten electrode and an inert shielding gas, typically argon, to protect the weld area from atmospheric contamination.
- Electron Beam Welding (EBW): This advanced welding technique is ideal for joining Ti3Al2.5V titanium alloy tubes in applications demanding high precision and minimal heat-affected zones. EBW uses a focused beam of high-velocity electrons to melt and join the materials. The process is carried out in a vacuum chamber, which eliminates the need for shielding gas and provides excellent protection against atmospheric contamination. EBW is particularly useful for welding thick-walled tubes and achieving deep penetration welds.
- Laser Beam Welding (LBW): This method uses a high-energy laser beam to melt and fuse the Ti3Al2.5V titanium alloy. LBW offers advantages such as high welding speeds, minimal distortion, and the ability to weld in hard-to-reach areas. It is well-suited for automated production processes and can produce narrow, deep welds with minimal heat input. LBW is often used for joining thin-walled tubes and creating hermetic seals in critical applications.
- Plasma Arc Welding (PAW): PAW is a variation of GTAW that uses a constricted plasma arc to achieve higher energy density and deeper penetration. This technique is particularly useful for welding thicker Ti3Al2.5V titanium alloy tubes and can produce high-quality welds at faster speeds compared to conventional GTAW.
Regardless of the chosen welding technique, it is crucial to maintain a clean, contamination-free environment during the welding process. Ti3Al2.5V titanium alloy is highly reactive at elevated temperatures and can easily absorb atmospheric gases, leading to embrittlement and reduced weld quality. Therefore, proper shielding and meticulous cleaning procedures are essential for achieving optimal results.
How does the microstructure of Ti3Al2.5V titanium alloy affect its weldability?
The microstructure of Ti3AL2.5VTitanium Alloy tube plays a significant role in determining its weldability and the properties of the welded joint. Understanding the relationship between microstructure and weldability is crucial for optimizing welding parameters and achieving desired mechanical properties in the final welded component.
Ti3Al2.5V is an alpha-beta titanium alloy, meaning its microstructure consists of a mixture of alpha (hexagonal close-packed) and beta (body-centered cubic) phases. The presence of both phases contributes to the alloy's unique characteristics and affects its behavior during welding:
- Phase Transformation: During welding, the heat input causes localized melting and subsequent solidification of the material. As the weld cools, the beta phase transforms back to alpha phase. The rate of cooling and the presence of alloying elements influence the final microstructure of the weld and heat-affected zone (HAZ). Rapid cooling can lead to the formation of martensitic alpha prime (α') phase, which can affect the mechanical properties of the welded joint.
- Grain Growth: The heat input during welding can cause grain growth in the HAZ, potentially leading to a reduction in strength and ductility. The extent of grain growth depends on factors such as heat input, welding speed, and initial grain size of the base material. Controlling these parameters is essential for maintaining desirable mechanical properties in the welded joint.
- Texture Development: Welding can induce changes in the crystallographic texture of Ti3Al2.5V titanium alloy. The development of specific textures can influence the mechanical properties and performance of the welded component, particularly in applications where directional properties are important.
- Interstitial Element Absorption: The high reactivity of titanium at elevated temperatures makes it susceptible to absorption of interstitial elements such as oxygen, nitrogen, and hydrogen. These elements can significantly affect the microstructure and mechanical properties of the weld. Proper shielding and control of the welding environment are crucial to minimize interstitial element absorption and maintain the desired microstructure.
To optimize the weldability of Ti3Al2.5V titanium alloy tubes and achieve the desired microstructure in the welded joint, several strategies can be employed:
- Controlling heat input and cooling rates to manage phase transformations and grain growth
- Using pulsed welding techniques to promote finer grain structures in the weld and HAZ
- Implementing post-weld heat treatments to optimize the microstructure and relieve residual stresses
- Carefully selecting filler materials that are compatible with the base metal composition and desired final properties
- Employing advanced process monitoring and control systems to ensure consistent welding parameters and minimize microstructural variations
By considering the microstructural aspects of Ti3Al2.5V titanium alloy and implementing appropriate welding strategies, it is possible to achieve high-quality welds with optimal mechanical properties and performance characteristics.
What are the common challenges in welding Ti3Al2.5V titanium alloy tubes?
Welding Ti3AL2.5VTitanium Alloy tube presents several challenges that must be addressed to ensure high-quality, reliable welds. Understanding these challenges is crucial for developing effective welding procedures and implementing appropriate mitigation strategies. Some of the most common challenges in welding Ti3Al2.5V titanium alloy tubes include:
- Atmospheric Contamination: Ti3Al2.5V titanium alloy is highly reactive at elevated temperatures and can easily absorb atmospheric gases such as oxygen, nitrogen, and hydrogen. This contamination can lead to embrittlement, reduced ductility, and decreased corrosion resistance in the welded joint. To address this challenge:
- Use high-purity shielding gases (typically argon) and maintain proper gas flow rates
- Implement effective shielding techniques, including trailing shields and purge gases for the tube interior
- Ensure a clean welding environment and properly clean the base material and filler wire before welding
- Consider using vacuum or inert-atmosphere welding chambers for critical applications
- Heat-Affected Zone (HAZ) Embrittlement: The heat input during welding can cause microstructural changes in the HAZ, potentially leading to reduced ductility and increased susceptibility to cracking. To mitigate this issue:
- Optimize welding parameters to minimize heat input while maintaining adequate penetration
- Use pulsed welding techniques to control heat input and promote finer grain structures
- Implement post-weld heat treatments to improve the microstructure and mechanical properties of the HAZ
- Consider using advanced welding processes with highly focused heat sources, such as electron beam or laser welding, to minimize the HAZ
- Distortion and Residual Stresses: The low thermal conductivity and high coefficient of thermal expansion of Ti3Al2.5V titanium alloy can lead to significant distortion and residual stresses during welding. These issues can affect the dimensional accuracy and fatigue performance of welded components. To address this challenge:
- Implement proper fixturing and clamping techniques to minimize distortion
- Use balanced welding sequences and techniques to distribute heat input evenly
- Consider employing low-stress welding methods, such as friction stir welding, for suitable applications
- Apply post-weld stress relief treatments to reduce residual stresses
- Weld Porosity: Titanium alloys are susceptible to weld porosity, which can significantly reduce the strength and fatigue performance of the welded joint. Porosity can be caused by factors such as contamination, improper shielding, or trapped gases. To minimize porosity:
- Ensure thorough cleaning of the base material and filler wire before welding
- Optimize shielding gas flow rates and nozzle positioning
- Use high-purity shielding gases and filler materials
- Implement proper welding techniques, such as maintaining a stable arc and consistent travel speed
- Control of Weld Bead Profile: Achieving consistent and desirable weld bead profiles can be challenging when welding Ti3Al2.5V titanium alloy tubes, particularly for thin-walled sections. Improper bead profiles can lead to stress concentrations and reduced joint performance. To address this issue:
- Optimize welding parameters, including current, voltage, and travel speed, to achieve the desired bead profile
- Use pulsed welding techniques to control the weld pool and improve bead geometry
- Implement automated welding systems for improved consistency and repeatability
- Consider using specialized joint designs and preparation techniques to promote optimal bead profiles
By addressing these common challenges through careful planning, process optimization, and implementation of best practices, it is possible to achieve high-quality, reliable welds in Ti3AL2.5VTitanium Alloy tube. Continuous improvement in welding techniques, equipment, and process control will further enhance the weldability of this important alloy, enabling its broader use in critical applications across various industries.
At SHAANXI CXMET TECHNOLOGY CO., LTD, we take pride in our extensive product range, which caters to diverse customer needs. Our company is equipped with outstanding production and processing capabilities, ensuring the high quality and precision of our products. We are committed to innovation and continuously strive to develop new products, keeping us at the forefront of our industry. With leading technological development capabilities, we are able to adapt and evolve in a rapidly changing market. Furthermore, we offer customized solutions to meet the specific requirements of our clients. If you are interested in our products or wish to learn more about the intricate details of our offerings, please do not hesitate to contact us at sales@cxmet.com. Our team is always ready to assist you.
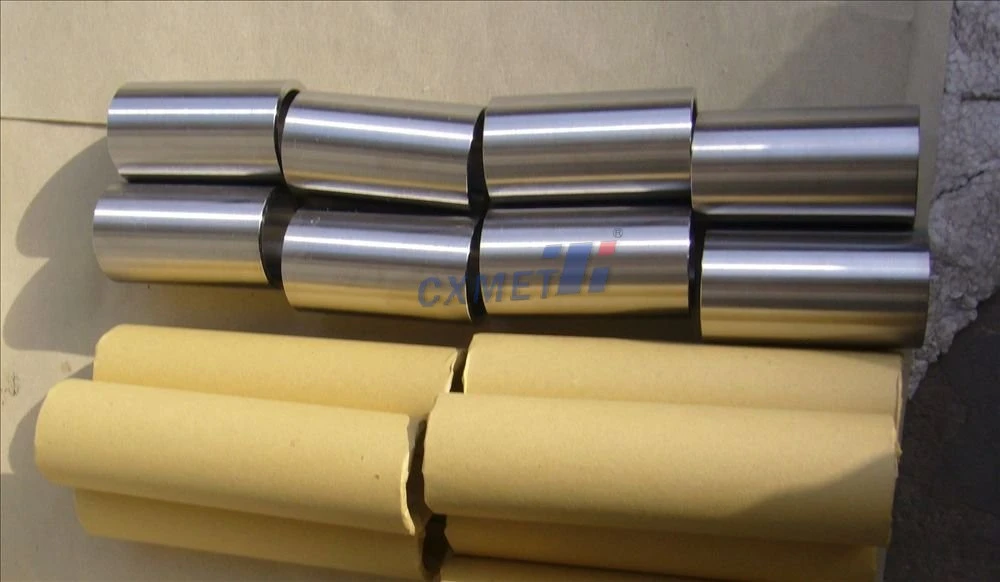
References
- Boyer, R., Welsch, G., & Collings, E. W. (1994). Materials Properties Handbook: Titanium Alloys. ASM International.
- Kou, S. (2003). Welding Metallurgy (2nd ed.). John Wiley & Sons.
- Donachie, M. J. (2000). Titanium: A Technical Guide (2nd ed.). ASM International.
- AWS D1.9/D1.9M:2015, Structural Welding Code - Titanium. American Welding Society.
- Peters, M., Kumpfert, J., Ward, C. H., & Leyens, C. (2003). Titanium alloys for aerospace applications. Advanced Engineering Materials, 5(6), 419-427.
- Lathabai, S., Jarvis, B. L., & Barton, K. J. (2001). Comparison of keyhole and conventional gas tungsten arc welds in commercially pure titanium. Materials Science and Engineering: A, 299(1-2), 81-93.
- Short, A. B. (2009). Gas tungsten arc welding of α + β titanium alloys: a review. Materials Science and Technology, 25(3), 309-324.
- Akman, E., Demir, A., Canel, T., & Sınmazçelik, T. (2009). Laser welding of Ti6Al4V titanium alloys. Journal of Materials Processing Technology, 209(8), 3705-3713.
- Yunlian, Q., Ju, D., Quan, H., & Liying, Z. (2000). Electron beam welding, laser beam welding and gas tungsten arc welding of titanium sheet. Materials Science and Engineering: A, 280(1), 177-181.
- Cao, X., & Jahazi, M. (2009). Effect of welding speed on butt joint quality of Ti–6Al–4V alloy welded using a high-power Nd:YAG laser. Optics and Lasers in Engineering, 47(11), 1231-1241.