Titanium 6Al7Nb Medical Bar, also known as Ti-6Al-7Nb, is an advanced biocompatible alloy widely used in the healthcare industry, particularly in medical implants and devices. This alloy combines the excellent properties of titanium with enhanced biocompatibility and mechanical strength, making it an ideal material for various medical applications. In this blog post, we will explore the diverse applications of Titanium 6Al7Nb medical bars in healthcare and answer some frequently asked questions about this remarkable material.
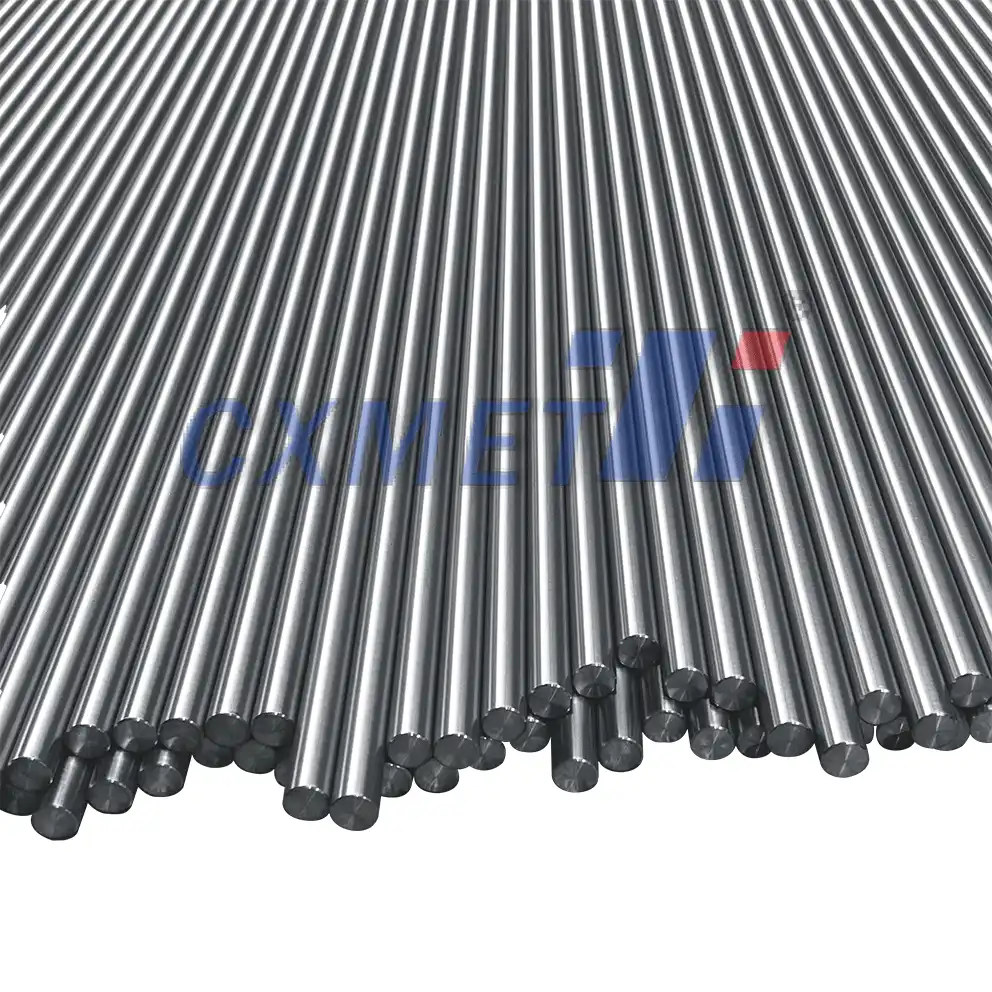
How does Titanium 6Al7Nb compare to other medical-grade alloys?
Titanium 6Al7Nb Medical Bar is a high-performance alloy that offers several advantages over other medical-grade materials. When compared to traditional alloys like stainless steel or cobalt-chromium, Ti-6Al-7Nb exhibits superior properties that make it particularly suitable for medical applications:
- Biocompatibility: One of the most critical factors in selecting materials for medical implants is biocompatibility. Titanium 6Al7Nb demonstrates excellent biocompatibility, meaning it is well-tolerated by the human body and does not cause adverse reactions. This property is attributed to the formation of a stable oxide layer on the surface of the alloy, which prevents corrosion and ion release.
- Mechanical strength: Ti-6Al-7Nb offers high strength-to-weight ratio, making it ideal for load-bearing applications such as orthopedic implants. It provides the necessary strength to withstand the stresses and strains experienced by implants while remaining lightweight, which is crucial for patient comfort and mobility.
- Corrosion resistance: The alloy's excellent corrosion resistance is vital for long-term implant stability. Ti-6Al-7Nb forms a protective oxide layer that prevents degradation in the aggressive biological environment of the human body, ensuring the longevity of medical devices and implants.
- Osseointegration: Titanium 6Al7Nb has been shown to promote osseointegration, which is the direct structural and functional connection between living bone tissue and the surface of an implant. This property is crucial for the success of dental and orthopedic implants, as it ensures a strong and stable bond between the implant and the surrounding bone.
- Low elastic modulus: Compared to other metallic biomaterials, Ti-6Al-7Nb has a relatively low elastic modulus, which is closer to that of human bone. This characteristic helps reduce stress shielding, a phenomenon where the implant takes on most of the load, leading to bone resorption and potential implant failure.
These superior properties make Titanium 6Al7Nb an excellent choice for various medical applications, outperforming many traditional alloys in terms of biocompatibility, mechanical performance, and long-term stability.
What are the main applications of Titanium 6Al7Nb in orthopedic implants?
Titanium 6Al7Nb Medical Bar has found extensive use in orthopedic implants due to its exceptional properties. The alloy's combination of strength, biocompatibility, and osseointegration capabilities makes it an ideal material for various orthopedic applications. Some of the main uses of Ti-6Al-7Nb in orthopedic implants include:
- Joint replacements: Ti-6Al-7Nb is commonly used in hip and knee replacement implants. The alloy's high strength and low elastic modulus make it suitable for the load-bearing components of these prostheses. Its excellent biocompatibility ensures minimal risk of rejection or adverse reactions, while its ability to promote osseointegration contributes to the long-term stability of the implant.
- Spinal implants: Titanium 6Al7Nb is used in various spinal implants, including vertebral body replacements, interbody fusion cages, and pedicle screw systems. The alloy's strength and corrosion resistance are crucial for these applications, as spinal implants must withstand significant loads and maintain their integrity over extended periods.
- Fracture fixation devices: Ti-6Al-7Nb is employed in the manufacturing of plates, screws, and intramedullary nails used for fracture fixation. The alloy's high strength-to-weight ratio allows for the creation of robust yet lightweight devices that provide excellent support during bone healing without causing discomfort to the patient.
- Custom implants: With the advent of 3D printing and additive manufacturing technologies, Ti-6Al-7Nb has become increasingly popular for creating custom-designed implants. These patient-specific implants can be tailored to match the exact anatomy of the individual, providing optimal fit and function.
- Dental implants: Although technically not an orthopedic application, dental implants made from Ti-6Al-7Nb have gained popularity due to the alloy's excellent osseointegration properties and biocompatibility. These implants provide a stable foundation for prosthetic teeth, offering long-term durability and natural-looking results.
The use of Titanium 6Al7Nb in orthopedic implants has significantly improved patient outcomes by providing long-lasting, biocompatible solutions for various musculoskeletal conditions. The alloy's versatility allows for its application in a wide range of orthopedic devices, from large joint replacements to small fixation screws, contributing to enhanced mobility and quality of life for patients worldwide.
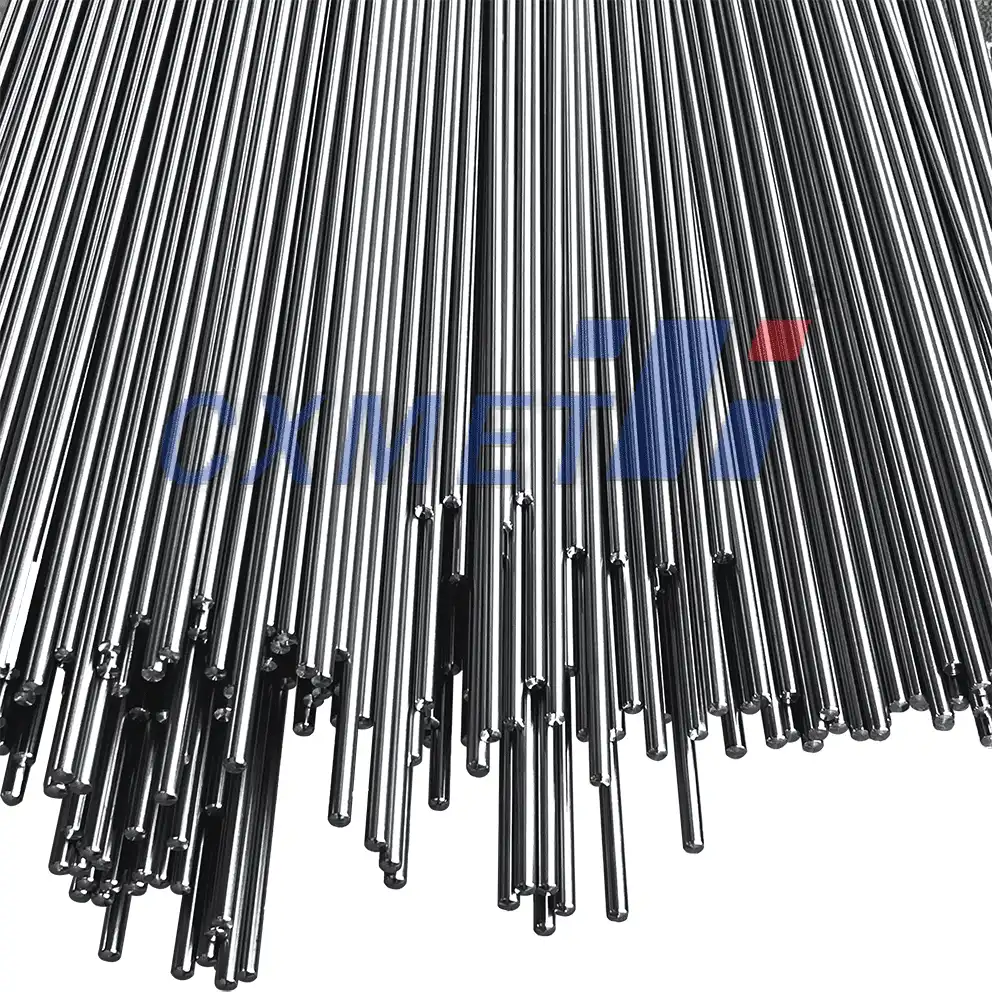
How is Titanium 6Al7Nb processed for medical device manufacturing?
The processing of Titanium 6Al7Nb Medical Bar for medical device manufacturing involves several sophisticated techniques to ensure the final product meets the stringent requirements of the healthcare industry. The following steps outline the typical processing methods used in the production of Ti-6Al-7Nb medical bars and devices:
- Alloy production: The process begins with the creation of the Ti-6Al-7Nb alloy. This involves carefully mixing and melting high-purity titanium with aluminum and niobium in precise proportions. The melting is typically done using vacuum arc remelting (VAR) or electron beam melting (EBM) to ensure the highest purity and homogeneity of the alloy.
- Ingot formation: Once the alloy is melted and mixed, it is cast into ingots. These ingots undergo multiple remelting cycles to further improve the alloy's uniformity and remove any impurities or defects.
- Hot working: The ingots are then subjected to hot working processes such as forging or rolling. This step helps to break down the cast structure and improve the alloy's mechanical properties. Hot working is typically performed at temperatures above the material's recrystallization temperature to ensure optimal formability.
- Cold working: After hot working, the material may undergo cold working processes to further refine its microstructure and enhance its mechanical properties. This step can include operations like drawing or swaging, which help to achieve the desired dimensions and surface finish of the medical bars.
- Heat treatment: Heat treatment is a crucial step in the processing of Ti-6Al-7Nb. Various heat treatment protocols, such as solution treatment and aging, are employed to optimize the alloy's microstructure and mechanical properties. These treatments can significantly influence the material's strength, ductility, and fatigue resistance.
- Surface treatment: To enhance the biocompatibility and osseointegration properties of Ti-6Al-7Nb, various surface treatments may be applied. These can include mechanical treatments like grit blasting or chemical treatments such as acid etching. Advanced surface modification techniques like plasma spraying or anodization may also be used to create specific surface topographies or coatings.
- Machining and forming: The processed Ti-6Al-7Nb bars are then machined and formed into the final shapes required for specific medical devices. This step often involves precision CNC machining, laser cutting, or other advanced manufacturing techniques to achieve the complex geometries needed for medical implants and instruments.
- Additive manufacturing: In recent years, additive manufacturing or 3D printing has emerged as a powerful technique for processing Ti-6Al-7Nb. This method allows for the creation of complex, custom-designed implants with intricate internal structures that can enhance osseointegration and reduce implant weight.
- Quality control and testing: Throughout the manufacturing process, rigorous quality control measures are implemented to ensure the final product meets the required specifications. This includes extensive testing of mechanical properties, chemical composition, and microstructure, as well as biocompatibility testing to confirm the material's suitability for medical use.
- Sterilization: The final step in processing Ti-6Al-7Nb medical devices is sterilization. Various methods such as gamma irradiation, ethylene oxide treatment, or steam sterilization may be used, depending on the specific requirements of the device and its intended use.
The processing of Titanium 6Al7Nb Medical Bar for medical device manufacturing is a complex and highly controlled process that requires specialized equipment and expertise. Each step is carefully monitored and optimized to ensure the final product meets the exacting standards required for medical applications. The result is a high-performance material that can be shaped into a wide range of medical devices, offering excellent biocompatibility, mechanical properties, and long-term stability in the human body.
At SHAANXI CXMET TECHNOLOGY CO., LTD, we take pride in our extensive product range, which caters to diverse customer needs. Our company is equipped with outstanding production and processing capabilities, ensuring the high quality and precision of our products. We are committed to innovation and continuously strive to develop new products, keeping us at the forefront of our industry. With leading technological development capabilities, we are able to adapt and evolve in a rapidly changing market. Furthermore, we offer customized solutions to meet the specific requirements of our clients. If you are interested in our products or wish to learn more about the intricate details of our offerings, please do not hesitate to contact us at sales@cxmet.com. Our team is always ready to assist you.
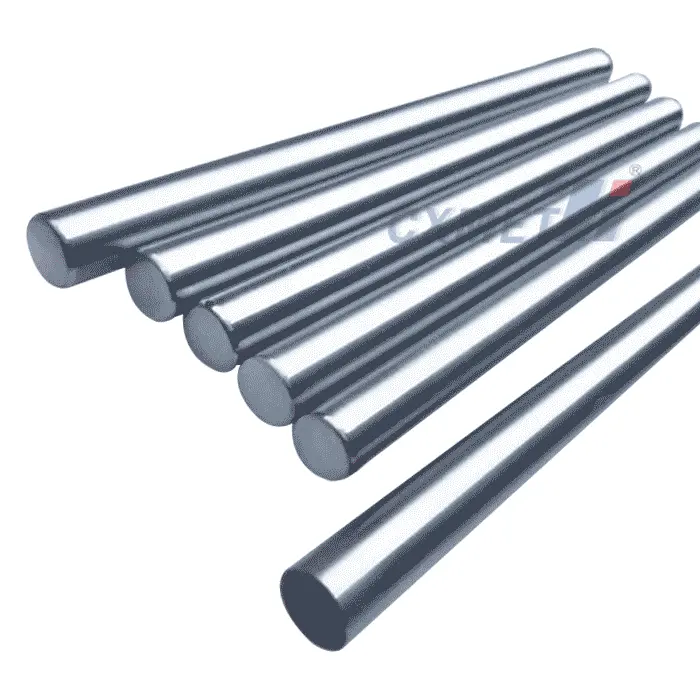
References
- Geetha, M., et al. (2009). Ti based biomaterials, the ultimate choice for orthopaedic implants – A review. Progress in Materials Science, 54(3), 397-425.
- Niinomi, M. (2008). Mechanical biocompatibilities of titanium alloys for biomedical applications. Journal of the Mechanical Behavior of Biomedical Materials, 1(1), 30-42.
- Chen, Q., & Thouas, G. A. (2015). Metallic implant biomaterials. Materials Science and Engineering: R: Reports, 87, 1-57.
- Özcan, M., & Hämmerle, C. (2012). Titanium as a reconstruction and implant material in dentistry: advantages and pitfalls. Materials, 5(9), 1528-1545.
- Rack, H. J., & Qazi, J. I. (2006). Titanium alloys for biomedical applications. Materials Science and Engineering: C, 26(8), 1269-1277.
- Elias, C. N., et al. (2008). Biomedical applications of titanium and its alloys. Jom, 60(3), 46-49.
- Long, M., & Rack, H. J. (1998). Titanium alloys in total joint replacement—a materials science perspective. Biomaterials, 19(18), 1621-1639.
- Banerjee, D., & Williams, J. C. (2013). Perspectives on titanium science and technology. Acta Materialia, 61(3), 844-879.
- Sidambe, A. T. (2014). Biocompatibility of advanced manufactured titanium implants—A review. Materials, 7(12), 8168-8188.
- Bauer, S., et al. (2013). Engineering biocompatible implant surfaces: Part I: Materials and surfaces. Progress in Materials Science, 58(3), 261-326.