Gr11 titanium wire, also known as Grade 11 titanium wire, is a high-performance alloy that combines the strength of titanium with enhanced properties due to its specific composition. This wire is part of the titanium alloy family and is known for its excellent corrosion resistance, high strength-to-weight ratio, and biocompatibility. Gr11 titanium wire is widely used in various industries, including aerospace, medical, and marine applications, due to its unique combination of properties.
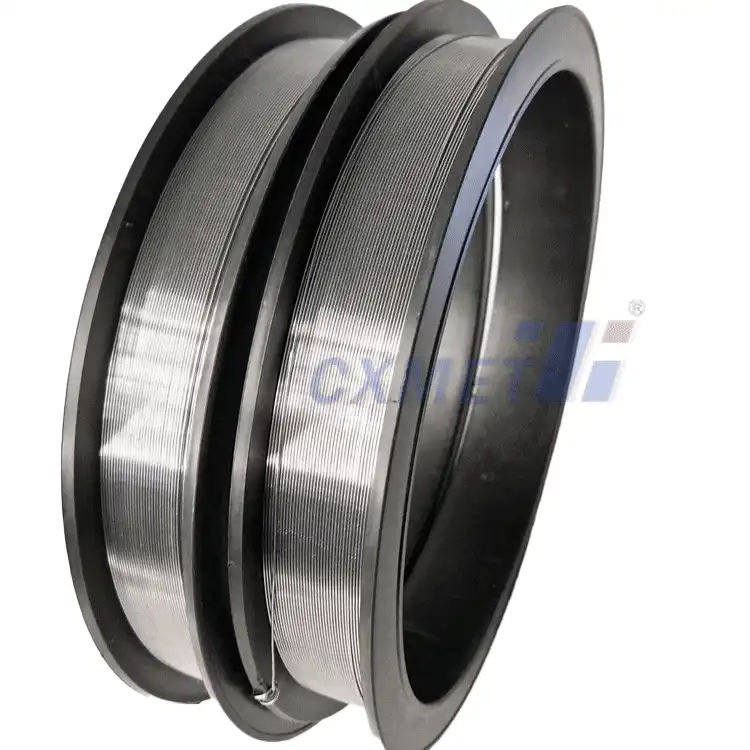
What are the properties of Gr11 titanium wire?
Gr11 titanium wire possesses a range of impressive properties that make it a sought-after material in various applications. Some of the key properties of Gr11 titanium wire include:
- Excellent Corrosion Resistance: Gr11 titanium wire exhibits exceptional resistance to corrosion, even in harsh environments. This property is attributed to the formation of a stable, passive oxide layer on the surface of the wire, which protects it from further oxidation and chemical attack. This makes it ideal for use in marine environments, chemical processing plants, and other corrosive settings.
- High Strength-to-Weight Ratio: Despite being lightweight, Gr11 titanium wire offers impressive strength. This combination of low density and high strength makes it an excellent choice for applications where weight reduction is crucial, such as in aerospace and automotive industries.
- Biocompatibility: Gr11 titanium wire is highly biocompatible, meaning it can be safely used in medical applications without causing adverse reactions in the human body. This property makes it a popular choice for medical implants, surgical instruments, and dental applications.
- Temperature Resistance: Gr11 titanium wire maintains its strength and structural integrity over a wide range of temperatures, making it suitable for use in both cryogenic and high-temperature applications.
- Low Thermal Expansion: The wire exhibits a low coefficient of thermal expansion, which means it maintains its dimensional stability even when subjected to temperature changes. This property is particularly valuable in precision engineering and aerospace applications.
- Non-Magnetic Properties: Gr11 titanium wire is non-magnetic, making it suitable for use in applications where magnetic interference needs to be minimized, such as in certain medical devices and scientific instruments.
- Excellent Fatigue Resistance: The wire demonstrates superior fatigue resistance, allowing it to withstand repeated stress cycles without failure. This property is crucial in applications involving cyclic loading, such as in aerospace components and medical implants.
These properties make Gr11 titanium wire an versatile material that finds applications in a wide range of industries, from aerospace and medical to chemical processing and marine engineering.
How is Gr11 titanium wire manufactured?
The manufacturing process of Gr11 titanium wire involves several steps to ensure the production of high-quality wire with consistent properties. The process typically includes the following stages:
- Raw Material Preparation: The process begins with the selection of high-purity titanium and alloying elements. Gr11 titanium is an alpha-beta alloy, containing elements such as aluminum, vanadium, and molybdenum in specific proportions.
- Melting and Ingot Formation: The raw materials are melted in a vacuum or inert atmosphere to prevent contamination. The molten metal is then cast into ingots using techniques such as vacuum arc remelting (VAR) or electron beam melting (EBM) to ensure homogeneity and remove impurities.
- Hot Working: The ingots are subjected to hot working processes, such as forging or rolling, to break down the cast structure and improve the material's mechanical properties. This step also helps in achieving the desired shape and size for further processing.
- Cold Working: The material undergoes cold working processes, which may include drawing or rolling, to further refine the microstructure and achieve the desired wire diameter. Cold working also contributes to increasing the strength of the wire.
- Heat Treatment: Heat treatment processes, such as solution treatment and aging, are applied to optimize the mechanical properties of the wire. These processes help in achieving the desired balance of strength, ductility, and other properties.
- Surface Treatment: The wire may undergo surface treatments such as pickling, passivation, or coating to enhance its corrosion resistance and surface finish.
- Quality Control: Throughout the manufacturing process, rigorous quality control measures are implemented to ensure that the wire meets the required specifications. This includes testing for mechanical properties, chemical composition, and dimensional accuracy.
- Packaging and Distribution: The finished Gr11 titanium wire is carefully packaged to prevent damage during transportation and storage. Proper labeling and documentation are provided to ensure traceability and compliance with industry standards.
The manufacturing process of Gr11 titanium wire requires specialized equipment and expertise to maintain consistent quality and meet the stringent requirements of various industries. Advanced techniques such as precision controlled atmospheres, specialized heat treatment processes, and state-of-the-art testing equipment are often employed to produce high-quality Gr11 titanium wire.
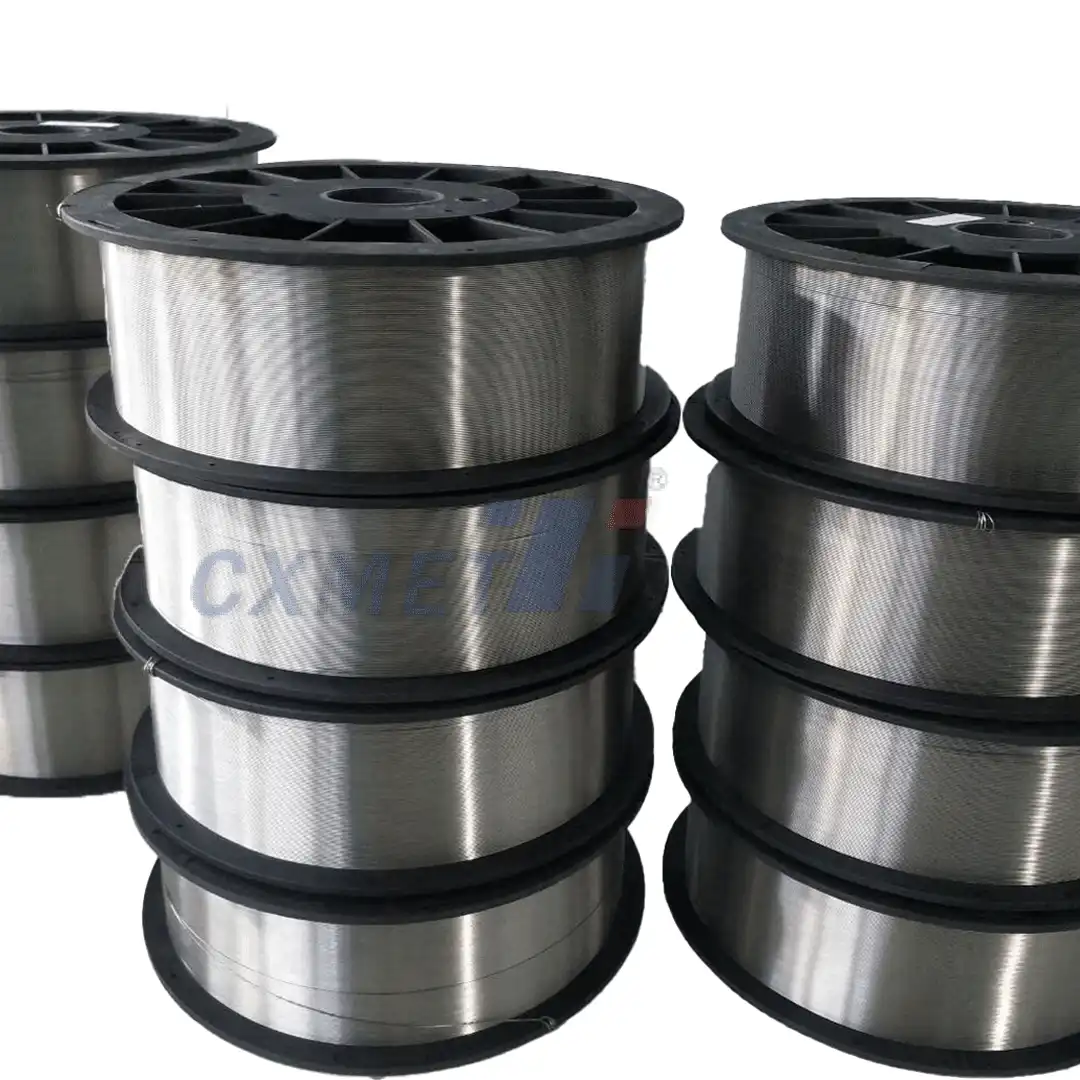
What are the applications of Gr11 titanium wire?
Gr11 titanium wire finds applications in a wide range of industries due to its unique combination of properties. Some of the key applications include:
- Aerospace Industry: In the aerospace sector, Gr11 titanium wire is used in the fabrication of various components, including fasteners, springs, and structural elements. Its high strength-to-weight ratio and excellent fatigue resistance make it ideal for use in aircraft and spacecraft construction.
- Medical and Dental Applications: The biocompatibility and corrosion resistance of Gr11 titanium wire make it an excellent choice for medical implants, surgical instruments, and dental appliances. It is commonly used in orthodontic wires, bone screws, and prosthetic devices.
- Marine Engineering: The wire's exceptional corrosion resistance in saltwater environments makes it suitable for various marine applications, including underwater sensors, offshore structures, and boat fittings.
- Chemical Processing: In the chemical industry, Gr11 titanium wire is used in the construction of heat exchangers, valves, and other components that require high corrosion resistance in aggressive chemical environments.
- Automotive Industry: The automotive sector utilizes Gr11 titanium wire in various applications, including exhaust systems, suspension components, and valve springs, where high strength and low weight are crucial.
- Sports Equipment: The wire is used in the production of high-performance sports equipment, such as golf club shafts, bicycle frames, and tennis racket strings, due to its strength and lightweight properties.
- Jewelry Making: Gr11 titanium wire is increasingly popular in the jewelry industry for creating hypoallergenic and durable pieces.
- Energy Sector: In the oil and gas industry, the wire is used in downhole tools and offshore equipment due to its corrosion resistance and strength in harsh environments.
- Electronics: The wire's non-magnetic properties make it suitable for use in certain electronic components and precision instruments where magnetic interference needs to be minimized.
- Research and Development: Gr11 titanium wire is often used in scientific research and development projects, particularly in fields such as materials science and biomedical engineering.
The versatility of Gr11 titanium wire continues to drive its adoption in new and emerging applications across various industries. As technology advances and new challenges arise, the unique properties of this material make it a valuable resource for innovative solutions in engineering and manufacturing.
At SHAANXI CXMET TECHNOLOGY CO., LTD, we take pride in our extensive product range, which caters to diverse customer needs. Our company is equipped with outstanding production and processing capabilities, ensuring the high quality and precision of our products. We are committed to innovation and continuously strive to develop new products, keeping us at the forefront of our industry. With leading technological development capabilities, we are able to adapt and evolve in a rapidly changing market. Furthermore, we offer customized solutions to meet the specific requirements of our clients. If you are interested in our products or wish to learn more about the intricate details of our offerings, please do not hesitate to contact us at sales@cxmet.com. Our team is always ready to assist you.
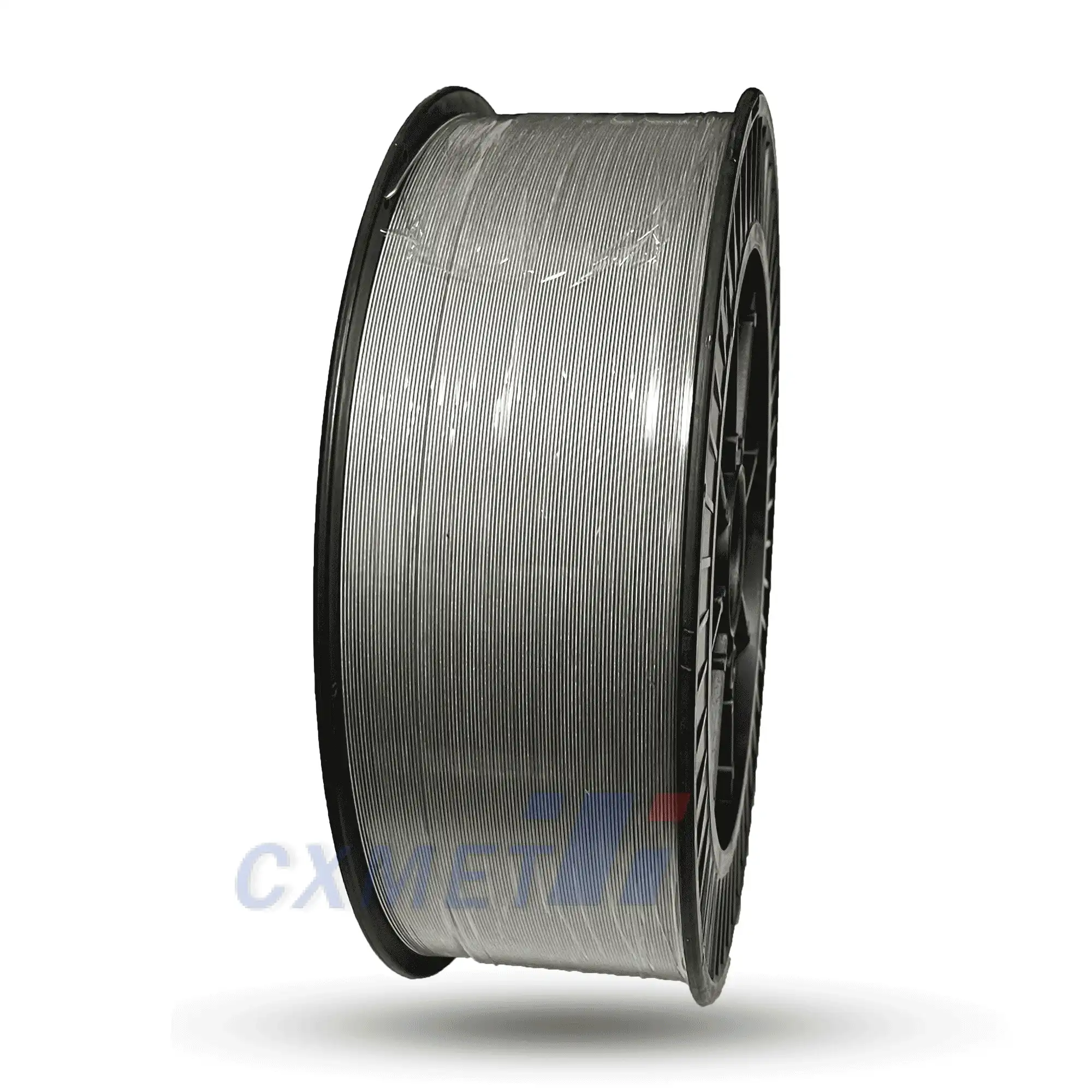
References
- ASM International. (2015). Titanium: A Technical Guide. Materials Park, OH: ASM International.
- Lutjering, G., & Williams, J. C. (2007). Titanium (2nd ed.). Berlin: Springer-Verlag.
- Donachie, M. J. (2000). Titanium: A Technical Guide (2nd ed.). Materials Park, OH: ASM International.
- Peters, M., Kumpfert, J., Ward, C. H., & Leyens, C. (2003). Titanium Alloys for Aerospace Applications. Advanced Engineering Materials, 5(6), 419-427.
- Rack, H. J., & Qazi, J. I. (2006). Titanium alloys for biomedical applications. Materials Science and Engineering: C, 26(8), 1269-1277.
- Boyer, R. R. (1996). An overview on the use of titanium in the aerospace industry. Materials Science and Engineering: A, 213(1-2), 103-114.
- Elias, C. N., Lima, J. H. C., Valiev, R., & Meyers, M. A. (2008). Biomedical applications of titanium and its alloys. JOM, 60(3), 46-49.
- Schutz, R. W., & Watkins, H. B. (1998). Recent developments in titanium alloy application in the energy industry. Materials Science and Engineering: A, 243(1-2), 305-315.
- Niinomi, M. (2008). Mechanical biocompatibilities of titanium alloys for biomedical applications. Journal of the Mechanical Behavior of Biomedical Materials, 1(1), 30-42.
- Froes, F. H. (Ed.). (2015). Titanium: Physical Metallurgy, Processing, and Applications. Materials Park, OH: ASM International.