Grade 6 titanium bar is a high-strength, corrosion-resistant alloy that combines the excellent properties of titanium with small amounts of aluminum and vanadium. This alloy, also known as Ti-5Al-5V-5Mo-1Cr-1Fe, offers an impressive balance of strength, toughness, and fatigue resistance. Grade 6 titanium bar is widely used in aerospace, marine, and industrial applications where superior performance under demanding conditions is required.
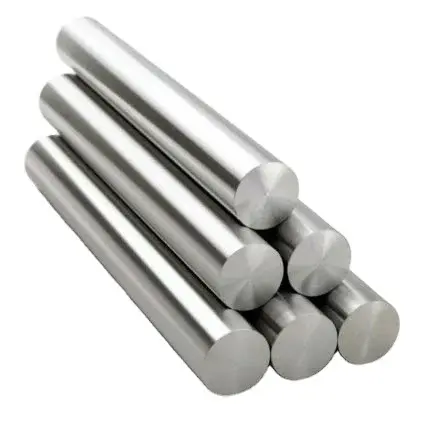
How does Grade 6 Titanium compare to other Titanium grades?
Grade 6 Titanium Bar is an alpha-beta alloy that offers distinct advantages over other titanium grades. When compared to commercially pure titanium (Grade 1-4) and the popular Grade 5 (Ti-6Al-4V), Grade 6 titanium exhibits superior strength and excellent fatigue properties. Here's a detailed comparison:
- Strength: Grade 6 titanium has a typical tensile strength of 1170 MPa (170 ksi), which is significantly higher than Grade 5 (900 MPa or 130 ksi) and more than twice that of Grade 2 (345 MPa or 50 ksi).
- Fatigue resistance: The fatigue strength of Grade 6 titanium is approximately 20-30% higher than Grade 5, making it ideal for applications involving cyclic loading.
- Toughness: While not as ductile as commercially pure titanium, Grade 6 offers better toughness than Grade 5, providing a good balance between strength and impact resistance.
- Corrosion resistance: Like other titanium alloys, Grade 6 exhibits excellent corrosion resistance in various environments, including seawater and chemical processing applications.
- Heat treatment: Grade 6 titanium can be heat treated to achieve even higher strength levels, offering more flexibility in design and manufacturing processes.
The unique composition of Grade 6 titanium, with its balanced mix of alpha and beta stabilizing elements, contributes to its superior mechanical properties. The addition of molybdenum, chromium, and iron provides enhanced hardenability and improved strength-to-weight ratio compared to other titanium grades. This makes Grade 6 titanium bars an excellent choice for critical structural components in aerospace and marine applications where weight savings and high performance are crucial.
What are the main applications of Grade 6 Titanium Bar?
Grade 6 titanium bar finds extensive use in various high-performance applications across multiple industries. Its exceptional combination of strength, corrosion resistance, and fatigue properties make it an ideal material for demanding environments. Some of the main applications include:
- Aerospace industry:
- Aircraft structural components: Grade 6 titanium is used in critical parts such as landing gear, wing attachments, and engine mounts.
- Fasteners and bolts: The high strength-to-weight ratio makes it suitable for aerospace fasteners.
- Engine components: Compressor blades, discs, and other engine parts benefit from Grade 6 titanium's high-temperature performance.
- Marine applications:
- Submarine and ship components: Grade 6 titanium's corrosion resistance in seawater makes it ideal for marine environments.
- Propeller shafts and underwater vehicle parts: The alloy's strength and durability are crucial for these applications.
- Desalination plant components: Its resistance to saltwater corrosion is beneficial in water treatment facilities.
- Industrial uses:
- Chemical processing equipment: Grade 6 titanium's resistance to various chemicals makes it suitable for reactors and storage tanks.
- Oil and gas industry: Downhole tools and offshore platform components benefit from its strength and corrosion resistance.
- High-performance automotive parts: Racing and high-end vehicles use Grade 6 titanium for components requiring exceptional strength and light weight.
- Medical implants:
- Orthopedic implants: While less common than Grade 5, Grade 6 titanium is used in some high-stress implant applications.
- Dental implants: Its biocompatibility and strength make it suitable for certain dental procedures.
The versatility of Grade 6 titanium bar allows engineers and designers to push the boundaries of material performance in these applications. Its ability to maintain strength at elevated temperatures, resist fatigue, and withstand corrosive environments makes it an invaluable material in situations where failure is not an option. As technology advances and new challenges emerge, Grade 6 titanium continues to play a crucial role in enabling innovative solutions across various industries.
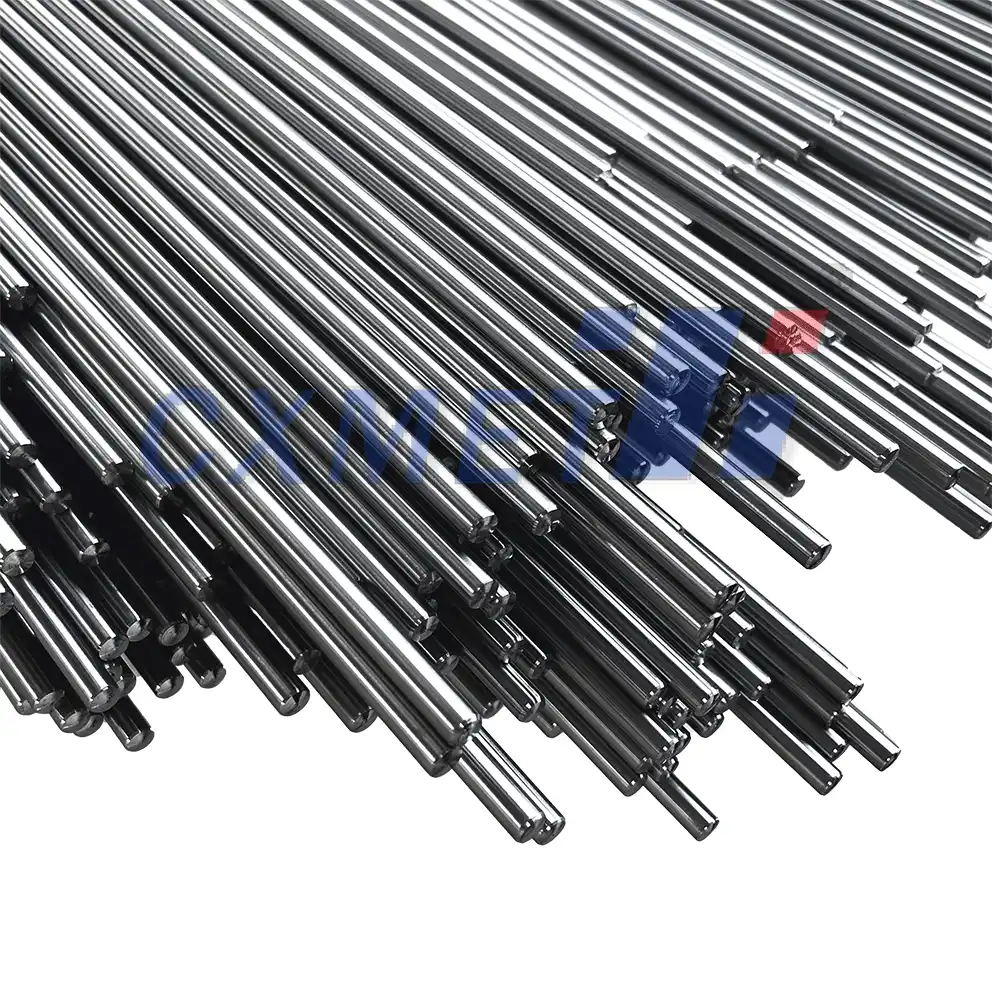
How is Grade 6 Titanium Bar manufactured and processed?
The manufacturing and processing of Grade 6 Titanium Bar involve several complex steps to ensure the material meets the required specifications and properties. The process typically includes the following stages:
- Raw material preparation:
- Titanium sponge production: Pure titanium is extracted from its ore (usually rutile or ilmenite) through the Kroll process.
- Alloying element preparation: High-purity aluminum, vanadium, molybdenum, chromium, and iron are sourced for alloying.
- Melting and ingot formation:
- Vacuum Arc Remelting (VAR): The alloy components are melted together in a vacuum environment to ensure purity and homogeneity.
- Electron Beam Melting (EBM): Sometimes used as an alternative or in combination with VAR for improved cleanliness.
- Ingot casting: The molten alloy is cast into large ingots for further processing.
- Primary processing:
- Forging: The ingots are heated and shaped using hydraulic presses to improve grain structure and mechanical properties.
- Rolling: Hot rolling is used to reduce the cross-section and create long bars or billets.
- Secondary processing:
- Cold working: Further shaping and size reduction may be done at room temperature to achieve tighter tolerances.
- Machining: Turning, milling, and other machining processes are used to create the final bar shape and dimensions.
- Heat treatment:
- Solution treatment: Heating the alloy to a specific temperature and then rapidly cooling to achieve desired microstructure.
- Aging: Controlled heating at lower temperatures to precipitate strengthening phases within the alloy.
- Surface treatment:
- Pickling: Chemical treatment to remove surface oxides and create a clean, passive surface.
- Anodizing: Electrochemical process to enhance surface properties and corrosion resistance.
- Quality control and testing:
- Non-destructive testing: Ultrasonic, X-ray, and other methods to check for internal defects.
- Mechanical testing: Tensile, hardness, and fatigue tests to verify material properties.
- Chemical analysis: To ensure the correct composition and purity of the alloy.
The manufacturing process for Grade 6 titanium bar requires strict control over every stage to maintain the alloy's unique properties. Special attention is paid to temperature control during melting and forging to prevent oxygen contamination, which can significantly affect the material's performance. The multiple melting steps ensure a homogeneous composition and reduce the risk of inclusions or defects that could compromise the bar's integrity.
Advanced processing techniques, such as thermomechanical processing, may be employed to fine-tune the microstructure and enhance specific properties like fatigue resistance or fracture toughness. This involves carefully controlled cycles of deformation and heat treatment to optimize grain size and phase distribution within the alloy.
The final heat treatment process is crucial in developing the desired balance of strength and ductility in Grade 6 titanium bars. Solution treatment dissolves alloying elements into the titanium matrix, while subsequent aging allows controlled precipitation of strengthening phases. The specific heat treatment parameters are often tailored to meet the requirements of particular applications or customer specifications.
Quality control measures are implemented throughout the manufacturing process to ensure consistency and reliability. This includes rigorous testing and inspection protocols, as well as maintaining detailed documentation of processing parameters and material traceability. The stringent quality standards required for aerospace and critical industrial applications drive continuous improvement in manufacturing techniques and process control for Grade 6 titanium bars.
At SHAANXI CXMET TECHNOLOGY CO., LTD, we take pride in our extensive product range, which caters to diverse customer needs. Our company is equipped with outstanding production and processing capabilities, ensuring the high quality and precision of our products. We are committed to innovation and continuously strive to develop new products, keeping us at the forefront of our industry. With leading technological development capabilities, we are able to adapt and evolve in a rapidly changing market. Furthermore, we offer customized solutions to meet the specific requirements of our clients. If you are interested in our products or wish to learn more about the intricate details of our offerings, please do not hesitate to contact us at sales@cxmet.com. Our team is always ready to assist you.
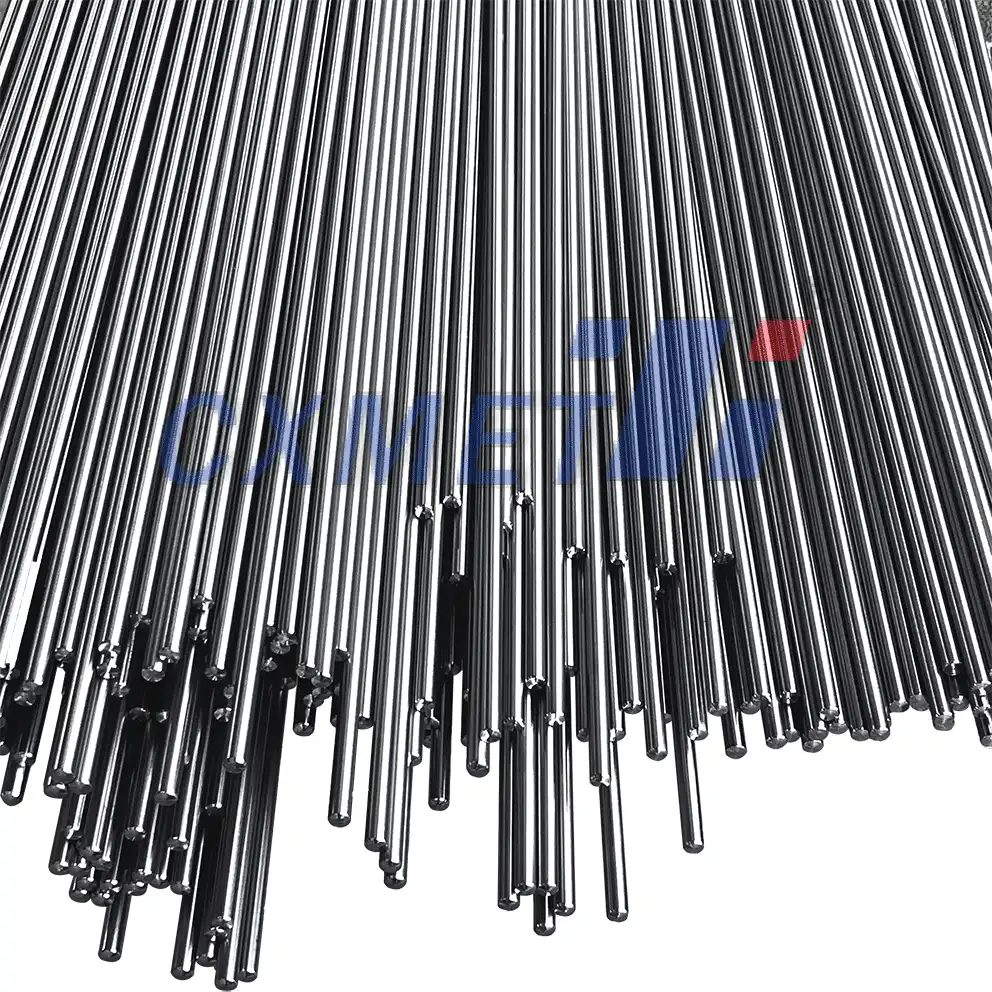
References
- ASM International. (2015). Titanium: Physical Metallurgy, Processing, and Applications.
- Lutjering, G., & Williams, J. C. (2007). Titanium (2nd ed.). Springer-Verlag Berlin Heidelberg.
- Rack, H. J., & Qazi, J. I. (2006). Titanium alloys for biomedical applications. Materials Science and Engineering: C, 26(8), 1269-1277.
- Boyer, R. R. (1996). An overview on the use of titanium in the aerospace industry. Materials Science and Engineering: A, 213(1-2), 103-114.
- Peters, M., Kumpfert, J., Ward, C. H., & Leyens, C. (2003). Titanium alloys for aerospace applications. Advanced Engineering Materials, 5(6), 419-427.
- Donachie, M. J. (2000). Titanium: A Technical Guide (2nd ed.). ASM International.
- Froes, F. H. (2015). Titanium: Physical Metallurgy, Processing, and Applications. ASM International.
- Banerjee, D., & Williams, J. C. (2013). Perspectives on titanium science and technology. Acta Materialia, 61(3), 844-879.
- Leyens, C., & Peters, M. (Eds.). (2003). Titanium and Titanium Alloys: Fundamentals and Applications. John Wiley & Sons.
- ASTM International. (2020). ASTM B348 - Standard Specification for Titanium and Titanium Alloy Bars and Billets.