Titanium 6Al-4V Grade 5 round bar is a high-strength, low-weight alloy widely used in aerospace, medical, and industrial applications. The manufacturing process for this versatile material involves several complex steps, combining advanced metallurgical techniques with precision engineering. This blog post will explore the intricate journey from raw materials to finished Titanium 6Al-4V Grade 5 round bar, highlighting key processes and quality control measures.
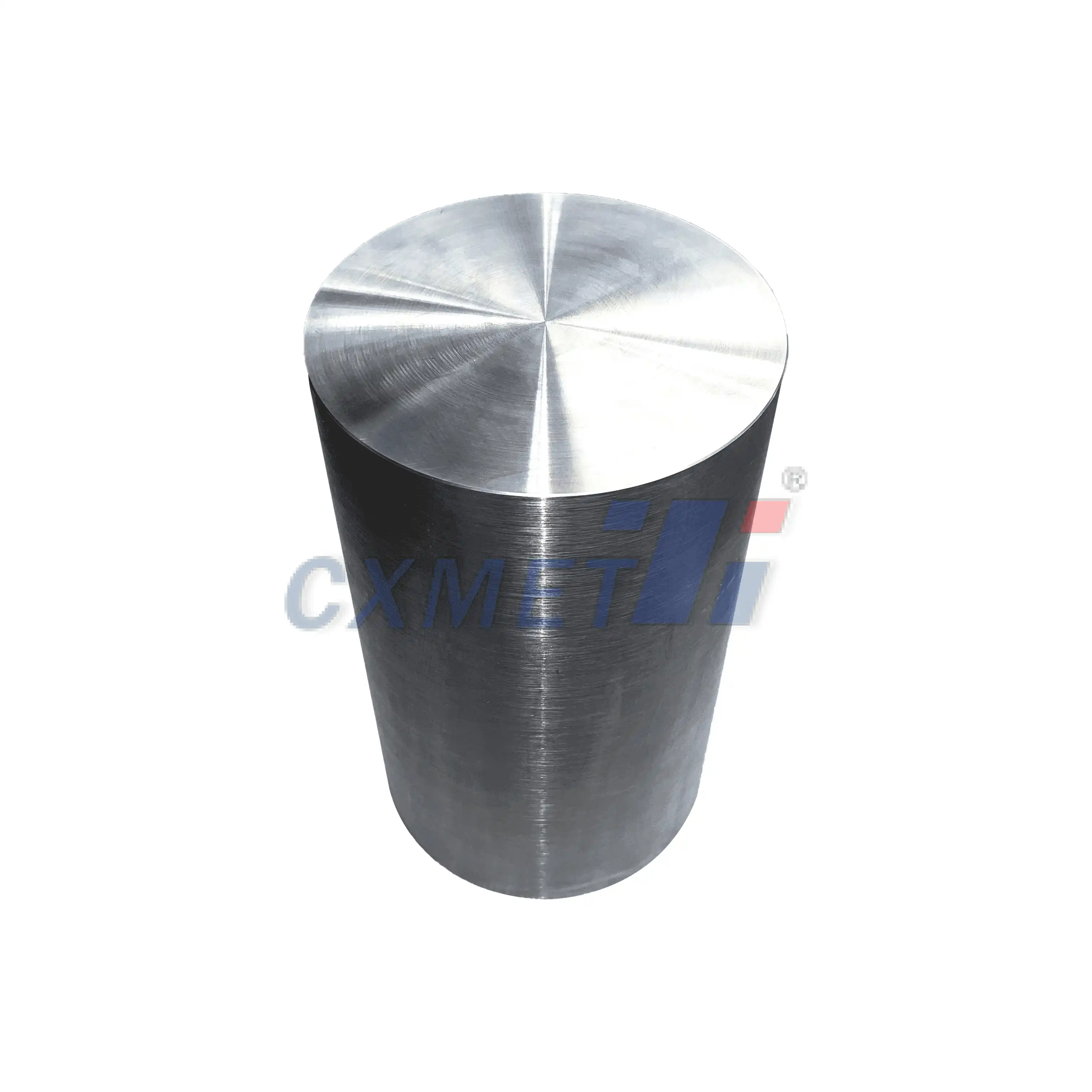
What are the key steps in producing Titanium 6Al-4V Grade 5 alloy?
The production of Titanium 6Al-4V Grade 5 alloy begins with the careful selection and preparation of raw materials. The primary components are titanium, aluminum (6%), and vanadium (4%), along with trace elements that contribute to the alloy's unique properties. The process typically involves the following key steps:
- Raw Material Preparation: High-purity titanium sponge, aluminum, and vanadium are carefully measured and combined. The exact ratios are critical to achieving the desired mechanical properties of the final alloy.
- Melting: The raw materials are melted in a vacuum or inert gas environment using either Vacuum Arc Remelting (VAR) or Electron Beam Melting (EBM) techniques. These methods prevent contamination and ensure the purity of the alloy.
- Ingot Formation: The molten alloy is poured into molds to form large ingots. These ingots can weigh several tons and serve as the starting point for further processing.
- Homogenization: The ingots undergo a homogenization heat treatment to ensure uniform distribution of alloying elements throughout the material. This step is crucial for achieving consistent properties in the final product.
- Primary Processing: The homogenized ingots are then subjected to primary processing techniques such as forging, rolling, or extrusion. These processes break down the ingot's cast structure and begin to shape the material into more manageable forms.
- Secondary Processing: Depending on the desired final form, the material may undergo additional processing steps such as machining, heat treatment, or surface finishing.
Throughout these steps, strict quality control measures are implemented to ensure that the alloy meets the required specifications for Titanium 6Al-4V Grade 5. This includes regular chemical analysis, microstructure examination, and mechanical property testing.
How is Titanium 6Al-4V Grade 5 round bar formed and shaped?
The formation and shaping of Titanium 6Al-4V Grade 5 round bar is a specialized process that builds upon the initial alloy production. The goal is to create a uniform, cylindrical product with precise dimensions and excellent surface finish. The process typically involves the following steps:
- Billet Preparation: The alloy ingot is first cut into smaller, more manageable sections called billets. These billets are typically heated to improve workability.
- Extrusion or Forging: The heated billets are then either extruded through a die or forged using powerful presses. Extrusion involves forcing the material through a shaped opening to create a long, continuous bar. Forging, on the other hand, uses compressive forces to shape the billet into a round bar form.
- Hot Working: The material is often worked at elevated temperatures (typically around 900-950°C) to improve formability and reduce the risk of cracking. This process helps to refine the grain structure and enhance the mechanical properties of the alloy.
- Straightening: After the initial shaping, the bars may be straightened using specialized machinery to ensure they meet roundness and straightness tolerances.
- Heat Treatment: The shaped bars undergo heat treatment processes such as solution treatment and aging. These treatments optimize the microstructure and mechanical properties of the alloy.
- Machining: The heat-treated bars are then machined to achieve the final dimensions and surface finish. This may involve turning, grinding, or other precision machining techniques.
- Surface Treatment: Depending on the application, the round bars may undergo additional surface treatments such as polishing, coating, or anodizing to enhance corrosion resistance or other properties.
Throughout the forming and shaping process, rigorous quality control measures are implemented. These include dimensional checks, non-destructive testing (such as ultrasonic inspection), and mechanical property testing to ensure that the round bars meet the required specifications for Titanium 6Al-4V Grade 5.
The choice between extrusion and forging often depends on the desired final properties and the intended application of the round bar. Extrusion typically produces a more uniform microstructure and is well-suited for longer, smaller diameter bars. Forging, on the other hand, can produce bars with enhanced mechanical properties and is often preferred for larger diameter bars or those requiring superior strength in specific directions.
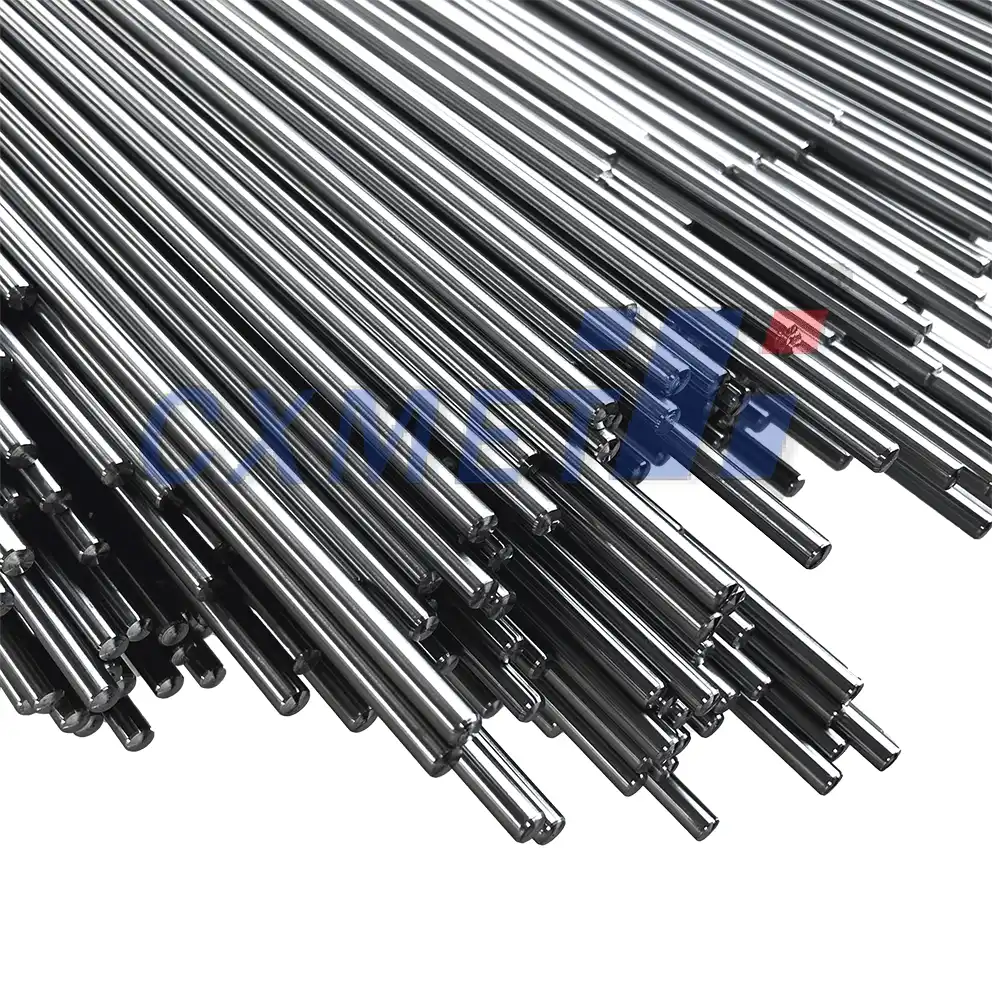
What quality control measures are used in Titanium 6Al-4V Grade 5 round bar production?
Quality control is a critical aspect of Titanium 6Al-4V Grade 5 round bar production, ensuring that the final product meets the stringent requirements for aerospace, medical, and industrial applications. The quality control process is comprehensive, covering every stage of production from raw material selection to final inspection. Key quality control measures include:
- Raw Material Verification: Before production begins, all raw materials are thoroughly analyzed to ensure they meet purity and composition requirements. This includes spectrographic analysis and other advanced testing methods.
- Process Monitoring: Throughout the manufacturing process, key parameters such as temperature, pressure, and processing times are continuously monitored and recorded. This ensures consistency and allows for traceability in case of any issues.
- Chemical Composition Analysis: Regular samples are taken during production for chemical analysis. This ensures that the alloy composition remains within the specified ranges for Titanium 6Al-4V Grade 5.
- Microstructure Examination: Metallographic analysis is performed to examine the microstructure of the alloy. This helps verify that the proper phases are present and that the grain structure meets requirements.
- Mechanical Property Testing: Samples from each production lot undergo mechanical testing, including tensile strength, yield strength, elongation, and hardness tests. These results must meet or exceed the minimum requirements for Titanium 6Al-4V Grade 5.
- Non-Destructive Testing (NDT): Various NDT methods are employed to detect any internal or surface defects in the round bars. These may include:
- Ultrasonic Testing: To detect internal flaws or inconsistencies
- Eddy Current Testing: For surface and near-surface defect detection
- Liquid Penetrant Inspection: To identify surface-breaking defects
- Dimensional Inspection: Precise measurements are taken to ensure that the round bars meet specified dimensional tolerances, including diameter, length, straightness, and roundness.
- Surface Quality Inspection: The surface of the round bars is carefully examined for any imperfections, such as scratches, pits, or other defects that could affect performance.
- Heat Treatment Verification: For heat-treated bars, the heat treatment process is closely monitored, and post-treatment testing is performed to verify that the desired mechanical properties have been achieved.
- Documentation and Traceability: Detailed records are maintained throughout the production process, allowing for complete traceability of each batch of round bars back to the original raw materials and processing parameters.
In addition to these specific measures, many manufacturers of Titanium 6Al-4V Grade 5 round bars adhere to international quality management standards such as ISO 9001 and AS9100 for aerospace applications. These standards ensure that comprehensive quality management systems are in place, covering all aspects of production, testing, and documentation.
It's worth noting that the exact quality control procedures may vary somewhat between manufacturers, and some may employ additional proprietary testing methods. However, the goal remains the same: to produce Titanium 6Al-4V Grade 5 round bars that consistently meet or exceed industry standards and customer specifications.
The rigorous quality control process is essential given the critical nature of many applications for Titanium 6Al-4V Grade 5 round bars. In aerospace, for example, these materials may be used in structural components where failure could have catastrophic consequences. In medical applications, such as implants, the purity and consistency of the material are crucial for patient safety and long-term performance.
At SHAANXI CXMET TECHNOLOGY CO., LTD, we take pride in our extensive product range, which caters to diverse customer needs. Our company is equipped with outstanding production and processing capabilities, ensuring the high quality and precision of our products. We are committed to innovation and continuously strive to develop new products, keeping us at the forefront of our industry. With leading technological development capabilities, we are able to adapt and evolve in a rapidly changing market. Furthermore, we offer customized solutions to meet the specific requirements of our clients. If you are interested in our products or wish to learn more about the intricate details of our offerings, please do not hesitate to contact us at sales@cxmet.com. Our team is always ready to assist you.
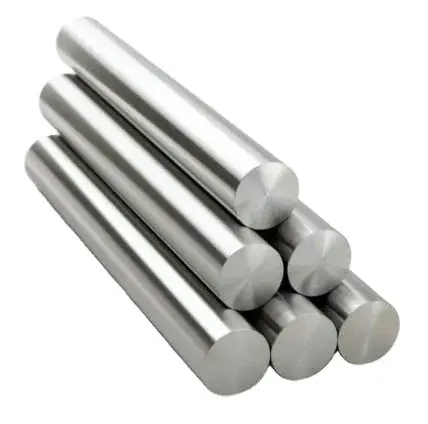
References
- ASM International. (2015). Titanium: A Technical Guide, 2nd Edition.
- Leyens, C., & Peters, M. (Eds.). (2003). Titanium and Titanium Alloys: Fundamentals and Applications.
- Boyer, R., Welsch, G., & Collings, E. W. (Eds.). (1994). Materials Properties Handbook: Titanium Alloys.
- ASTM International. (2020). ASTM B348 - Standard Specification for Titanium and Titanium Alloy Bars and Billets.
- Donachie, M. J. (2000). Titanium: A Technical Guide, 2nd Edition.
- Lütjering, G., & Williams, J. C. (2007). Titanium (Engineering Materials and Processes).
- Peters, M., Kumpfert, J., Ward, C. H., & Leyens, C. (2003). Titanium Alloys for Aerospace Applications. Advanced Engineering Materials, 5(6), 419-427.
- Veiga, C., Davim, J. P., & Loureiro, A. J. R. (2012). Properties and applications of titanium alloys: A brief review. Reviews on Advanced Materials Science, 32(2), 133-148.
- Rack, H. J., & Qazi, J. I. (2006). Titanium alloys for biomedical applications. Materials Science and Engineering: C, 26(8), 1269-1277.
- Inagaki, I., Takechi, T., Shirai, Y., & Ariyasu, N. (2014). Application and Features of Titanium for the Aerospace Industry. Nippon Steel & Sumitomo Metal Technical Report, 106, 22-27.