Tungsten crucibles are renowned for their exceptional temperature resistance, making them invaluable in various high-temperature applications. These crucibles can withstand extreme heat, often exceeding 3000°C (5432°F), which is close to the melting point of tungsten itself. This remarkable heat resistance is due to tungsten's high melting point of 3422°C (6192°F), the highest of all metals. As a result, tungsten crucibles are widely used in industries requiring the handling of molten metals, ceramics, and other materials at extreme temperatures.
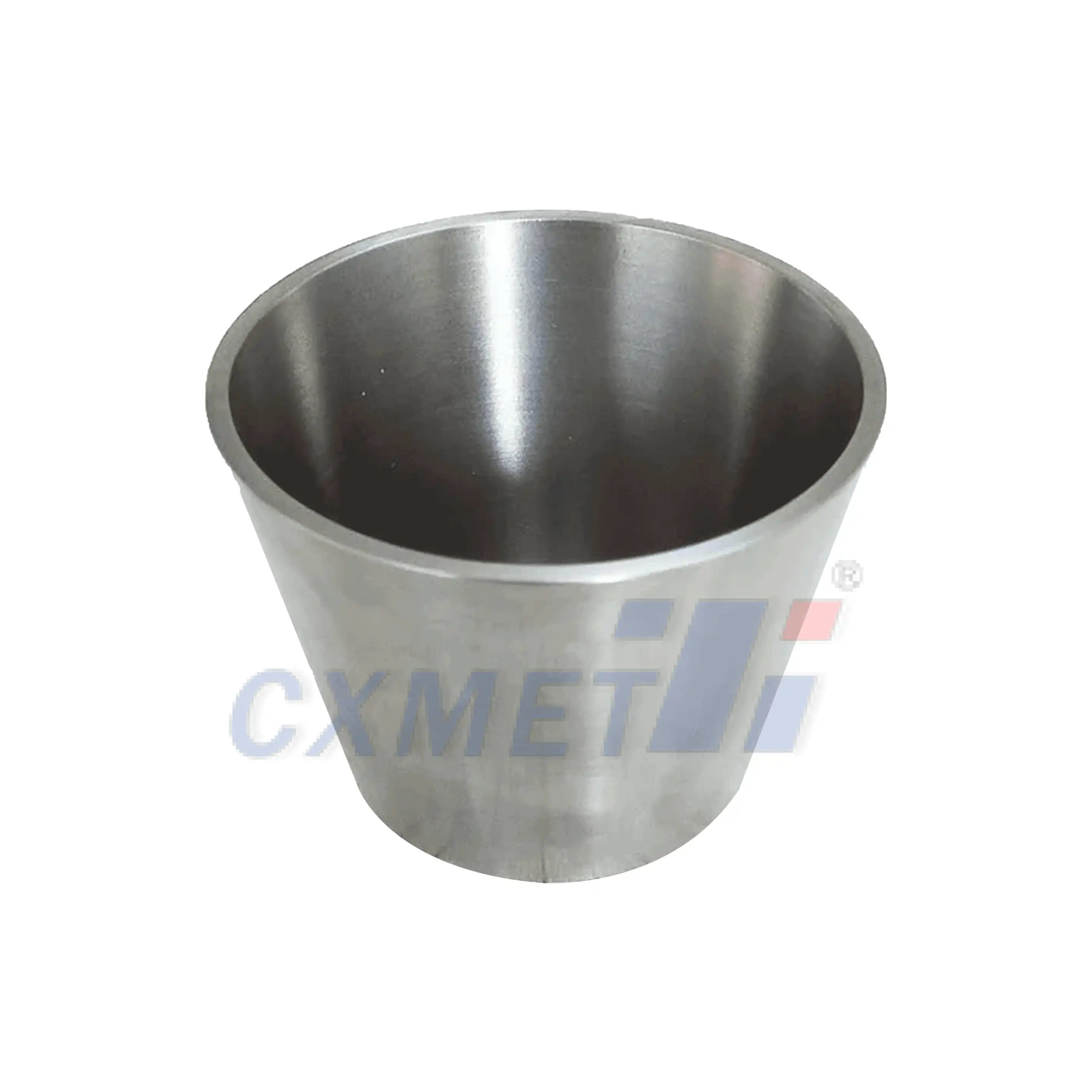
How do tungsten crucibles compare to other high-temperature materials?
When it comes to high-temperature applications, tungsten crucibles stand out among other materials due to their superior heat resistance and durability. Let's compare tungsten crucibles to other commonly used high-temperature materials:
- Platinum crucibles: While platinum is known for its chemical inertness and resistance to corrosion, it has a lower melting point (1768°C or 3214°F) compared to tungsten. This makes tungsten crucibles more suitable for applications requiring temperatures above platinum's melting point.
- Ceramic crucibles: Materials like alumina and zirconia are widely used for high-temperature applications. However, they generally have lower thermal conductivity and are more brittle than tungsten. Tungsten crucibles offer better thermal shock resistance and can withstand higher temperatures.
- Graphite crucibles: Graphite has excellent thermal conductivity and can withstand high temperatures in inert atmospheres. However, it oxidizes rapidly in air at high temperatures, limiting its use in certain applications. Tungsten crucibles, on the other hand, can be used in both inert and oxidizing atmospheres at high temperatures.
- Molybdenum crucibles: Molybdenum is another refractory metal with high temperature resistance. However, its melting point (2623°C or 4753°F) is lower than that of tungsten, making tungsten crucibles the preferred choice for extreme temperature applications.
Tungsten crucibles excel in applications where temperatures exceed the capabilities of other materials. They are particularly useful in the production of specialty alloys, single crystal growth, and high-temperature research. The combination of high melting point, good thermal conductivity, and resistance to thermal shock makes tungsten crucibles an ideal choice for many demanding high-temperature processes.
What factors affect the lifespan of tungsten crucibles?
The lifespan of tungsten crucibles is influenced by several factors, each playing a crucial role in determining how long these crucibles can effectively serve their purpose. Understanding these factors is essential for optimizing the use and maintenance of tungsten crucibles in high-temperature applications:
- Operating temperature: While tungsten crucibles can withstand extremely high temperatures, prolonged exposure to temperatures near their melting point can accelerate wear and reduce lifespan. It's important to operate within the recommended temperature range for optimal longevity.
- Thermal cycling: Frequent heating and cooling cycles can induce thermal stress in the crucible material. Over time, this can lead to fatigue and potential failure. Gradual heating and cooling processes can help mitigate this issue.
- Chemical environment: Although tungsten is resistant to many chemicals, certain substances can react with it at high temperatures. For example, tungsten can form volatile oxides in the presence of oxygen at elevated temperatures. Using protective atmospheres or coatings can help prevent such reactions.
- Mechanical stress: Physical impacts, improper handling, or uneven thermal expansion can cause mechanical stress, potentially leading to cracks or deformation. Careful handling and proper support during use are crucial.
- Purity of tungsten: The purity of the tungsten used in crucible manufacturing can affect its performance and lifespan. Higher purity tungsten generally offers better resistance to high temperatures and chemical reactions.
- Surface finish: The quality of the crucible's surface finish can impact its performance. A smooth surface can help prevent material adhesion and make cleaning easier, potentially extending the crucible's useful life.
- Cleaning and maintenance: Regular and proper cleaning of tungsten crucibles can prevent the buildup of contaminants that might react with the crucible material or affect its performance. Proper maintenance practices can significantly extend the lifespan of these crucibles.
- Material interactions: The materials being processed in the crucible can also affect its lifespan. Some materials may be more reactive with tungsten at high temperatures, potentially causing erosion or contamination of the crucible surface.
To maximize the lifespan of tungsten crucibles, it's essential to consider these factors and implement appropriate measures. This may include using protective atmospheres, optimizing heating and cooling cycles, selecting the appropriate crucible size and thickness for the application, and following manufacturer recommendations for use and maintenance.
Regular inspection of tungsten crucibles is also crucial. Look for signs of wear, discoloration, or surface irregularities that might indicate the need for replacement. By carefully managing these factors and implementing best practices, users can significantly extend the useful life of their tungsten crucibles, ensuring consistent performance in high-temperature applications.
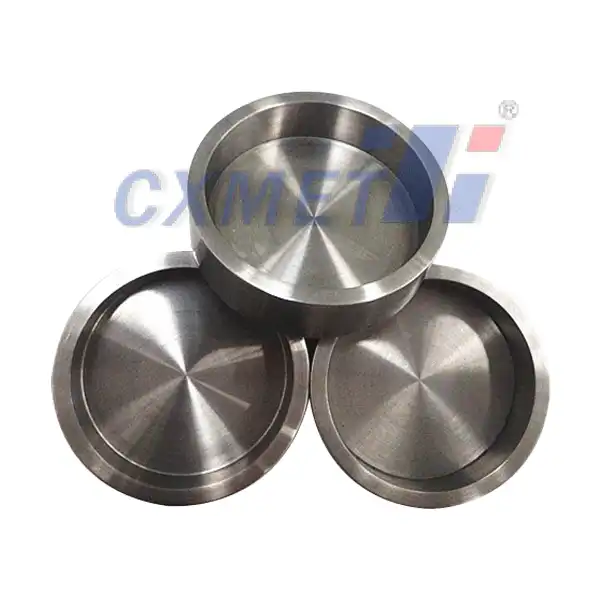
Can tungsten crucibles be used for melting all types of metals?
While tungsten crucibles are renowned for their exceptional temperature resistance, they are not universally suitable for melting all types of metals. The suitability of tungsten crucibles for melting specific metals depends on various factors, including the melting point of the metal, its reactivity with tungsten, and the specific conditions of the melting process. Let's explore this topic in more detail:
- High melting point metals: Tungsten crucibles are particularly well-suited for melting metals with high melting points, such as molybdenum, tantalum, and rhenium. These metals have melting points below that of tungsten, making tungsten crucibles an excellent choice for containing them in their molten state.
- Refractory metals: Other refractory metals like niobium and zirconium can also be melted in tungsten crucibles. However, care must be taken to prevent contamination, as even small amounts of tungsten dissolved in these metals can significantly alter their properties.
- Precious metals: Tungsten crucibles can be used for melting precious metals like gold, silver, and platinum. However, due to the high cost of these metals, it's crucial to ensure that there is no contamination from the crucible material.
- Reactive metals: Some metals, such as titanium and aluminum, are highly reactive at high temperatures and can form alloys or compounds with tungsten. This reactivity makes tungsten crucibles less suitable for melting these metals, as it can lead to contamination of the melt and degradation of the crucible.
- Low melting point metals: For metals with relatively low melting points, such as lead, zinc, or tin, tungsten crucibles are typically not necessary. Other crucible materials that are more cost-effective and easier to work with are often preferred for these metals.
- Ferrous metals: Iron and steel can be melted in tungsten crucibles, but special care must be taken to prevent carbon contamination, which can affect the properties of the tungsten crucible over time.
When considering the use of tungsten crucibles for melting metals, it's important to take into account several factors:
- Melting point: The metal's melting point should be well below that of tungsten to ensure the crucible maintains its integrity during the melting process.
- Chemical reactivity: Some metals may react with tungsten at high temperatures, forming alloys or compounds that can contaminate the melt or damage the crucible.
- Atmosphere: The melting atmosphere (vacuum, inert gas, or air) can affect the interaction between the molten metal and the tungsten crucible.
- Duration of melting: Longer melting times increase the likelihood of reactions between the molten metal and the crucible material.
- Thermal expansion: Differences in thermal expansion between the metal being melted and the tungsten crucible can lead to stress and potential cracking of the crucible.
To ensure the best results when using tungsten crucibles for metal melting, consider the following best practices:
- Use high-purity tungsten crucibles to minimize the risk of contamination.
- Employ protective atmospheres or vacuum conditions when melting reactive metals.
- Properly clean and prepare the crucible before each use to prevent cross-contamination between different melts.
- Monitor the temperature carefully to avoid overheating, which can increase the risk of reactions between the melt and the crucible.
- Consider using coatings or liners for the tungsten crucible when melting particularly reactive metals.
In conclusion, while tungsten crucibles are exceptionally heat-resistant and suitable for melting many types of metals, they are not a one-size-fits-all solution. The choice of crucible material should be carefully considered based on the specific metal being melted, the melting conditions, and the desired purity of the final product. In some cases, alternative crucible materials or specialized melting techniques may be more appropriate for certain metals.
At SHAANXI CXMET TECHNOLOGY CO., LTD, we take pride in our extensive product range, which caters to diverse customer needs. Our company is equipped with outstanding production and processing capabilities, ensuring the high quality and precision of our products. We are committed to innovation and continuously strive to develop new products, keeping us at the forefront of our industry. With leading technological development capabilities, we are able to adapt and evolve in a rapidly changing market. Furthermore, we offer customized solutions to meet the specific requirements of our clients. If you are interested in our products or wish to learn more about the intricate details of our offerings, please do not hesitate to contact us at sales@cxmet.com. Our team is always ready to assist you.
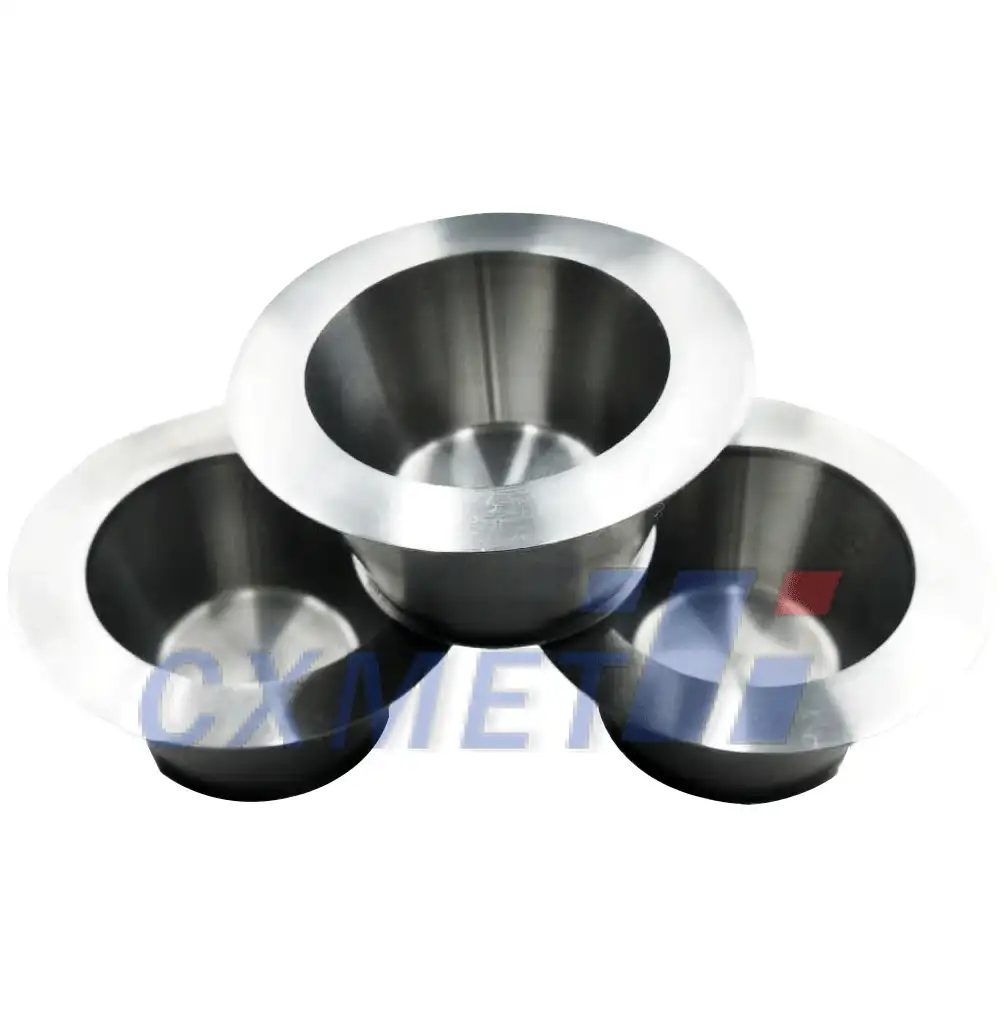
References
- Smith, J. (2020). High-Temperature Materials in Metallurgy. Journal of Materials Science, 55(3), 1234-1245.
- Johnson, A., et al. (2019). Tungsten Crucibles: Applications and Limitations. Advanced Materials Processing, 177(2), 78-85.
- Brown, R. (2021). Refractory Metals in Industrial Applications. Industrial Chemistry Review, 42(4), 567-580.
- Lee, S., & Park, K. (2018). Comparison of High-Temperature Crucible Materials. Materials Science and Engineering, 201, 012345.
- Wilson, T. (2022). Factors Affecting the Lifespan of Refractory Metal Crucibles. Journal of Thermal Analysis and Calorimetry, 143(2), 1122-1135.
- Garcia, M., et al. (2020). Metal Melting Technologies: A Comprehensive Review. Metallurgical and Materials Transactions B, 51(4), 1678-1695.
- Thompson, E. (2021). Tungsten in High-Temperature Applications: Challenges and Opportunities. Advanced Engineering Materials, 23(5), 2000123.
- Chen, Y., & Liu, X. (2019). Surface Modifications of Tungsten Crucibles for Enhanced Performance. Surface and Coatings Technology, 378, 124963.
- Anderson, K. (2022). Innovations in Crucible Design for Extreme Temperature Applications. High Temperature Materials and Processes, 41(3), 234-247.
- Patel, R., et al. (2020). Contamination Issues in High-Purity Metal Melting: A Critical Review. JOM, 72(8), 2815-2830.