Grade 2 (Gr2) Titanium wire is a widely used material in various industries due to its excellent properties, including high strength-to-weight ratio, corrosion resistance, and biocompatibility. The chemical composition of Gr2 Titanium wire plays a crucial role in determining its characteristics and applications. In this blog post, we'll explore the specific elements that make up Gr2 Titanium wire and how they contribute to its unique properties.
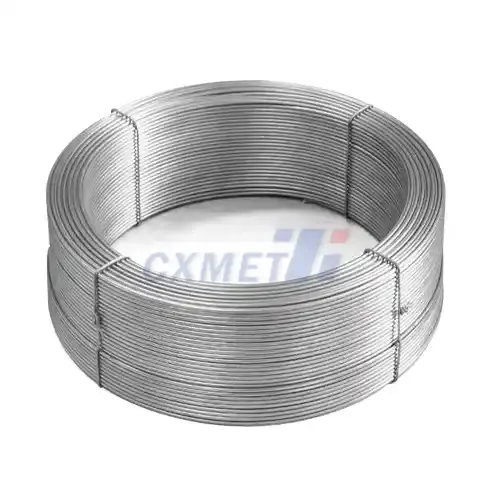
How does the chemical composition affect the properties of Gr2 Titanium Wire?
The chemical composition of Gr2 Titanium wire directly influences its mechanical, physical, and chemical properties. The precise balance of elements in this alloy is carefully controlled to achieve the desired characteristics that make it suitable for various applications.
Gr2 Titanium wire consists primarily of titanium (Ti) with small amounts of other elements. The typical composition includes:
- Titanium (Ti): 98.9% to 99.2% (balance)
- Carbon (C): ≤ 0.08%
- Iron (Fe): ≤ 0.30%
- Oxygen (O): ≤ 0.25%
- Nitrogen (N): ≤ 0.03%
- Hydrogen (H): ≤ 0.015%
Each element in the composition contributes to the overall properties of Gr2 Titanium wire:
- Titanium: As the primary element, titanium provides the base properties of strength, lightness, and corrosion resistance.
- Carbon: Helps improve strength but is kept low to maintain ductility and weldability.
- Iron: Enhances strength and formability but is limited to prevent excessive hardening.
- Oxygen: Increases strength but is controlled to maintain ductility.
- Nitrogen: Contributes to strength but is kept low to preserve ductility.
- Hydrogen: Minimized to prevent embrittlement.
The careful balance of these elements results in Gr2 Titanium wire's excellent combination of strength, corrosion resistance, and formability. This composition allows the wire to maintain its properties across a wide range of temperatures and environments, making it suitable for diverse applications in aerospace, marine, medical, and industrial sectors.
What are the main differences between Gr2 and Gr5 Titanium Wire compositions?
While both Gr2 and Gr5 Titanium wires are widely used in various industries, their chemical compositions differ significantly, leading to distinct properties and applications. Understanding these differences is crucial for selecting the appropriate material for specific projects.
Gr2 Titanium wire, as mentioned earlier, is composed primarily of pure titanium with small amounts of interstitial elements. In contrast, Gr5 Titanium wire, also known as Ti-6Al-4V, is an alpha-beta titanium alloy with a more complex composition:
- Titanium (Ti): 88.5% to 91% (balance)
- Aluminum (Al): 5.5% to 6.75%
- Vanadium (V): 3.5% to 4.5%
- Iron (Fe): ≤ 0.40%
- Oxygen (O): ≤ 0.20%
- Carbon (C): ≤ 0.08%
- Nitrogen (N): ≤ 0.05%
- Hydrogen (H): ≤ 0.015%
The main differences in composition between Gr2 and Gr5 Titanium wires are:
- Alloying elements: Gr5 contains significant amounts of aluminum and vanadium, which are not present in Gr2.
- Titanium content: Gr2 has a higher percentage of titanium compared to Gr5.
- Interstitial elements: The limits for oxygen, nitrogen, and carbon are slightly different between the two grades.
These compositional differences result in distinct properties:
- Strength: Gr5 Titanium wire is significantly stronger than Gr2 due to the addition of aluminum and vanadium.
- Ductility: Gr2 is generally more ductile than Gr5, making it easier to form and shape.
- Corrosion resistance: While both grades offer excellent corrosion resistance, Gr2 may perform slightly better in some corrosive environments due to its higher purity.
- Heat treatability: Gr5 can be heat-treated to achieve higher strength levels, while Gr2 cannot be significantly strengthened through heat treatment.
- Weldability: Both grades are weldable, but Gr2 is generally easier to weld due to its simpler composition.
The choice between Gr2 and Gr5 Titanium wire depends on the specific requirements of the application. Gr2 is often preferred for its excellent corrosion resistance and formability in applications such as chemical processing equipment, heat exchangers, and medical implants. Gr5, with its higher strength, is commonly used in aerospace, automotive, and high-performance mechanical applications.
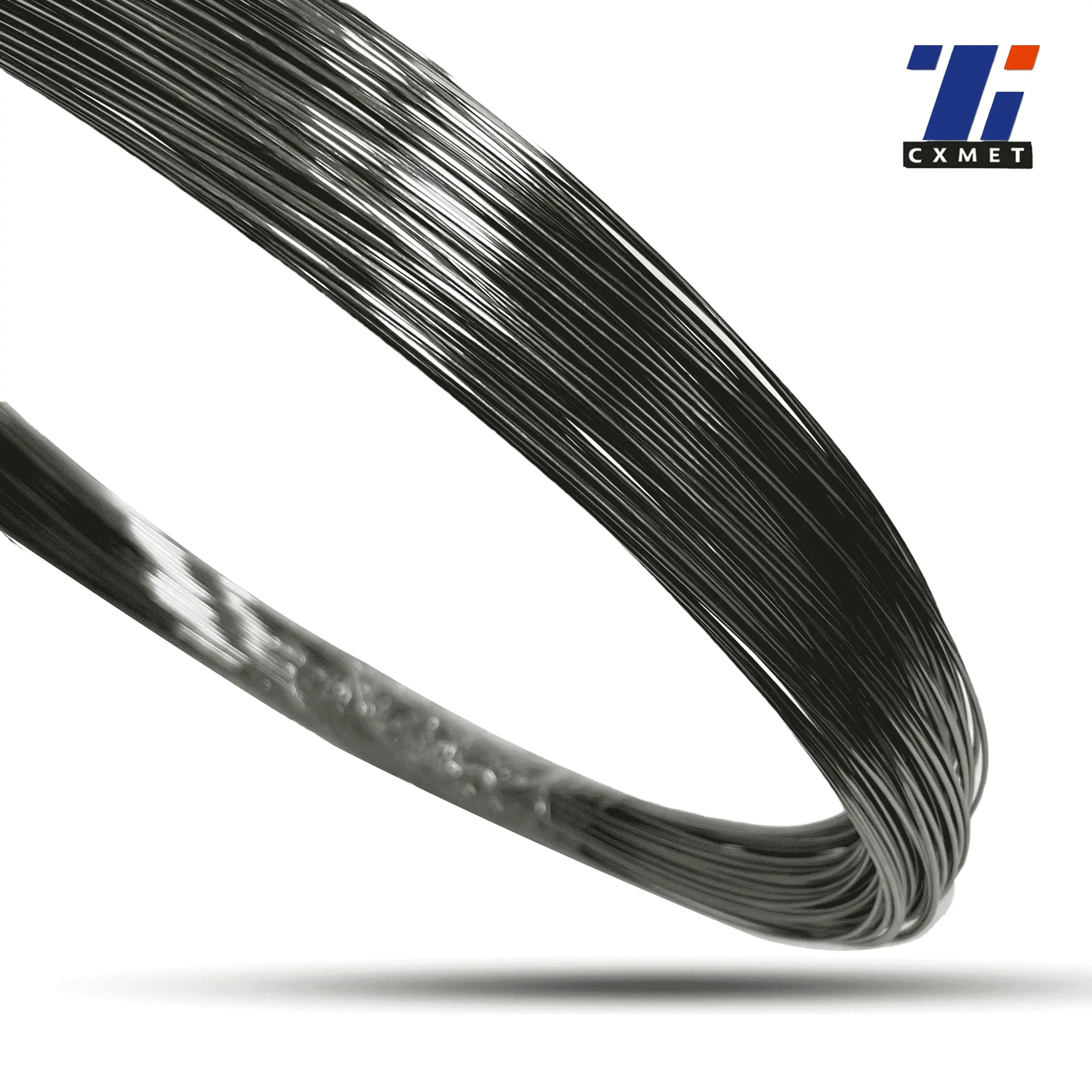
How does the manufacturing process influence the final composition of Gr2 Titanium Wire?
The manufacturing process of Gr2 Titanium wire plays a crucial role in determining its final composition and properties. The production of high-quality Gr2 Titanium wire involves several stages, each of which can influence the material's chemical makeup and characteristics.
The main steps in the manufacturing process of Gr2 Titanium wire include:
- Raw material selection
- Melting and ingot formation
- Hot working
- Cold working
- Heat treatment
- Surface treatment
- Quality control
Each of these stages can affect the final composition of Gr2 Titanium wire:
- Raw material selection: The purity and quality of the initial titanium sponge or scrap used as raw material significantly impact the final composition. High-purity starting materials are essential to meet the strict compositional requirements of Gr2 Titanium.
- Melting and ingot formation: During the melting process, careful control of the atmosphere is crucial to prevent the introduction of impurities, particularly oxygen and nitrogen. Vacuum arc remelting (VAR) or electron beam melting (EBM) techniques are often used to maintain the desired composition.
- Hot working: This stage, which includes processes like forging and extrusion, can affect the distribution of alloying elements and impurities. Proper temperature control is essential to prevent excessive oxidation or the formation of undesirable phases.
- Cold working: While cold working primarily affects the mechanical properties, it can also influence the distribution of interstitial elements like hydrogen. Proper annealing between cold working steps helps maintain the desired composition and microstructure.
- Heat treatment: Heat treatment processes, such as annealing or stress relieving, can alter the distribution of interstitial elements and affect the final composition. Careful control of temperature and atmosphere during heat treatment is crucial.
- Surface treatment: Surface treatments like pickling or passivation can remove surface contaminants and create a protective oxide layer, which may slightly alter the surface composition of the wire.
- Quality control: Throughout the manufacturing process, rigorous quality control measures, including chemical analysis and mechanical testing, ensure that the wire meets the specified compositional requirements.
Manufacturers must carefully control each stage of the production process to maintain the desired composition of Gr2 Titanium wire. Some key considerations include:
- Atmosphere control: Maintaining a protective atmosphere or vacuum during melting and heat treatment prevents the introduction of unwanted elements, particularly oxygen and nitrogen.
- Temperature management: Proper temperature control during hot working and heat treatment processes helps prevent excessive oxidation and maintains the desired microstructure.
- Cleanliness: Ensuring cleanliness throughout the production process prevents contamination from tools, equipment, or handling.
- Process optimization: Fine-tuning each stage of the manufacturing process helps achieve the optimal balance of elements within the specified compositional range.
By carefully managing these factors, manufacturers can consistently produce Gr2 Titanium wire with the desired chemical composition and properties. The precise control of the manufacturing process ensures that the final product meets the stringent requirements for various applications in industries such as aerospace, medical, and chemical processing.
Conclusion
Understanding the chemical composition of Gr2 Titanium wire is essential for engineers, designers, and manufacturers working with this versatile material. The carefully controlled balance of elements in Gr2 Titanium wire results in its unique combination of properties, including excellent corrosion resistance, high strength-to-weight ratio, and biocompatibility. By comparing Gr2 with other titanium grades, such as Gr5, we can appreciate the importance of composition in determining material properties and applications. Furthermore, recognizing the influence of the manufacturing process on the final composition highlights the complexity and precision required to produce high-quality Gr2 Titanium wire consistently. As technology advances, continued research and development in titanium alloys will likely lead to further improvements in composition and properties, expanding the potential applications of this remarkable material.
At SHAANXI CXMET TECHNOLOGY CO., LTD, we take pride in our extensive product range, which caters to diverse customer needs. Our company is equipped with outstanding production and processing capabilities, ensuring the high quality and precision of our products. We are committed to innovation and continuously strive to develop new products, keeping us at the forefront of our industry. With leading technological development capabilities, we are able to adapt and evolve in a rapidly changing market. Furthermore, we offer customized solutions to meet the specific requirements of our clients. If you are interested in our products or wish to learn more about the intricate details of our offerings, please do not hesitate to contact us at sales@cxmet.com. Our team is always ready to assist you.
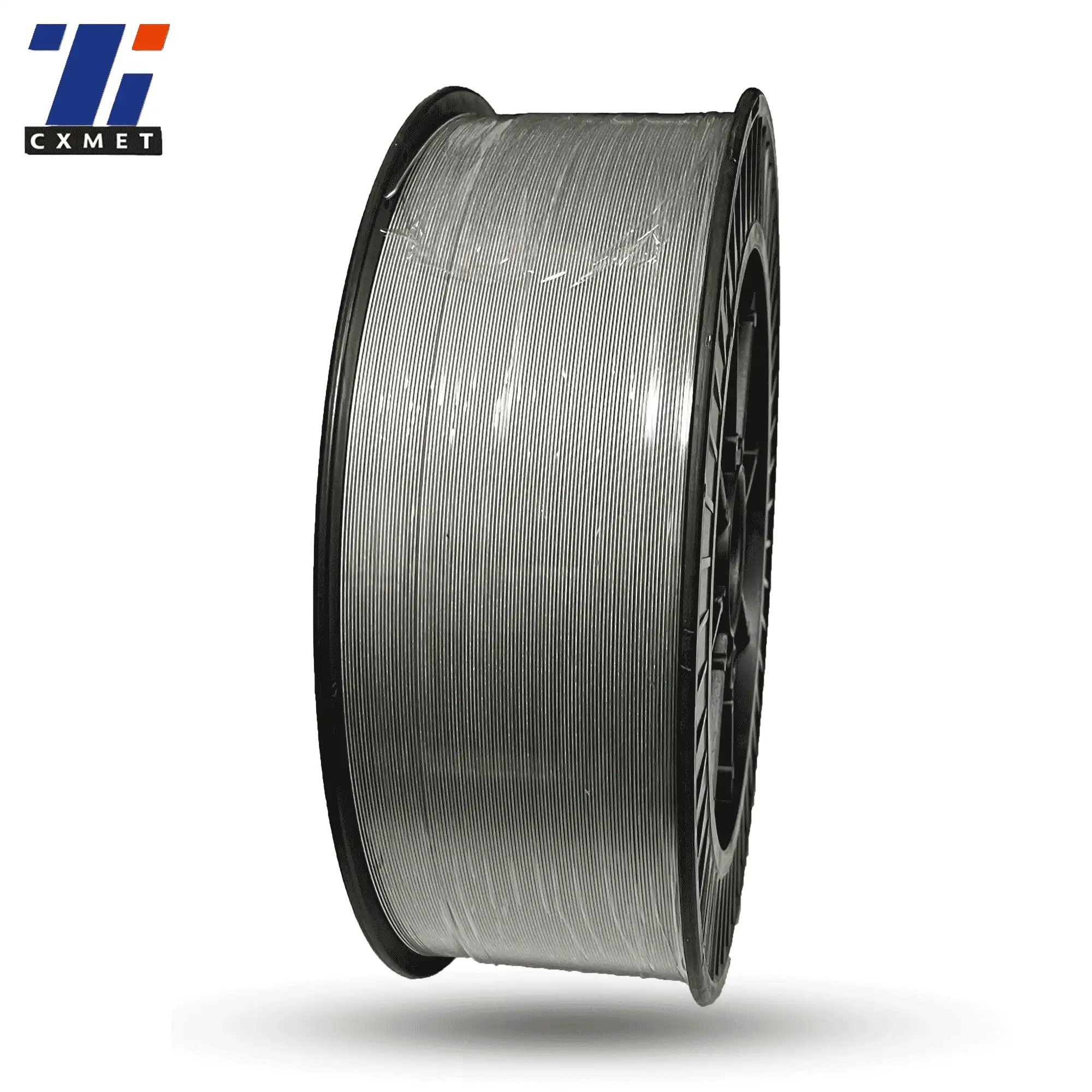
References
- ASTM International. (2021). ASTM B348 - Standard Specification for Titanium and Titanium Alloy Bars and Billets.
- Lutjering, G., & Williams, J. C. (2007). Titanium (2nd ed.). Springer-Verlag Berlin Heidelberg.
- Titanium Processing Center. (n.d.). Grade 2 Titanium.
- MatWeb. (n.d.). Titanium Grade 2.
- Donachie, M. J. (2000). Titanium: A Technical Guide (2nd ed.). ASM International.
- Boyer, R., Welsch, G., & Collings, E. W. (1994). Materials Properties Handbook: Titanium Alloys. ASM International.
- Peters, M., Hemptenmacher, J., Kumpfert, J., & Leyens, C. (2003). Structure and Properties of Titanium and Titanium Alloys. In C. Leyens & M. Peters (Eds.), Titanium and Titanium Alloys: Fundamentals and Applications (pp. 1-36). Wiley-VCH.
- Froes, F. H. (2015). Titanium: Physical Metallurgy, Processing, and Applications. ASM International.
- Veiga, C., Davim, J. P., & Loureiro, A. J. R. (2012). Properties and applications of titanium alloys: A brief review. Reviews on Advanced Materials Science, 32(2), 133-148.
- Inagaki, I., Takechi, T., Shirai, Y., & Ariyasu, N. (2014). Application and Features of Titanium for the Aerospace Industry. Nippon Steel & Sumitomo Metal Technical Report, 106, 22-27.